How AI is Improving Energy Efficiency in Industrial Operations: Forget clunky, outdated systems – the future of industrial energy is smart, and it’s powered by AI. From predicting equipment failures to optimizing entire production lines, artificial intelligence is revolutionizing how we approach energy consumption. This isn’t just about saving a few bucks; it’s about building a more sustainable and efficient industrial landscape, one algorithm at a time. We’re diving deep into how AI is transforming energy management across various sectors, revealing the surprising ways it’s slashing costs and boosting sustainability.
This deep dive explores how AI-powered predictive maintenance minimizes downtime, AI-driven process control optimizes energy use in real-time, and AI-enhanced energy management systems offer unprecedented control and efficiency. We’ll also uncover the potential of AI in smart grid integration and building automation, showcasing real-world examples and highlighting the key technologies driving this transformation. Get ready to witness the future of industrial energy – it’s smarter than you think.
AI-Driven Predictive Maintenance in Industrial Energy Systems: How AI Is Improving Energy Efficiency In Industrial Operations
Predictive maintenance, powered by artificial intelligence, is revolutionizing how industries manage their energy consumption and reduce operational costs. By leveraging machine learning algorithms, businesses can anticipate equipment failures before they occur, minimizing costly downtime and preventing significant energy waste. This proactive approach not only saves money but also contributes to a more sustainable and efficient industrial landscape.
AI algorithms analyze vast amounts of data from various sensors and equipment monitoring systems to identify patterns and anomalies that indicate potential problems. This data can include vibration levels, temperature fluctuations, pressure readings, and energy consumption patterns. Sophisticated machine learning models, such as deep learning and time series analysis, are trained on historical data to predict the likelihood of equipment failure with remarkable accuracy. This allows for timely interventions, such as scheduled maintenance or component replacement, preventing catastrophic failures that lead to extended downtime and significant energy losses.
AI-Powered Predictive Maintenance Tools in Industrial Sectors
The application of AI in predictive maintenance spans various industries. In manufacturing, AI-powered systems monitor the performance of production equipment, predicting potential breakdowns in robotic arms, conveyor belts, or CNC machines. Early detection of impending failures prevents production halts, thereby saving energy that would otherwise be wasted during downtime. Similarly, in the oil and gas sector, AI algorithms analyze data from pipelines, pumps, and compressors to anticipate leaks or malfunctions. This prevents significant energy loss from leaks and ensures the continued efficient operation of critical infrastructure. The power generation sector also benefits, with AI predicting failures in turbines, generators, and transformers, optimizing maintenance schedules and minimizing energy disruptions. Furthermore, in the transportation sector, AI helps predict potential failures in railway systems and optimize energy consumption in trains, thereby contributing to significant energy savings.
Energy Savings Comparison: Predictive vs. Reactive Maintenance
The following table illustrates the potential energy savings achieved by implementing predictive maintenance strategies compared to traditional reactive maintenance approaches. These figures are based on industry studies and real-world case examples, demonstrating the significant potential for energy efficiency improvements. Note that actual savings can vary depending on factors such as the specific industry, equipment type, and the sophistication of the AI system implemented.
Industry Sector | Reactive Maintenance Energy Loss (%) | Predictive Maintenance Energy Savings (%) | Cost Savings |
---|---|---|---|
Manufacturing | 5-15% | 10-25% | Reduced downtime costs, lower repair expenses, optimized energy usage leading to significant annual cost savings. For example, a large manufacturing plant might see savings in the hundreds of thousands of dollars annually. |
Oil & Gas | 8-20% | 15-30% | Prevention of major leaks and equipment failures resulting in substantial cost savings. A single major pipeline failure can cost millions in repairs and lost production, not to mention environmental damage. |
Power Generation | 7-18% | 12-28% | Minimized energy disruptions and increased plant efficiency, leading to considerable cost savings. A power plant avoiding a major outage can save millions in lost revenue and repair costs. |
Transportation (Rail) | 3-10% | 5-15% | Improved train efficiency and reduced delays, leading to energy savings and improved operational efficiency. This translates to reduced fuel consumption and maintenance costs. |
Optimizing Energy Consumption through AI-Powered Process Control
AI is revolutionizing industrial energy efficiency, moving beyond simple predictive maintenance to actively optimize energy consumption in real-time. This dynamic approach leverages the power of artificial intelligence to fine-tune industrial processes, resulting in significant cost savings and reduced environmental impact. By analyzing vast amounts of data from various sensors and control systems, AI algorithms can identify patterns and inefficiencies invisible to human operators, leading to optimized energy use and improved overall productivity.
AI-powered process control systems are transforming how industries manage energy consumption. These systems continuously monitor operational parameters, identify deviations from optimal performance, and automatically adjust control variables to minimize energy waste. This continuous optimization, impossible to achieve through traditional methods, leads to substantial energy savings and a more sustainable operational model. The implementation of these systems varies depending on the specific industry and process, but the underlying principle remains the same: using AI to make real-time adjustments for optimal energy efficiency.
AI Algorithms for Process Optimization
The effectiveness of AI-powered process control relies heavily on the choice of appropriate algorithms. Different algorithms excel in different scenarios, and selecting the right one is crucial for achieving optimal results. Here’s a breakdown of some key algorithms used in this field:
- Reinforcement Learning (RL): RL algorithms learn through trial and error, interacting with the environment (the industrial process) and receiving rewards for actions that improve energy efficiency. This iterative process allows the AI to discover optimal control strategies without explicit programming. For example, in a chemical plant, an RL algorithm might learn to adjust temperature and pressure settings to maximize yield while minimizing energy consumption, learning optimal settings over time through experimentation within a safe operational range. This approach is particularly effective for complex systems with many interacting variables.
- Supervised Learning: Supervised learning uses labeled data—historical process data paired with corresponding energy consumption—to train a model that predicts energy usage under different operating conditions. This model can then be used to optimize control parameters in real-time. Imagine a steel mill using historical data on furnace temperature, material flow, and energy usage. A supervised learning model trained on this data can predict energy consumption for given operating conditions and suggest adjustments to minimize energy waste. This method is effective when sufficient high-quality historical data is available.
Case Studies: Real-World Applications of AI-Powered Process Control
Several industries have already successfully implemented AI-powered process control systems, resulting in significant energy savings.
- Cement Manufacturing: A cement plant implemented an AI-powered system to optimize its kiln operations. By analyzing real-time data on fuel consumption, temperature, and material flow, the AI system was able to reduce fuel consumption by 15% without impacting production output. The AI continuously adjusted parameters such as fuel feed rate and air flow based on the dynamic changes in the kiln’s operating conditions.
- Data Center Cooling: Data centers consume massive amounts of energy, largely for cooling. AI-powered systems are now used to dynamically adjust cooling systems based on real-time data from temperature sensors, server load, and weather conditions. This dynamic approach reduces energy waste by optimizing cooling only when and where needed, resulting in significant energy savings and reduced operational costs. For example, one data center reported a 20% reduction in cooling energy consumption after implementing an AI-powered control system.
AI-Enhanced Energy Management Systems in Industrial Facilities
Industrial energy management is undergoing a massive transformation, fueled by the increasing adoption of artificial intelligence. AI-enhanced Energy Management Systems (EMS) are no longer a futuristic concept; they’re actively reshaping how industrial facilities optimize their energy consumption, leading to significant cost savings and environmental benefits. These systems leverage the power of machine learning and data analytics to provide a level of efficiency and control previously unattainable.
AI-enhanced EMS go beyond traditional systems by incorporating sophisticated algorithms that analyze vast amounts of data from various sources within the facility. This allows for real-time monitoring, predictive analytics, and automated adjustments to optimize energy usage across different processes and equipment. The result is a more responsive, intelligent, and ultimately more efficient energy management strategy.
Functionalities of an AI-Enhanced Energy Management System
An AI-enhanced EMS boasts a range of functionalities designed to maximize energy efficiency and minimize waste. These systems typically integrate data from various sources, including smart meters, building management systems (BMS), and production equipment sensors. This integrated data forms the basis for intelligent decision-making. Key functionalities include real-time energy consumption monitoring, predictive maintenance scheduling based on equipment energy usage patterns, automated control of HVAC systems based on occupancy and weather forecasts, and optimization of energy production from renewable sources. For instance, an AI-powered EMS might dynamically adjust the operation of a combined heat and power (CHP) plant based on real-time energy demand and renewable energy generation. This dynamic optimization leads to significant improvements in overall energy efficiency.
Data Flow and Decision-Making Process in an AI-Powered EMS
Imagine a central hub receiving a constant stream of data. This is represented in the diagram below, illustrating the data flow and decision-making process within an AI-powered EMS.
Diagram: The diagram would show a central AI engine at the heart of the system. Arrows would flow into the engine from various sources: smart meters (measuring energy consumption in different areas), BMS (providing data on temperature, humidity, and other environmental factors), production equipment sensors (monitoring energy usage of individual machines), and weather data APIs (providing real-time weather information). From the AI engine, arrows would flow out to different control points: HVAC systems (adjusting temperature and ventilation), lighting systems (optimizing lighting schedules), and production equipment (adjusting operational parameters to minimize energy consumption). The AI engine would process all this data using machine learning algorithms to identify patterns, predict future energy needs, and make automated adjustments to optimize energy usage. Feedback loops would ensure continuous monitoring and refinement of the system’s performance.
Comparison of Traditional and AI-Powered EMS
Feature | Traditional EMS | AI-Powered EMS |
---|---|---|
Data Analysis | Relies on manual data analysis and predefined rules. | Utilizes machine learning algorithms for real-time data analysis and pattern recognition. |
Decision-Making | Primarily reactive; responds to detected issues. | Proactive; predicts potential problems and optimizes energy usage preemptively. |
Efficiency | Offers moderate energy savings. | Delivers significant energy savings through optimized resource allocation and predictive maintenance. |
Maintenance | Scheduled maintenance based on fixed intervals. | Predictive maintenance based on real-time equipment performance and energy usage patterns. |
Scalability | Limited scalability; difficult to adapt to changing conditions. | Highly scalable; easily adapts to changing operational requirements and data volumes. |
Integration | Limited integration capabilities. | Seamless integration with various systems and data sources. |
Leveraging AI for Smart Grid Integration in Industrial Energy Consumption
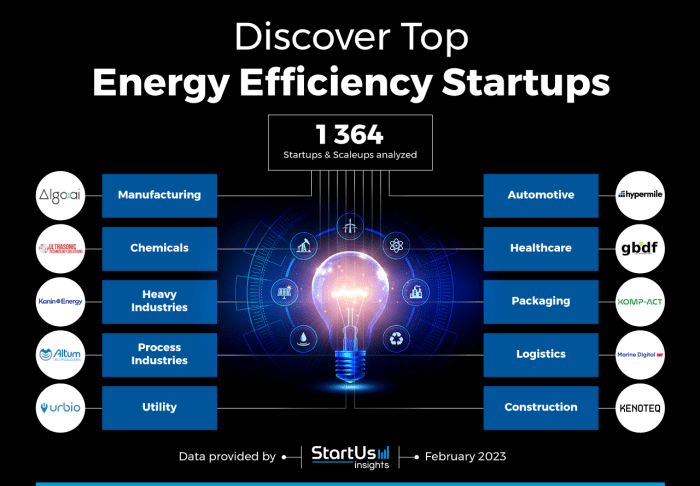
Source: startus-insights.com
Integrating industrial energy consumption into smart grids presents a complex challenge, but also unlocks significant opportunities for enhanced efficiency and sustainability. AI is emerging as a crucial tool to navigate this complexity, offering the potential to optimize energy distribution, predict demand fluctuations, and ultimately reduce operational costs and environmental impact. This section explores how AI facilitates this integration and the resulting benefits for industrial facilities.
AI significantly improves the integration of industrial energy consumption into smart grids by providing the analytical power to manage the complexities of real-time data analysis and prediction. This allows for dynamic adjustments to energy distribution, optimizing both supply and demand, and fostering a more resilient and efficient energy ecosystem. The ability to predict energy needs, anticipate disruptions, and proactively adjust operations based on real-time data makes AI an indispensable component in modern smart grid management.
AI-Driven Optimization of Energy Distribution and Demand Response
AI algorithms can analyze vast amounts of data from various sources, including industrial energy consumption patterns, weather forecasts, and grid conditions. This comprehensive analysis enables predictive modeling of energy demand, allowing for proactive adjustments to energy distribution. For example, if an AI system predicts a surge in energy demand at a specific time, it can optimize energy distribution by diverting power from less critical operations or drawing upon energy storage resources. Similarly, AI can facilitate demand response programs, encouraging industrial facilities to adjust their energy consumption based on real-time grid conditions. This could involve temporarily reducing energy-intensive processes during peak demand periods, thereby preventing grid overload and minimizing energy costs. Imagine a steel mill adjusting its furnace operations based on AI predictions of grid stress, ensuring continuous production while contributing to grid stability.
Key Benefits of AI-Driven Smart Grid Integration for Industrial Energy Efficiency, How AI is Improving Energy Efficiency in Industrial Operations
The integration of AI into smart grids offers several crucial benefits for industrial energy efficiency. These advantages extend beyond cost savings and encompass broader operational improvements and environmental responsibility.
- Reduced Energy Costs: AI-powered predictive maintenance and demand response strategies minimize energy waste and optimize energy procurement, resulting in significant cost reductions. For example, a manufacturing plant might reduce its electricity bill by 15% through AI-driven optimization of its operations during peak demand periods.
- Enhanced Grid Stability: By predicting and managing energy demand fluctuations, AI contributes to a more stable and reliable grid, reducing the risk of outages and ensuring continuous industrial operations. This stability translates to less downtime and improved productivity.
- Improved Operational Efficiency: AI optimizes energy consumption across various industrial processes, leading to streamlined operations and improved resource allocation. This can translate to increased production efficiency and reduced waste.
- Increased Sustainability: By reducing energy consumption and optimizing resource utilization, AI contributes to a more sustainable industrial landscape, reducing the carbon footprint and promoting environmental responsibility. This aligns with growing corporate sustainability goals and regulatory requirements.
AI-Based Building Automation for Industrial Energy Savings
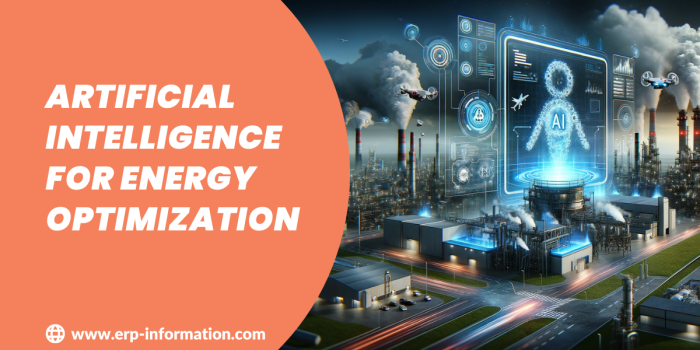
Source: erp-information.com
AI’s optimizing industrial energy use is a game-changer, slashing waste and boosting profits. This tech-driven efficiency mirrors the transformative potential of other innovative fields, like education, where immersive learning experiences are revolutionizing how we learn; check out this insightful article on The Role of Virtual Reality in Transforming Education for the Future to see how. Ultimately, both AI in industry and VR in education represent a smarter, more efficient future.
Industrial buildings, with their vast spaces and energy-intensive operations, present a significant opportunity for energy efficiency improvements. AI-based building automation systems are emerging as a powerful tool to optimize energy consumption in these facilities, leading to substantial cost savings and reduced environmental impact. By leveraging machine learning and advanced analytics, these systems can fine-tune HVAC operations, lighting schedules, and other energy-consuming processes, achieving levels of efficiency previously unattainable through traditional methods.
AI significantly enhances the efficiency of HVAC systems and lighting in industrial buildings by analyzing vast amounts of data from various sources, including temperature sensors, occupancy detectors, and weather forecasts. This data-driven approach allows for precise control and optimization of these systems, leading to significant energy savings. For example, AI can predict peak energy demand periods based on historical data and weather patterns, enabling preemptive adjustments to HVAC systems to minimize energy waste. Similarly, AI can intelligently manage lighting systems based on occupancy levels and natural light availability, ensuring that lights are only on when and where needed.
AI-Powered HVAC System Optimization
AI algorithms can analyze real-time data from various sensors within the HVAC system, including temperature, humidity, and air pressure sensors. This data is used to create a dynamic model of the building’s thermal performance, allowing for precise control of heating, ventilation, and air conditioning. For instance, an AI system might identify inefficient air circulation patterns and recommend adjustments to damper positions or fan speeds to improve energy efficiency. This level of granular control goes beyond the capabilities of traditional rule-based systems, leading to substantial reductions in energy consumption and operational costs. Consider a large manufacturing facility: By using AI-powered predictive maintenance, the facility could anticipate equipment failures and schedule repairs proactively, preventing costly downtime and energy loss. Furthermore, AI can optimize the system’s operation based on external factors like weather conditions, automatically adjusting cooling or heating based on outside temperatures.
AI-Driven Lighting Control Strategies
Intelligent lighting systems powered by AI can significantly reduce energy consumption by dynamically adjusting lighting levels based on occupancy, daylight availability, and time of day. These systems use sensors to detect occupancy in different areas of the building, automatically turning off lights in unoccupied spaces. They also incorporate daylight harvesting techniques, reducing the reliance on artificial lighting during daylight hours. For example, an AI-powered lighting system in a warehouse could automatically dim lights in areas with sufficient natural light, while maintaining adequate illumination in other areas. The system learns occupancy patterns over time, further refining its control strategies to minimize energy waste.
Adaptive Learning in AI-Based Building Automation
The ability of AI algorithms to learn and adapt to changing environmental conditions is crucial for optimizing building energy performance over time. Traditional control systems often rely on fixed rules and parameters, which may not be optimal under all circumstances. In contrast, AI systems can continuously learn from operational data, refining their control strategies to achieve greater efficiency.
AI’s adaptive learning capabilities enable it to respond effectively to unexpected events, such as sudden changes in weather patterns or occupancy levels. This dynamic adjustment ensures optimal energy performance regardless of external conditions.
Examples of AI-Powered Building Automation Systems and their Impact
Several companies offer AI-powered building automation systems that have demonstrated significant energy savings in industrial settings. One such system, deployed in a large data center, reduced energy consumption by 15% within the first year of implementation by optimizing cooling systems based on real-time data analysis and predictive maintenance. Another example involves a manufacturing plant that reduced its HVAC energy consumption by 20% through AI-driven control of its ventilation system, resulting in significant cost savings and a smaller carbon footprint. These are just a few examples illustrating the transformative potential of AI in industrial building energy management.
The Role of AI in Developing and Implementing Energy-Efficient Technologies
AI is no longer a futuristic concept; it’s actively reshaping how we approach industrial energy efficiency. Its ability to process vast datasets, identify complex patterns, and optimize systems in real-time is revolutionizing the development and implementation of energy-saving technologies. This isn’t just about tweaking existing processes; AI is fundamentally changing the design and operation of industrial energy systems.
AI accelerates the development of new energy-efficient technologies by drastically reducing the time and resources required for research and development. Traditional methods often rely on extensive experimentation and iterative refinement, a lengthy and costly process. AI, however, can simulate various scenarios, predict outcomes, and optimize designs virtually, significantly speeding up the innovation cycle. This allows engineers to explore a much wider range of possibilities and identify optimal solutions more quickly.
AI’s Contribution to Energy-Efficient Equipment Design
AI algorithms are being integrated into the design process of various industrial equipment, leading to significant energy savings. For example, in the design of electric motors, AI can optimize the geometry and magnetic properties to minimize energy losses during operation. Similarly, in the design of heat exchangers, AI can analyze fluid dynamics and heat transfer to optimize the surface area and flow patterns, maximizing efficiency. These AI-driven design optimizations often lead to equipment that consumes significantly less energy while maintaining or even improving performance. Consider the example of a large industrial fan: AI-powered design could reduce energy consumption by 15-20% compared to traditionally designed counterparts, leading to substantial cost savings over the equipment’s lifespan.
AI-Driven Optimization of Industrial Processes
Beyond equipment design, AI plays a crucial role in optimizing industrial processes to minimize energy consumption. Machine learning algorithms can analyze real-time data from sensors and control systems to identify inefficiencies and suggest improvements. For instance, in a chemical plant, AI can analyze the process parameters and optimize the temperature, pressure, and flow rates to maximize product yield while minimizing energy use. In steel manufacturing, AI can optimize the heating and cooling processes, reducing energy consumption during the production cycle. These optimizations often result in not only energy savings but also improved product quality and reduced waste. One real-world example is a cement plant that implemented AI-powered process control, resulting in a 10% reduction in energy consumption within six months.
The Future Impact of AI on Industrial Energy Efficiency
The following table illustrates the potential impact of AI on various energy-efficient technologies in industrial settings. These projections are based on current research and real-world implementations, demonstrating the transformative potential of AI in the years to come. Note that the “Time to Implementation” column reflects the time it takes to integrate AI solutions into existing systems, which varies depending on the complexity of the system and the availability of data.
Technology | Current Efficiency | AI-Enhanced Efficiency | Time to Implementation |
---|---|---|---|
Electric Motors | 85-90% | 95-98% | 1-3 years |
Heat Exchangers | 70-80% | 85-95% | 2-5 years |
HVAC Systems | 60-70% | 75-85% | 1-2 years |
Industrial Process Control | Variable, often below optimal | Significant improvement, often 10-20% reduction in energy consumption | 2-5 years |
Epilogue
The integration of AI into industrial energy management isn’t just a trend; it’s a necessity. The potential for cost savings, reduced environmental impact, and increased operational efficiency is undeniable. From predictive maintenance that prevents costly downtime to AI-powered process control that fine-tunes energy consumption, the applications are vast and the benefits are transformative. As AI algorithms continue to evolve and become more sophisticated, we can expect even greater advancements in industrial energy efficiency, paving the way for a more sustainable and prosperous future. The bottom line? AI is not just improving energy efficiency; it’s redefining it.