How AI and Automation Are Transforming Traditional Manufacturing? It’s not just about robots on assembly lines anymore. We’re talking a total overhaul, from predictive maintenance that keeps factories humming to AI-powered quality control that’s practically flawless. Think smarter supply chains, optimized production, and even new job roles emerging from this tech revolution. Get ready for a deep dive into the future of manufacturing – it’s seriously mind-blowing.
This transformation isn’t just about increased efficiency; it’s a complete shift in how we think about manufacturing. From streamlining repetitive tasks with robotic process automation to leveraging AI algorithms for better product design and predictive maintenance, the impact is profound. We’ll explore how companies are using data analytics to make real-time adjustments, improve supply chain management, and even navigate the challenges of workforce adaptation. Prepare to be amazed by the possibilities – and the potential pitfalls – of this exciting new era.
Increased Efficiency and Productivity in Manufacturing
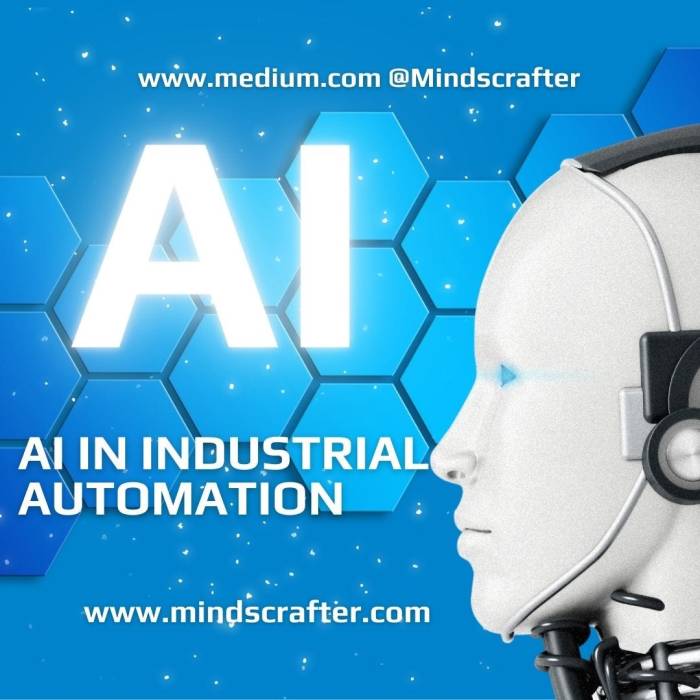
Source: medium.com
The integration of artificial intelligence (AI) and automation is revolutionizing traditional manufacturing, ushering in an era of unprecedented efficiency and productivity. No longer are factories reliant solely on human labor for repetitive tasks; instead, intelligent systems are optimizing processes, predicting potential problems, and streamlining operations in ways previously unimaginable. This leads to significant cost savings, improved product quality, and faster production cycles.
AI and automation are transforming manufacturing by boosting efficiency and productivity in several key ways. This includes leveraging predictive maintenance, automating repetitive tasks, and optimizing production lines through data analysis.
AI-Powered Predictive Maintenance, How AI and Automation Are Transforming Traditional Manufacturing
Predictive maintenance, powered by AI, analyzes real-time data from manufacturing equipment – such as vibration sensors, temperature readings, and power consumption – to predict potential failures before they occur. This allows for proactive maintenance scheduling, minimizing downtime and extending the lifespan of expensive machinery. Instead of relying on scheduled maintenance intervals (which can lead to unnecessary downtime or delayed maintenance), AI algorithms identify patterns and anomalies indicating impending failures. For example, a system might detect a slight increase in vibration in a motor, predicting a bearing failure within the next week. This early warning allows for preventative maintenance, preventing costly production halts and reducing the risk of catastrophic equipment failure. The result is significantly reduced downtime and increased equipment lifespan, translating to substantial cost savings.
Robotic Process Automation (RPA) in Manufacturing
Robotic Process Automation (RPA) plays a crucial role in streamlining repetitive tasks within manufacturing environments. These tasks, often mundane and error-prone when performed manually, are perfectly suited for automation. RPA software robots can handle tasks like data entry, invoice processing, quality control checks, and even basic assembly line operations. By automating these repetitive tasks, manufacturers free up human workers to focus on more complex and value-added activities, such as problem-solving, innovation, and strategic planning. This leads to increased overall productivity and improved worker satisfaction. For instance, a factory using RPA might automate the process of inspecting parts for defects, leading to faster and more consistent quality control.
AI-Driven Optimization of Production Lines
AI is also being used to optimize production lines in real-time. By analyzing vast amounts of data from various sources – including sensors, production schedules, and inventory levels – AI algorithms can identify bottlenecks, inefficiencies, and areas for improvement. This data-driven approach enables manufacturers to make informed decisions about resource allocation, production scheduling, and process adjustments, leading to significant gains in efficiency. For example, an AI system might identify that a particular stage in the production line is consistently causing delays. By analyzing the data, the system could suggest adjustments to the process, such as re-allocating resources or adjusting machine settings, resulting in a faster and more efficient production flow. One real-world example is a company that used AI to optimize its production line, resulting in a 15% increase in throughput and a 10% reduction in production costs.
Efficiency Gains: Traditional vs. AI-Integrated Manufacturing
The following table compares the efficiency gains achieved by integrating AI and automation into manufacturing processes across three key performance indicators (KPIs):
Year | KPI | Traditional | AI-Integrated |
---|---|---|---|
2022 | Production Downtime (Hours/Month) | 150 | 75 |
2022 | Defect Rate (%) | 5 | 2 |
2022 | Production Output (Units/Hour) | 100 | 120 |
Enhanced Quality Control and Product Development
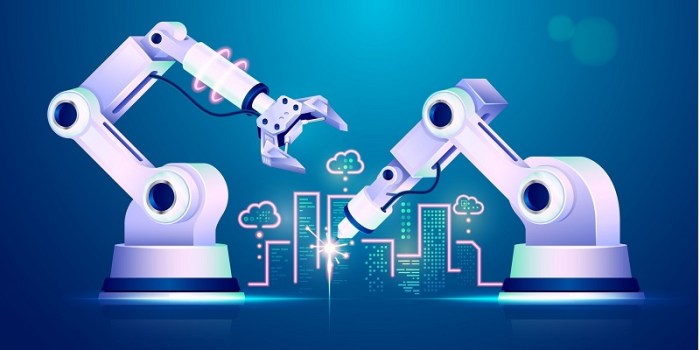
Source: spiceworks.com
AI and automation are revamping traditional manufacturing, boosting efficiency and output. But this rapid change raises crucial questions about job displacement and resource allocation, prompting a deeper look into the ethical implications of these technologies. Understanding this necessitates exploring the complex field of The Role of Artificial Intelligence in Ethical Decision Making , which is vital for responsible implementation in manufacturing and beyond, ensuring a future where technological advancement benefits all.
The integration of AI and automation is revolutionizing quality control and product development in manufacturing, moving beyond traditional methods to deliver unprecedented levels of precision and efficiency. This leap forward isn’t just about faster production; it’s about creating higher-quality products, minimizing waste, and fostering innovation. AI’s ability to analyze vast amounts of data and identify subtle patterns allows manufacturers to proactively address potential issues, optimize designs, and ultimately, deliver superior products to the market.
AI algorithms and computer vision systems are transforming how manufacturers ensure product quality. This technology goes beyond human capabilities, enabling the detection of minute flaws invisible to the naked eye and significantly reducing human error. The result? A dramatic increase in product consistency and a reduction in costly rework or product recalls.
Computer Vision in Defect Detection
Computer vision, a branch of AI that allows computers to “see” and interpret images, plays a crucial role in automated quality control. Cameras equipped with sophisticated algorithms inspect products at various stages of the manufacturing process, identifying defects such as scratches, dents, cracks, or inconsistencies in color or texture. This real-time feedback enables immediate corrective actions, preventing flawed products from progressing further down the production line. For example, in the automotive industry, computer vision systems are used to inspect car bodies for paint imperfections or misaligned parts, ensuring a consistently high-quality finish. Similarly, in food processing, computer vision can detect blemishes on fruits and vegetables, sorting out imperfect produce for alternative uses.
AI-Driven Analysis for Product Design Improvement
AI algorithms can analyze massive datasets of manufacturing data—including production parameters, defect rates, customer feedback, and market trends—to identify patterns and insights that are difficult, if not impossible, for humans to discern. This data-driven approach enables manufacturers to refine their product designs, optimize production processes, and predict potential problems before they arise. For instance, analyzing historical data on product failures can reveal underlying design weaknesses, leading to improved product durability and reliability. Predictive maintenance models, powered by AI, can anticipate equipment failures, minimizing downtime and preventing costly disruptions to the production process.
Examples of AI-Powered Quality Control Systems
Several manufacturing sectors are already leveraging AI-powered quality control systems. In the electronics industry, AI algorithms are used to inspect circuit boards for faulty components or soldering defects. The textile industry utilizes computer vision to assess fabric quality, detecting imperfections such as weaving errors or inconsistencies in color. Pharmaceutical companies employ AI-powered systems to ensure the consistency and purity of medications, detecting contaminants or variations in dosage. These are just a few examples of how AI is transforming quality control across various industries.
AI-Driven Quality Control Process Flowchart
Imagine a flowchart depicting the process:
1. Raw Material Inspection: Computer vision systems analyze incoming raw materials for defects and inconsistencies.
2. In-Process Inspection: Automated systems monitor the production process at various stages, detecting defects in real-time.
3. Defect Classification: AI algorithms classify detected defects based on their type and severity.
4. Corrective Actions: The system triggers corrective actions, such as adjusting machine settings or rejecting defective products.
5. Final Product Verification: A final inspection verifies the quality of the finished product before packaging and shipment.
6. Data Analysis and Improvement: Data collected throughout the process is analyzed to identify trends and improve the overall quality control process. This feedback loop constantly refines the system’s accuracy and efficiency.
This iterative process ensures continuous improvement and enhances the overall quality of the final product.
Improved Supply Chain Management and Logistics
Forget the days of relying on gut feelings and spreadsheets for supply chain management. AI is revolutionizing how manufacturers track, predict, and optimize their entire supply chain, from raw materials to finished goods. This translates to significant cost savings, reduced waste, and a more agile and responsive business. Let’s explore how AI is making this happen.
AI optimizes inventory management and reduces waste by leveraging predictive analytics and machine learning algorithms. Traditional methods often relied on historical data and safety stock estimations, leading to overstocking or stockouts. AI, however, can analyze a far wider range of data – including real-time sales figures, weather patterns, economic indicators, and even social media trends – to create highly accurate demand forecasts. This enables manufacturers to order precisely the amount of materials needed, minimizing storage costs and reducing the risk of obsolescence.
AI-Powered Demand Forecasting and its Impact on Production Planning
AI-driven demand forecasting leverages sophisticated algorithms to analyze vast datasets and predict future demand with greater accuracy than traditional methods. For instance, a company producing seasonal clothing might use AI to predict demand for specific items based on historical sales, weather forecasts, and social media trends related to fashion. This allows them to adjust their production schedules, ensuring they have the right products available at the right time, preventing overproduction or stockouts. Imagine a scenario where a traditional forecasting model predicted a 10% increase in demand, leading to a 10% increase in production. An AI model, however, might predict a 15% increase in demand for one specific item and a 5% decrease in demand for another, leading to a much more efficient and profitable production plan. This level of granularity is impossible to achieve with traditional methods.
Benefits of AI in Logistics
The benefits of AI extend beyond inventory management. AI is significantly improving logistics operations through several key areas:
- Route Optimization: AI algorithms analyze real-time traffic data, road closures, and other factors to determine the most efficient delivery routes, reducing transportation costs and delivery times. This is particularly beneficial for companies with large fleets of vehicles or complex distribution networks.
- Autonomous Delivery Systems: The use of autonomous vehicles, drones, and robots is transforming last-mile delivery. These systems can operate 24/7, reducing reliance on human drivers and improving delivery speed and efficiency. Imagine a factory using autonomous drones to deliver urgent parts to a production line, preventing costly downtime.
- Predictive Maintenance: AI can monitor the condition of vehicles and equipment, predicting potential failures and scheduling maintenance before breakdowns occur. This minimizes downtime and reduces repair costs.
- Warehouse Automation: AI-powered robots and automated guided vehicles (AGVs) are streamlining warehouse operations, improving efficiency and reducing labor costs. These systems can automate tasks such as picking, packing, and transporting goods.
Comparison of Traditional and AI-Powered Supply Chain Management
Traditional supply chain management often relies on manual processes, historical data, and basic forecasting models. This approach is often reactive, struggling to adapt to unexpected changes in demand or supply. In contrast, AI-powered solutions are proactive, leveraging real-time data, predictive analytics, and machine learning to optimize every stage of the supply chain. This leads to greater agility, resilience, and efficiency. For example, a traditional approach might struggle to respond to a sudden surge in demand, leading to stockouts or delays. An AI-powered system, however, could quickly adjust production schedules, optimize delivery routes, and even re-route shipments to meet the increased demand. The result is a more responsive and customer-centric supply chain.
The Impact of Automation on the Manufacturing Workforce: How AI And Automation Are Transforming Traditional Manufacturing
The rise of AI and automation in manufacturing is undeniably reshaping the landscape of employment. While boosting efficiency and productivity, it also presents significant challenges and opportunities for the workforce. Understanding these shifts is crucial for navigating the transition and ensuring a smooth integration of technology into the manufacturing sector. This section explores the impact of automation on jobs, focusing on displacement, new roles, necessary skill shifts, and projected employment changes.
Automation’s impact on manufacturing jobs is a complex issue, often painted in stark terms of job losses versus gains. The reality is more nuanced, involving both displacement and the creation of new, higher-skilled positions. While some traditional roles will inevitably decline, the overall impact depends significantly on proactive strategies for workforce adaptation and the development of new skills.
Job Displacement and Reskilling/Upskilling Strategies
The introduction of robots and AI-powered systems can lead to the displacement of workers in roles easily automated, such as assembly line tasks or repetitive manual processes. However, this doesn’t mean the end of manufacturing jobs. Instead, it signifies a shift towards a workforce requiring different skills. Effective reskilling and upskilling initiatives are vital to mitigate job losses and prepare workers for the new roles emerging in the industry. Successful strategies involve collaborations between employers, educational institutions, and government agencies to provide training programs focusing on areas like robotics maintenance, AI programming, data analysis, and advanced manufacturing techniques. For instance, Germany’s “Industry 4.0” initiative emphasizes apprenticeships and continuous learning to equip workers with the skills needed for the digitalized manufacturing environment. Similarly, initiatives in the US, like those funded through the Department of Labor, focus on providing grants and support for retraining programs in advanced manufacturing technologies.
New Job Roles and Opportunities in AI-Driven Manufacturing
The integration of AI and automation creates a demand for new roles that require specialized skills. These include AI specialists, data scientists, robotics engineers, cybersecurity experts, and technicians skilled in maintaining and troubleshooting automated systems. These roles often involve higher levels of education and specialized training, offering higher earning potential and greater job security. The development and implementation of sophisticated manufacturing systems, predictive maintenance using AI, and the analysis of vast datasets from smart factories all create a need for professionals with expertise in these areas. For example, the growing field of digital twin technology, which uses virtual representations of physical assets, necessitates specialists capable of designing, managing, and interpreting data from these complex systems.
Skillset Comparison: Traditional vs. AI-Integrated Manufacturing
Traditional manufacturing jobs often emphasize manual dexterity, repetitive tasks, and basic technical skills. AI-integrated roles, however, require a different skillset. They demand proficiency in programming, data analysis, problem-solving, critical thinking, and the ability to work with complex technological systems. While some basic mechanical skills remain relevant, the focus shifts towards digital literacy, analytical abilities, and the capacity to manage and interpret data from automated systems. This transition requires a significant investment in education and training to bridge the gap between the existing workforce and the needs of the evolving manufacturing landscape. A clear example of this shift is the increasing demand for workers skilled in using and maintaining collaborative robots (cobots), which require a blend of technical expertise and an understanding of human-robot interaction.
Projected Changes in Manufacturing Employment
The following table presents projected changes in employment across different manufacturing job categories, based on current trends and expert predictions. These projections are illustrative and subject to variations depending on technological advancements, economic conditions, and government policies. Note that these are hypothetical examples and do not represent specific, verifiable data from a single source.
Job Category | Current Employment (hypothetical) | Projected Employment (5 years) (hypothetical) | Projected Employment (10 years) (hypothetical) |
---|---|---|---|
Assembly Line Workers | 100,000 | 80,000 | 60,000 |
Robotics Technicians | 5,000 | 15,000 | 30,000 |
Data Analysts | 2,000 | 8,000 | 20,000 |
Quality Control Specialists (AI-assisted) | 10,000 | 12,000 | 15,000 |
Data Analytics and Insights in Manufacturing
The marriage of AI and manufacturing is producing a data deluge, offering unprecedented opportunities for optimization and growth. AI-powered analytics are no longer a futuristic concept; they’re transforming how factories operate, from streamlining production lines to predicting equipment failures. This allows manufacturers to move beyond reactive problem-solving and embrace proactive strategies for continuous improvement.
The ability to analyze vast amounts of manufacturing data is revolutionizing decision-making processes. AI and machine learning algorithms sift through this data, uncovering hidden patterns and insights that would be impossible for humans to detect manually. This leads to significant improvements in efficiency, quality, and overall profitability.
Data Collection and Analysis in AI-Driven Manufacturing
AI-driven manufacturing environments collect a wide variety of data from various sources. This includes data from sensors embedded in machines, capturing real-time information on performance, energy consumption, and potential malfunctions. Production data, such as cycle times, defect rates, and output volumes, is also crucial. Further, supplier data, inventory levels, and customer demand forecasts contribute to a holistic picture. Sophisticated algorithms then analyze this data to identify correlations, predict trends, and ultimately optimize processes. For example, machine learning models can analyze sensor data to predict when a machine is likely to fail, allowing for preventative maintenance and minimizing downtime.
Real-Time Data Analysis and Production Adjustments
Real-time data analysis empowers manufacturers to make immediate adjustments to production processes based on current conditions. Imagine a bottling plant using sensors to monitor fill levels. If a sensor detects a consistently low fill level, the system can automatically adjust the filling mechanism, preventing underfilling and product waste. Similarly, AI can identify bottlenecks in the production line by analyzing real-time data on machine performance and material flow. This allows for immediate intervention, preventing delays and ensuring consistent output.
Data Visualization and Decision-Making
Effective data visualization is key to translating complex data into actionable insights. A well-designed dashboard can provide manufacturers with a clear and concise overview of key performance indicators (KPIs). For instance, a dashboard might display real-time data on production output, defect rates, machine uptime, and inventory levels. Visual representations, such as charts and graphs, allow manufacturers to quickly identify trends, anomalies, and areas requiring attention. For example, a sudden spike in defect rates might highlight a problem with a specific machine or process, prompting an immediate investigation and corrective action. A hypothetical dashboard could show a geographical heatmap of machine failures, instantly pinpointing problem areas within the factory floor, enabling targeted maintenance efforts. This visual representation, compared to simply looking at raw data, offers an immediate, intuitive understanding of complex operational patterns.
Challenges and Considerations in AI Adoption
Integrating AI and automation into manufacturing isn’t a simple plug-and-play operation. It requires careful planning, substantial investment, and a willingness to navigate a complex landscape of technological, operational, and human factors. Success hinges on understanding and proactively addressing the inherent challenges.
Data Security and Privacy in AI-Driven Manufacturing
The increasing reliance on data in AI-powered manufacturing systems necessitates robust security measures. Manufacturing processes often involve sensitive information, including proprietary designs, production data, and potentially customer data. Breaches can lead to significant financial losses, reputational damage, and legal repercussions. Implementing comprehensive cybersecurity protocols, including data encryption, access control, and regular security audits, is crucial. Furthermore, adherence to data privacy regulations like GDPR and CCPA is paramount to maintain customer trust and avoid penalties. A layered approach to security, encompassing both physical and digital safeguards, is essential to protect valuable data and ensure the integrity of AI-driven operations.
Infrastructure Requirements for AI in Manufacturing
Successfully deploying AI in manufacturing demands significant investment in robust infrastructure. This includes high-speed internet connectivity to facilitate real-time data transfer and analysis, powerful computing resources to handle large datasets and complex algorithms, and advanced automation systems capable of integrating with AI applications. Legacy systems often present compatibility challenges, requiring upgrades or replacements to ensure seamless integration with new AI technologies. The cost of this infrastructure upgrade can be substantial, requiring careful planning and budgeting to avoid unforeseen expenses. For example, a small-to-medium-sized enterprise (SME) might need to invest in cloud computing services to access the necessary processing power without significant upfront capital expenditure.
Skilled Workforce for AI Implementation and Maintenance
AI implementation in manufacturing requires a skilled workforce capable of designing, implementing, and maintaining AI systems. This necessitates training existing employees in new technologies and potentially recruiting individuals with specialized AI expertise. The shortage of skilled data scientists, AI engineers, and cybersecurity professionals can hinder successful AI adoption. Companies need to invest in employee training programs, partnerships with educational institutions, and proactive recruitment strategies to address this skills gap. Furthermore, fostering a culture of continuous learning and adaptation is vital to ensure the workforce can keep pace with the rapid advancements in AI technology. Investing in upskilling initiatives could involve sponsoring employees to attend relevant workshops or pursuing advanced degrees in data science or AI.
Examples of Successful and Unsuccessful AI Implementations
A successful example is Fanuc, a leading robotics company, which utilizes AI-powered predictive maintenance to minimize downtime in its manufacturing facilities. By analyzing sensor data from machines, Fanuc’s AI system can predict potential failures and schedule maintenance proactively, leading to increased efficiency and reduced costs. Conversely, an unsuccessful example might involve a company that hastily implemented an AI-powered quality control system without adequately training its employees or considering the potential for integration issues with existing systems. This resulted in inaccurate predictions, operational disruptions, and ultimately, the abandonment of the AI system. The key difference lies in thorough planning, realistic expectations, and a commitment to ongoing support and training.
Closure
The integration of AI and automation in traditional manufacturing is undeniably reshaping the industry, boosting efficiency, and driving innovation at an unprecedented pace. While challenges exist, particularly concerning workforce adaptation and data security, the potential benefits are too significant to ignore. The future of manufacturing is intelligent, automated, and undeniably exciting – and it’s happening now.