How AI and Automation Are Redefining the Manufacturing Industry: Forget clunky assembly lines; the future of factories is here, and it’s smarter than ever. We’re talking AI-powered robots collaborating with human workers, predictive maintenance eliminating downtime, and customized products rolling off the line at lightning speed. This isn’t just about efficiency; it’s a complete overhaul, reshaping the industry from the ground up, impacting everything from supply chains to the skills needed for the jobs of tomorrow. Get ready to explore the exciting – and sometimes unsettling – changes sweeping through the world of manufacturing.
From optimizing inventory with AI algorithms to using machine learning to catch defects before they even happen, the impact is undeniable. This shift isn’t just about technological advancements; it’s about adapting to a new paradigm where humans and machines work in concert, creating a more efficient, innovative, and responsive manufacturing landscape. We’ll delve into the specific ways AI and automation are transforming every aspect of this vital industry, from the factory floor to the boardroom, exploring both the incredible opportunities and the challenges that lie ahead.
Increased Efficiency and Productivity
The manufacturing landscape is undergoing a dramatic shift, driven by the convergence of artificial intelligence (AI) and automation. This revolution isn’t just about faster production; it’s about fundamentally redefining efficiency and productivity, leading to significant cost savings and improved product quality. This section explores how AI and automation are achieving these gains.
AI and automation are reshaping manufacturing processes, resulting in higher output, reduced waste, and improved overall efficiency. The integration of these technologies is not merely additive; it’s transformative, creating a synergistic effect that surpasses the sum of its parts. Let’s delve into specific examples.
AI and automation are seriously shaking up manufacturing, boosting efficiency and productivity like never before. This revolution is largely fueled by innovative tech startups, whose impact on the global economy is undeniable, as detailed in this insightful article: The Impact of Tech Startups on the Global Economy. Ultimately, these startups are key players in shaping the future of manufacturing, driving further advancements in AI-powered solutions.
AI-Powered Predictive Maintenance Reduces Downtime
Predictive maintenance, powered by AI and machine learning algorithms, analyzes sensor data from equipment to anticipate potential failures. Instead of relying on scheduled maintenance (which can be unnecessarily frequent or infrequent), AI systems identify patterns indicating impending malfunctions. This allows for proactive repairs, minimizing unexpected downtime and maximizing equipment lifespan. For example, a factory using AI-powered predictive maintenance on its assembly line robots might predict a motor failure a week in advance, allowing for a scheduled replacement during a low-production period, preventing costly production halts. This contrasts sharply with reactive maintenance, where failures cause immediate production disruptions and potentially damage other components.
Robotic Process Automation Streamlines Repetitive Tasks
Robotic Process Automation (RPA) excels at automating repetitive, rule-based tasks. In manufacturing, this translates to significant efficiency gains in areas like data entry, order processing, and inventory management. RPA bots can handle these tasks tirelessly and accurately, freeing up human workers to focus on more complex and value-added activities. Consider a scenario where a factory uses RPA to automatically update inventory levels based on real-time production data. This eliminates manual data entry errors, reduces the risk of stockouts or overstocking, and improves overall supply chain efficiency.
AI-Driven Quality Control Versus Traditional Methods
Traditional quality control methods often rely on manual inspection, which is time-consuming, prone to human error, and can be inconsistent. AI-driven quality control leverages computer vision and machine learning to analyze images and data, identifying defects with far greater speed and accuracy. This leads to improved product quality, reduced waste, and enhanced customer satisfaction.
Metric | Traditional Methods | AI-Driven Methods |
---|---|---|
Speed | Slow, dependent on human inspection rate | Fast, near real-time analysis |
Accuracy | Prone to human error and inconsistency | High accuracy, consistent detection |
Cost | High labor costs, potential for rework and waste | High initial investment, but lower long-term costs due to reduced waste and improved efficiency |
Enhanced Product Quality and Innovation
AI and automation aren’t just about speeding up manufacturing; they’re fundamentally changing the quality and innovation landscape. By leveraging the power of data analysis and predictive modeling, manufacturers are creating better products, faster, and with fewer defects. This translates to increased customer satisfaction, stronger brand reputation, and a significant competitive edge in today’s market.
AI algorithms are revolutionizing the way products are designed and developed. Instead of relying solely on human intuition and experience, manufacturers can now use sophisticated software to simulate product performance, optimize designs for strength and efficiency, and even predict potential failures before they occur. This allows for faster iteration cycles, reduced prototyping costs, and the creation of products that are both innovative and robust.
AI-Driven Product Design and Development
AI-powered design tools use machine learning algorithms to analyze vast datasets of existing product designs, material properties, and manufacturing processes. This allows them to identify optimal design parameters, predict the performance of different materials, and suggest improvements based on past successes and failures. For example, an AI system could analyze thousands of previous designs for a car part, identifying the optimal combination of materials and geometry to maximize strength while minimizing weight. This leads to lighter, more fuel-efficient vehicles, and a reduction in manufacturing costs. Furthermore, generative design algorithms can explore a much wider range of design possibilities than a human engineer could ever manage, leading to truly innovative product solutions. Imagine an AI designing a completely new type of bicycle frame with unprecedented strength-to-weight ratio, a feat that would have been impossible using traditional methods.
Machine Learning for Defect Prevention
Machine learning plays a crucial role in identifying and preventing defects during the manufacturing process. By analyzing data from sensors and cameras on the factory floor, AI systems can detect anomalies in real-time, such as variations in temperature, pressure, or material properties, that might indicate a potential defect. This allows for immediate corrective action, preventing defective products from reaching the customer and minimizing waste. For instance, a machine learning model trained on images of manufactured circuit boards can identify microscopic flaws that are invisible to the human eye, preventing the shipment of faulty products. This proactive approach to quality control not only improves product quality but also significantly reduces production costs associated with rework, scrap, and warranty claims.
AI-Enabled Product Personalization
AI is also enabling the creation of customized and personalized products at scale. By analyzing customer data and preferences, manufacturers can tailor products to meet individual needs and desires. This could range from personalized clothing and footwear to customized medical devices and even bespoke furniture. For example, a company manufacturing hearing aids might use AI to analyze a customer’s hearing profile and automatically generate a personalized design and fitting. This level of customization enhances customer satisfaction and loyalty, while also creating new market opportunities for manufacturers. The ability to offer highly personalized products, previously limited to niche markets, is now within reach for a much broader range of industries, thanks to AI-driven manufacturing processes.
Improved Supply Chain Management
The manufacturing industry’s intricate web of suppliers, logistics, and inventory is being radically reshaped by AI and automation. No longer are supply chains reactive behemoths; they’re transforming into intelligent, self-optimizing systems capable of predicting and mitigating disruptions, leading to significant cost savings and increased resilience. This evolution hinges on the power of AI to analyze massive datasets, identify patterns, and make data-driven decisions that were previously impossible.
AI’s role in optimizing inventory management and logistics is multifaceted. It moves beyond simple forecasting to provide a dynamic, real-time view of the entire supply chain. This allows manufacturers to optimize stock levels, reducing warehousing costs and minimizing the risk of stockouts or overstocking. The integration of AI-powered systems with existing Enterprise Resource Planning (ERP) software provides a seamless flow of information, enhancing visibility and control.
AI-Powered Inventory Optimization and Logistics
AI algorithms, particularly machine learning models, can analyze historical sales data, seasonal trends, and even external factors like weather patterns and economic indicators to predict future demand with remarkable accuracy. This predictive capability allows manufacturers to adjust production schedules and optimize inventory levels proactively, reducing waste and improving efficiency. For instance, a clothing manufacturer might use AI to predict spikes in demand for specific items during promotional periods, ensuring sufficient stock is available to meet customer demand without overstocking slower-moving items. This dynamic adjustment minimizes storage costs and prevents potential losses due to obsolete inventory. Furthermore, AI can optimize logistics by identifying the most efficient routes for transportation, considering factors such as traffic conditions, fuel costs, and delivery deadlines. This results in faster delivery times and reduced transportation expenses.
Predictive AI for Supply Chain Disruptions and Mitigation
Predictive AI models, trained on vast datasets encompassing everything from supplier performance to geopolitical events, can identify potential supply chain disruptions with considerable lead time. These models can analyze various data points, such as supplier lead times, transportation delays, and natural disaster predictions, to assess the risk of disruptions. For example, an AI system might predict a potential shortage of a critical component due to a political instability in a key supplier’s region. This allows the manufacturer to proactively seek alternative suppliers, negotiate contracts with existing suppliers for increased production, or even explore alternative component designs to mitigate the potential impact. The system could then suggest mitigation strategies, such as diversifying sourcing, building safety stock, or implementing alternative transportation routes. This proactive approach minimizes the impact of unforeseen events and maintains production continuity.
AI-Enhanced Supplier Relationships and Collaboration
AI facilitates improved communication and collaboration across the entire supply chain. AI-powered platforms can automate tasks like order management, invoice processing, and performance tracking, streamlining communication and reducing administrative overhead. This increased transparency fosters stronger relationships with suppliers, as both parties have access to real-time data regarding performance and potential issues. For example, an AI system could automatically alert a manufacturer to a potential delay in a supplier’s delivery, allowing for prompt communication and collaborative problem-solving. Furthermore, AI can analyze supplier performance data to identify reliable and high-performing partners, aiding in supplier selection and relationship management. This ensures that manufacturers are working with partners who consistently meet their expectations, leading to a more stable and reliable supply chain.
Reshaping the Manufacturing Workforce
The rise of AI and automation in manufacturing isn’t just about faster machines; it’s a complete overhaul of the workforce. It demands a shift from manual labor to a more collaborative human-machine partnership, requiring a significant upskilling and reskilling initiative. This transformation presents both challenges and exciting opportunities for workers, opening doors to new, higher-skilled roles and a more fulfilling work experience.
The integration of AI and automation necessitates a workforce equipped with new skills and adapted to new roles. This isn’t about robots replacing humans; it’s about humans and robots working together to achieve greater efficiency and productivity. This collaborative model requires a fundamental shift in training and education to ensure a smooth transition and prevent a skills gap.
New Skills and Roles in AI-Driven Manufacturing
The demand for traditional manufacturing jobs might decrease, but simultaneously, a surge in specialized roles will emerge. These roles require a blend of technical expertise and soft skills, emphasizing problem-solving, critical thinking, and collaboration. For example, roles like AI/machine learning specialists, robotics technicians, data analysts, and cybersecurity experts will become increasingly crucial. These professionals will not only operate and maintain the advanced machinery but also program, troubleshoot, and optimize AI systems, ensuring seamless integration within the manufacturing process. Furthermore, roles focusing on human-robot collaboration, such as collaborative robot (cobot) programmers and trainers, will be essential to bridge the gap between human workers and automated systems.
Augmenting Human Capabilities Through Human-Machine Collaboration
AI and automation aren’t meant to replace human workers; they’re designed to augment their capabilities. Imagine a scenario where a human worker, equipped with a smart wearable device, receives real-time data analysis from sensors on a robotic arm performing a complex welding task. The AI system detects a potential flaw, alerting the worker to adjust the robotic arm’s trajectory slightly. This collaboration leverages the human’s problem-solving skills and experience alongside the robot’s precision and speed, resulting in a superior product and a more efficient process. This synergistic approach transforms manufacturing from a repetitive, physically demanding task into a more intellectually stimulating and collaborative endeavor. In other words, humans handle the complex, adaptive tasks requiring judgment and creativity, while machines handle the repetitive, high-precision tasks.
Retraining Programs for Upskilling the Workforce, How AI and Automation Are Redefining the Manufacturing Industry
Addressing the skills gap requires proactive and comprehensive retraining programs. These programs should be tailored to the specific needs of the manufacturing industry and the evolving skillsets required for the AI-driven environment.
- On-the-job training programs: Companies can implement internal training programs that allow existing employees to learn new skills while continuing their work. This could involve mentoring programs with experienced technicians and engineers.
- Industry-academia partnerships: Collaborations between manufacturing companies and educational institutions can create customized training programs that bridge the gap between theoretical knowledge and practical application. This approach can involve developing specialized apprenticeships or certificate programs.
- Government-funded initiatives: Governments can play a vital role in funding and supporting retraining programs, providing financial assistance to workers and businesses. This can involve subsidies for training courses or tax incentives for companies investing in workforce development.
- Virtual and augmented reality training: Immersive technologies can create realistic simulations of manufacturing environments, allowing workers to practice operating and maintaining AI-driven machinery in a safe and controlled setting. This can greatly reduce the risk of costly errors during actual operations.
- Micro-credentialing programs: Offering shorter, specialized courses focusing on specific AI and automation-related skills allows workers to quickly acquire new competencies without having to commit to lengthy degree programs.
The Rise of Smart Factories
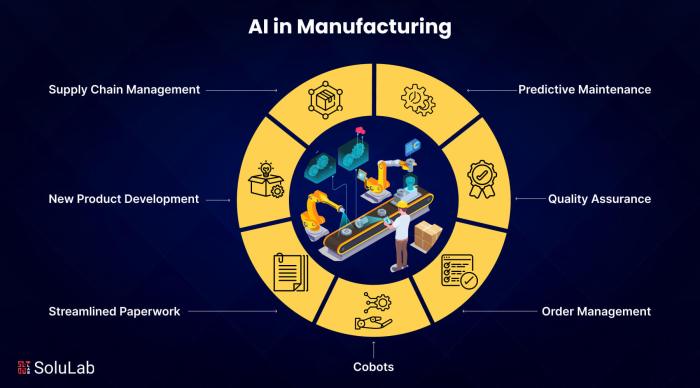
Source: solulab.com
Smart factories represent the cutting edge of manufacturing, leveraging advanced technologies to achieve unprecedented levels of efficiency, flexibility, and responsiveness. They’re not just about automating individual tasks; they’re about creating a fully integrated, intelligent system that optimizes the entire production process. This transformation is driven by the convergence of Artificial Intelligence (AI), automation, and the Internet of Things (IoT).
The core of a smart factory lies in its ability to collect, analyze, and utilize real-time data from every aspect of the production process. This data-driven approach allows for proactive adjustments, predictive maintenance, and continuous improvement, leading to significant gains in productivity and quality. AI algorithms play a crucial role in analyzing this vast amount of data, identifying patterns, predicting potential problems, and optimizing resource allocation. Automation, meanwhile, executes the optimized processes, from robotic assembly lines to automated material handling systems.
IoT Integration in Smart Factories
The Internet of Things (IoT) acts as the nervous system of a smart factory, connecting all the machines, sensors, and devices on the factory floor. These connected devices generate a constant stream of data – everything from machine performance metrics to inventory levels and environmental conditions. AI algorithms then process this data to provide valuable insights and enable intelligent decision-making. For example, sensors on a machine can detect subtle changes in vibration or temperature, indicating potential malfunctions before they lead to costly downtime. AI can analyze this data and predict when maintenance is needed, scheduling it proactively to prevent disruptions. This predictive maintenance capability significantly reduces downtime and extends the lifespan of equipment. Furthermore, IoT-connected systems can optimize material flow, ensuring that the right materials are available at the right time, minimizing waste and maximizing efficiency.
A Visual Representation of a Smart Factory Floor
Imagine a bustling factory floor, but instead of a chaotic scene of human workers struggling with manual tasks, you see a coordinated ballet of robots and automated systems working alongside human operators. Robotic arms precisely assemble components, guided by AI-powered vision systems that ensure perfect accuracy. Automated guided vehicles (AGVs) silently transport materials between workstations, optimizing the flow of goods. Large screens display real-time data on production metrics, allowing operators to monitor performance and identify potential bottlenecks. Human workers, rather than performing repetitive tasks, are focused on higher-level activities such as quality control, programming robots, and overseeing the overall production process. They interact with the system through intuitive interfaces, providing feedback and making adjustments as needed. The floor itself is smart, with embedded sensors monitoring environmental conditions and providing data for optimizing energy consumption and ensuring worker safety. This integrated system, seamlessly blending human expertise with advanced technology, is the hallmark of a truly smart factory. Companies like Siemens and General Electric are already implementing many of these features in their own manufacturing facilities, demonstrating the practical applications of this technology.
Addressing Ethical and Societal Implications
The integration of AI and automation in manufacturing, while promising unprecedented efficiency and innovation, necessitates a careful consideration of its ethical and societal ramifications. The transformative power of these technologies brings both incredible opportunities and potential challenges that demand proactive and responsible management. Failure to address these implications could lead to significant social and economic disruption.
The rapid advancement of AI-driven manufacturing systems presents a complex interplay of benefits and risks, particularly concerning the human element and the responsible use of data. Understanding and mitigating these challenges is crucial for ensuring a just and equitable transition to a more automated future.
Impact of Automation on Employment
Automation’s impact on employment in manufacturing is a significant concern. While some roles will be automated, leading to job displacement, new roles requiring different skill sets will also emerge. For example, the demand for data scientists, AI specialists, and robotics engineers is likely to increase. However, the transition requires proactive measures such as retraining and upskilling programs to help displaced workers adapt to the changing job market. This requires collaboration between governments, industries, and educational institutions to ensure a smooth transition and prevent widespread unemployment. For instance, Germany’s “Industry 4.0” initiative incorporates substantial investment in workforce retraining and education to mitigate potential job losses.
Data Privacy and Security in AI-Driven Manufacturing
Data privacy and security are paramount in AI-driven manufacturing. These systems collect and process vast amounts of sensitive data, including production data, customer information, and intellectual property. Robust cybersecurity measures are essential to protect this data from unauthorized access, theft, or misuse. Implementing strong encryption protocols, access control mechanisms, and regular security audits are crucial. Moreover, compliance with data privacy regulations, such as GDPR and CCPA, is vital to build trust and maintain ethical standards. Failure to adequately protect this data could lead to significant financial losses, reputational damage, and legal repercussions. The recent cyberattacks targeting manufacturing companies highlight the urgency of prioritizing data security.
Mitigation of Bias in AI Algorithms
AI algorithms are trained on data, and if this data reflects existing societal biases, the algorithms will perpetuate and even amplify these biases. This can lead to unfair or discriminatory outcomes in manufacturing processes, such as biased quality control assessments or unfair allocation of tasks. To mitigate bias, it’s crucial to use diverse and representative datasets for training AI models. Regular audits of AI systems for bias detection and implementing fairness-aware algorithms are also necessary. Furthermore, fostering transparency and explainability in AI decision-making processes can help identify and address potential biases. For example, an algorithm trained primarily on data from one demographic group might underperform or produce inaccurate results when applied to a different group. Addressing this requires careful data curation and algorithmic design.
Case Studies of Successful AI Implementation
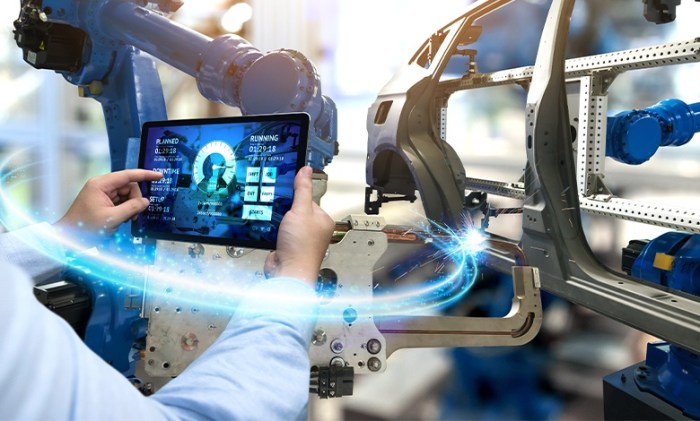
Source: connection.com
AI and automation aren’t just theoretical advancements; they’re transforming manufacturing realities. Numerous companies are reaping the benefits, proving the transformative power of these technologies. Examining successful implementations provides valuable insights for businesses considering similar strategies. These case studies highlight not only the achievements but also the challenges faced and the solutions employed.
Below, we showcase several companies that have successfully integrated AI and automation, detailing their approaches and outcomes. The table provides a concise overview, while subsequent sections delve deeper into specific challenges and solutions.
Examples of Successful AI Implementation in Manufacturing
Company Name | Industry | Implemented Technology | Results |
---|---|---|---|
GE | Aerospace, Energy | Predictive maintenance using machine learning algorithms analyzing sensor data from jet engines and power turbines. | Reduced downtime by 20%, improved operational efficiency, and extended asset lifespan. |
Siemens | Manufacturing Automation | Digital twins and AI-powered simulation for optimizing production processes and predicting potential bottlenecks. | Increased production throughput by 15%, reduced production costs, and improved product quality. |
Bosch | Automotive, Industrial Technology | AI-powered quality control systems using computer vision to detect defects in manufacturing processes. | Significantly reduced product defects, improved overall product quality, and minimized waste. |
Toyota | Automotive | Robotic automation combined with AI-driven scheduling and logistics optimization for its assembly lines. | Increased production efficiency, reduced labor costs, and improved product consistency. |
Challenges and Strategies for Successful AI Implementation
Implementing AI and automation in manufacturing isn’t without its hurdles. Companies often face significant challenges during the integration process. Understanding these challenges and the strategies used to overcome them is crucial for successful adoption.
One major challenge is data integration and quality. AI algorithms rely on vast amounts of high-quality data. Many manufacturers struggle to consolidate data from disparate sources, and data cleaning and preprocessing can be time-consuming and resource-intensive. Strategies to overcome this include investing in robust data management systems, implementing data quality checks, and adopting standardized data formats.
Another key challenge is integrating AI systems with existing infrastructure. Legacy systems often lack the necessary interfaces for seamless AI integration. This requires careful planning, potentially involving system upgrades or the development of custom integration solutions. Strategies here involve phased implementation, prioritizing integration points, and collaborating with experienced integration partners.
Finally, skill gaps and workforce training are significant concerns. Implementing and managing AI systems requires specialized expertise. Companies need to invest in training programs to upskill their workforce and attract talent with the necessary skills. Strategies include partnering with educational institutions, offering internal training programs, and recruiting skilled professionals.
Conclusion: How AI And Automation Are Redefining The Manufacturing Industry
The integration of AI and automation in manufacturing isn’t just a trend; it’s a fundamental shift that’s reshaping the industry’s future. While challenges exist, like job displacement and ethical considerations, the potential benefits – increased efficiency, improved quality, and innovative product development – are too significant to ignore. The smart factories of tomorrow are being built today, and understanding this transformation is key to navigating the exciting and ever-evolving landscape of modern manufacturing. Are you ready to embrace the change?