How AI and Automation are Changing Manufacturing Industries? Forget smokestacks and assembly lines – the factory floor is getting a serious tech upgrade. We’re talking robots with laser precision, AI that predicts problems before they happen, and data-driven decisions that boost efficiency like never before. This isn’t just about faster production; it’s a complete overhaul, impacting everything from worker roles to supply chain strategies. Get ready to see how the future of manufacturing is being built, one algorithm at a time.
From predictive maintenance that keeps machines humming to AI-powered quality control that eliminates defects, the impact is undeniable. We’ll explore how automation is streamlining processes, optimizing resource allocation, and even creating entirely new job opportunities. But it’s not all sunshine and robots; we’ll also tackle the challenges, including workforce adaptation and the ethical considerations of this rapid technological shift. So, buckle up, because this manufacturing revolution is happening now.
Increased Efficiency and Productivity in Manufacturing
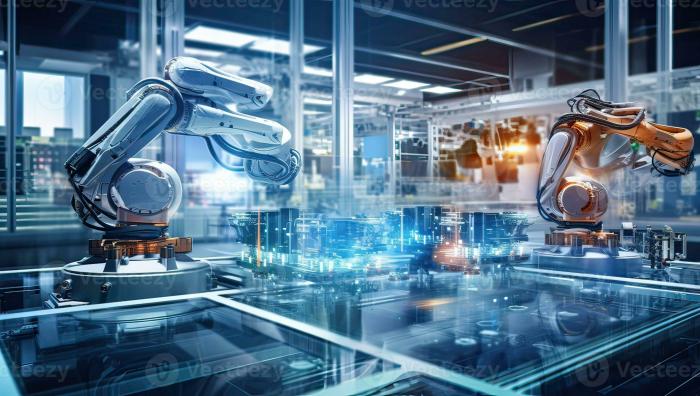
Source: vecteezy.com
The marriage of artificial intelligence (AI) and automation is revolutionizing manufacturing, ushering in an era of unprecedented efficiency and productivity. No longer are factories reliant on solely human labor and guesswork; instead, intelligent systems are optimizing processes, predicting problems, and boosting output in ways previously unimaginable. This translates to significant cost savings, improved product quality, and a more competitive global market position for manufacturers who embrace these technologies.
AI-Powered Predictive Maintenance
Predictive maintenance, driven by AI algorithms, analyzes sensor data from machinery to anticipate potential failures. This allows for proactive interventions, minimizing costly downtime. Instead of relying on scheduled maintenance that might be too early or too late, AI analyzes patterns and anomalies in real-time, predicting when a machine is likely to fail. This allows for repairs to be scheduled at the optimal time, preventing unexpected shutdowns and extending the lifespan of equipment. For example, a factory using AI-powered predictive maintenance on its assembly line robots might identify a potential motor failure days in advance, allowing for a planned replacement during a less busy period, minimizing production disruption. This contrasts sharply with reactive maintenance, where a breakdown halts production entirely until repairs are completed, often at a much higher cost.
Robotic Process Automation (RPA) in Manufacturing
Robotic Process Automation (RPA) is streamlining repetitive tasks within manufacturing processes. These software robots automate mundane, rule-based activities, freeing up human workers to focus on more complex and creative endeavors. RPA can handle tasks like data entry, invoice processing, and quality control checks, all with significantly higher speed and accuracy than human workers. Imagine a factory where RPA bots automatically scan and verify incoming parts, ensuring that only compliant materials reach the assembly line. This reduces human error, improves quality control, and speeds up the entire production process. The result is a significant increase in efficiency and a reduction in labor costs associated with these repetitive tasks.
Efficiency Gains: Traditional vs. AI-Driven Manufacturing
Traditional manufacturing methods rely heavily on manual labor, scheduled maintenance, and often, reactive problem-solving. This approach inherently leads to higher rates of downtime, more waste, and greater potential for human error. In contrast, AI and automation significantly reduce downtime through predictive maintenance, improve accuracy through RPA, and optimize resource allocation through intelligent scheduling. The difference in efficiency can be dramatic, with AI-driven factories often boasting significantly higher output and lower operational costs. A simple example is comparing the speed and accuracy of a human inspecting parts against an AI-powered vision system. The AI system can process hundreds of parts per minute with near-perfect accuracy, far surpassing human capabilities.
AI Optimization of Production Scheduling and Resource Allocation
AI algorithms excel at optimizing production schedules and resource allocation. By analyzing historical data, real-time demand, and various constraints (such as machine availability and material supply), AI systems create optimized schedules that maximize output while minimizing waste and delays. This involves dynamically adjusting production plans based on unforeseen events, ensuring that resources are always used efficiently. For instance, an AI system might detect a sudden surge in demand for a particular product and automatically adjust the production schedule to meet this demand, reallocating resources as needed. This dynamic optimization is impossible to achieve with manual scheduling alone.
Cost Savings of AI-Driven Automation vs. Manual Labor
Manufacturing Sector | AI-Driven Automation (Estimated Annual Savings) | Manual Labor (Estimated Annual Costs) | Percentage Savings |
---|---|---|---|
Automotive | $500,000 – $2,000,000 | $1,000,000 – $4,000,000 | 50% – 80% |
Electronics | $250,000 – $1,000,000 | $500,000 – $2,000,000 | 50% – 75% |
Pharmaceuticals | $100,000 – $500,000 | $200,000 – $1,000,000 | 50% – 90% |
Food Processing | $75,000 – $300,000 | $150,000 – $600,000 | 50% – 80% |
Enhanced Quality Control and Product Development
The integration of AI and automation is revolutionizing manufacturing’s approach to quality control and product development, moving beyond traditional methods to achieve unprecedented levels of precision, efficiency, and customer satisfaction. This shift allows manufacturers to not only identify and rectify defects more effectively but also to proactively design and develop products better tailored to market demands.
AI’s impact on quality control and product development is multifaceted, leveraging advanced technologies to streamline processes and enhance outcomes. This includes the use of computer vision for defect detection, AI algorithms for data analysis and design optimization, and personalized product development based on individual customer preferences.
Computer Vision in Defect Detection
Computer vision systems, powered by AI algorithms, are transforming quality control by providing a rapid and highly accurate method of identifying defects in manufactured goods. These systems use cameras and sophisticated image processing techniques to analyze products as they move along the production line. Unlike human inspectors, who can be prone to fatigue and inconsistencies, computer vision systems operate continuously with consistent accuracy, detecting even minute flaws that might be missed by the human eye. This leads to reduced waste, improved product quality, and ultimately, increased customer satisfaction. For example, in the automotive industry, computer vision is used to inspect car bodies for scratches, dents, and paint imperfections, ensuring that only flawless vehicles leave the factory.
AI-Driven Analysis for Product Design Improvement
AI algorithms excel at analyzing vast datasets, uncovering patterns and insights that would be impossible for humans to discern. In manufacturing, this capability is leveraged to optimize product design and functionality. By feeding AI systems with data on product performance, customer feedback, and market trends, manufacturers can identify areas for improvement and develop innovative new designs. For instance, AI can analyze data from sensor-equipped products to identify points of failure or areas for improved durability. This data-driven approach leads to products that are not only more reliable but also better suited to the needs of the target market. This allows for predictive maintenance, preventing breakdowns before they occur.
Advantages of AI in Quality Assurance
The advantages of using AI in quality assurance compared to traditional methods are significant. AI systems offer increased speed and accuracy in defect detection, leading to reduced waste and improved efficiency. They provide consistent performance, eliminating the human error factor and ensuring uniform quality across all products. Furthermore, AI can analyze far larger datasets than humans, leading to a deeper understanding of product performance and customer needs, ultimately resulting in better product design and increased customer satisfaction. Traditional methods, relying heavily on manual inspection, are slower, less consistent, and less capable of analyzing the vast amounts of data now available.
AI-Enabled Product Personalization
AI is enabling a new era of personalized manufacturing, where products are tailored to the specific needs and preferences of individual customers. By analyzing customer data, AI algorithms can identify patterns and predict preferences, allowing manufacturers to create customized products. For example, a shoe manufacturer might use AI to design shoes with customized fit and features based on individual customer foot scans and activity levels. This level of personalization enhances customer satisfaction and brand loyalty, creating a competitive advantage in the marketplace.
AI-Driven Quality Control Process Flowchart
Imagine a flowchart with these stages:
1. Data Acquisition: High-resolution images and sensor data are collected from products during the manufacturing process.
2. Data Preprocessing: Collected data is cleaned and prepared for analysis by AI algorithms. This might involve noise reduction or data transformation.
3. Defect Detection: AI algorithms, specifically trained computer vision models, analyze the data to identify defects.
4. Classification & Localization: The AI system classifies identified defects and pinpoints their location on the product.
5. Feedback & Adjustment: The system provides real-time feedback to the manufacturing process, enabling immediate adjustments to correct defects or prevent their recurrence.
6. Reporting & Analysis: The system generates reports on defect rates, types, and locations, providing valuable insights for process improvement.
Improved Supply Chain Management and Logistics
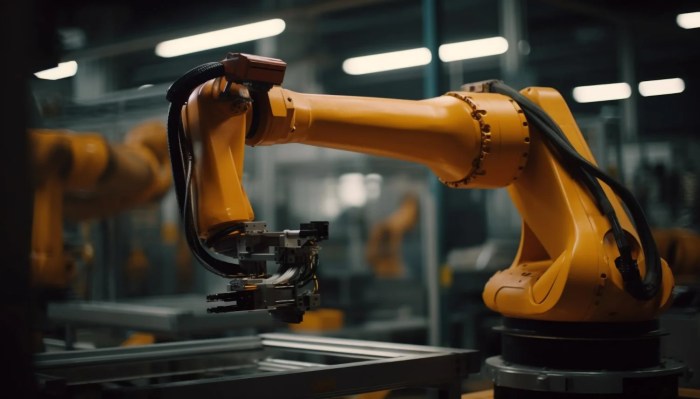
Source: the-newshub.com
AI and automation are reshaping manufacturing, boosting efficiency and precision. This digital transformation mirrors the leaps in other sectors; consider how the low latency of 5G is set to completely change the game, as detailed in this insightful article: How 5G Will Revolutionize Gaming and Virtual Reality Experiences. Ultimately, similar technological advancements are driving progress across diverse industries, including the future of smart factories.
The manufacturing landscape is undergoing a dramatic shift, driven by the integration of AI and automation. Beyond boosting efficiency and quality, these technologies are revolutionizing supply chain management and logistics, creating a more responsive, resilient, and cost-effective system. This involves optimizing inventory, predicting disruptions, and streamlining transportation – ultimately leading to a more agile and profitable manufacturing operation.
AI is transforming how manufacturers manage their inventory. Gone are the days of relying on gut feeling and outdated spreadsheets. Instead, sophisticated AI algorithms analyze vast datasets – encompassing sales forecasts, production schedules, and real-time inventory levels – to predict demand with remarkable accuracy. This allows for precise inventory optimization, minimizing storage costs and preventing stockouts or overstocking, which leads to significant waste reduction. For example, a leading consumer goods company used AI-powered demand forecasting to reduce its inventory holding costs by 15% within a year, freeing up capital for reinvestment in other areas.
AI-Driven Inventory Management and Waste Reduction, How AI and Automation are Changing Manufacturing Industries
AI algorithms, powered by machine learning, analyze historical sales data, seasonal trends, and even external factors like weather patterns and economic indicators to predict future demand. This predictive capability enables manufacturers to optimize their inventory levels, reducing the risk of stockouts (leading to lost sales) and overstocking (leading to increased storage costs and potential obsolescence). This precision allows for just-in-time inventory management, where materials arrive precisely when needed, minimizing storage space and reducing waste. The implementation of AI-powered inventory management systems has resulted in significant cost savings and increased efficiency for many manufacturers. A key element is the use of anomaly detection algorithms which can flag unusual patterns indicating potential issues such as faulty equipment or supplier delays.
Predicting and Mitigating Supply Chain Disruptions
AI’s predictive capabilities extend beyond inventory management to encompass the entire supply chain. By analyzing data from various sources, including weather reports, geopolitical events, and transportation networks, AI can identify potential disruptions – such as port congestion, natural disasters, or supplier failures – before they impact production. This early warning system allows manufacturers to proactively implement mitigation strategies, such as rerouting shipments, securing alternative suppliers, or adjusting production schedules. For instance, a major automotive manufacturer successfully used AI to predict a potential chip shortage months in advance, allowing them to secure alternative supply sources and avoid significant production delays. This proactive approach minimizes the financial and reputational damage associated with supply chain disruptions.
AI-Powered Logistics Solutions for Optimization
Various AI-powered logistics solutions are available to optimize transportation and delivery. These include route optimization algorithms that determine the most efficient delivery routes, considering factors such as traffic patterns, road closures, and delivery time windows. AI-powered fleet management systems monitor vehicle performance, optimize fuel consumption, and improve driver safety. Furthermore, AI-driven warehouse management systems automate tasks such as picking, packing, and shipping, increasing efficiency and reducing errors. The use of autonomous vehicles and drones is also gaining traction, offering potential for faster and more cost-effective delivery, particularly for last-mile logistics. A global logistics company reported a 10% reduction in delivery times and a 5% decrease in fuel costs after implementing an AI-powered route optimization system.
Enhanced Traceability and Transparency in the Supply Chain
AI enhances traceability and transparency by providing real-time visibility into the movement of goods throughout the supply chain. This is achieved through the use of RFID tags, blockchain technology, and sensor networks, which track products from origin to delivery. This increased transparency allows manufacturers to quickly identify and address any issues, ensuring product quality and compliance with regulations. For example, in the food industry, AI-powered traceability systems can quickly pinpoint the source of a contaminated product, preventing widespread recalls and protecting consumers. This improved transparency also builds trust with consumers and enhances brand reputation.
Benefits and Challenges of AI-Driven Supply Chain Management
The implementation of AI in supply chain management offers numerous benefits but also presents certain challenges.
- Benefits: Increased efficiency and productivity, reduced costs (inventory, transportation, labor), improved forecasting accuracy, enhanced risk management, improved customer satisfaction, increased transparency and traceability.
- Challenges: High initial investment costs, need for skilled workforce to implement and manage AI systems, data security and privacy concerns, integration with existing systems, potential for bias in AI algorithms, and the need for robust data infrastructure.
The Impact of AI and Automation on the Manufacturing Workforce: How AI And Automation Are Changing Manufacturing Industries
The rise of AI and automation in manufacturing is undeniably reshaping the employment landscape. While fears of widespread job displacement are valid, the reality is far more nuanced, presenting both challenges and opportunities for the manufacturing workforce. This transformation requires proactive adaptation, strategic reskilling initiatives, and a focus on creating new roles that leverage the unique capabilities of humans alongside intelligent machines.
Automation’s impact on jobs is a complex issue. While some roles will inevitably be automated, leading to job displacement in certain areas, AI simultaneously creates a demand for new skills and entirely new job categories. This shift necessitates a focus on reskilling and upskilling the existing workforce to meet the evolving needs of the industry. Companies are adopting various strategies to navigate this transition, ensuring a smooth shift towards a more technologically advanced and efficient manufacturing sector.
Job Displacement and Reskilling Initiatives
The automation of repetitive and physically demanding tasks is already underway in many manufacturing plants. This has led to concerns about job losses, particularly for workers with limited skills. However, the narrative isn’t solely one of displacement. Successful companies are investing heavily in reskilling programs, providing training to existing employees to acquire new skills relevant to AI-driven manufacturing processes. This includes training in areas such as data analysis, programming, robotics maintenance, and AI system operation. For example, Siemens offers extensive training programs for its employees to adapt to the changing landscape, focusing on digitalization and automation skills. These programs aim to equip workers with the competencies needed to thrive in the new manufacturing environment.
New Job Roles and Opportunities
AI’s integration into manufacturing is not simply about replacing human workers; it’s about augmenting human capabilities. This leads to the creation of new job roles requiring specialized skills. These roles include AI specialists, data scientists, robotics engineers, and AI system integrators. These professionals are crucial for designing, implementing, maintaining, and optimizing AI systems within manufacturing environments. Furthermore, the increased complexity of AI-driven systems necessitates roles focused on cybersecurity and data privacy, ensuring the integrity and security of manufacturing processes. For instance, the increasing reliance on predictive maintenance using AI creates a need for skilled technicians capable of interpreting AI-generated insights and performing targeted maintenance.
Strategies for Workforce Adaptation
Companies are adopting various strategies to adapt to the changing workforce landscape. These include investing in comprehensive training programs, fostering a culture of continuous learning, and collaborating with educational institutions to develop curricula aligned with the needs of the industry. Partnerships between industry and academia are crucial for developing talent pipelines and ensuring a steady supply of skilled workers. Moreover, some companies are exploring flexible work arrangements and upskilling initiatives to retain experienced employees and leverage their institutional knowledge. This proactive approach aims to mitigate the negative impacts of automation while maximizing the benefits of AI integration.
Skills Comparison: Traditional vs. AI-Driven Manufacturing
Traditional manufacturing jobs often emphasized manual dexterity, repetitive tasks, and basic technical skills. AI-driven manufacturing roles, in contrast, require a blend of technical expertise, analytical skills, and problem-solving abilities. While some traditional skills remain relevant, the focus shifts towards data interpretation, programming, AI system management, and collaborative work with robots and automated systems. For example, a traditional machine operator might primarily focus on operating a single machine, while an AI-driven manufacturing technician might oversee multiple automated systems, monitor their performance using AI-generated data, and troubleshoot complex issues using data analytics.
Visual Representation: Transformation of the Manufacturing Workforce
Imagine an infographic with a split timeline, showing the past and future of manufacturing work. The left side (past) depicts a factory floor with workers performing repetitive tasks on individual machines, symbolized by simple icons representing manual labor. The right side (future) shows a more automated factory, with robots and AI systems working alongside human workers. Human icons are depicted interacting with advanced technologies, represented by icons showing data analysis, programming, and AI system management. The infographic uses color-coding to differentiate between job roles that have been automated (greyed out) and new roles created by AI (bright, vibrant colors). A central arrow visually connects the past and future, emphasizing the transition. Key statistics, such as the projected growth in AI-related manufacturing jobs, could be incorporated to strengthen the message. The overall message is clear: while some jobs are lost, many more are created, requiring a shift in skills and a collaborative approach between humans and machines.
Safety and Security Enhancements in Manufacturing Environments
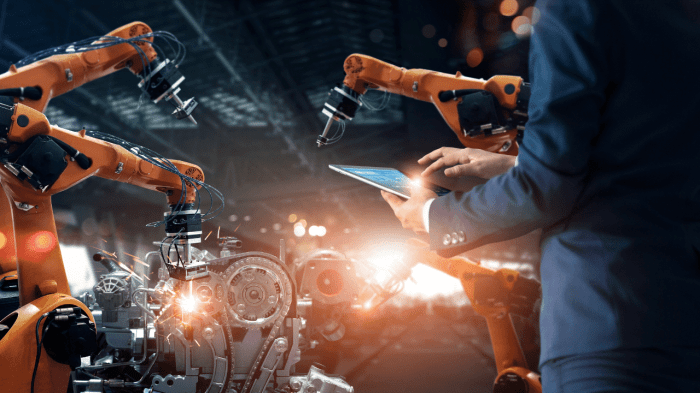
Source: darwinrecruitment.com
The integration of AI and automation isn’t just about boosting productivity; it’s fundamentally reshaping workplace safety and security in manufacturing. By leveraging the power of data analysis and predictive capabilities, AI systems are creating safer, more secure, and ultimately more efficient manufacturing environments. This shift is driven by a need to minimize risks, protect valuable data, and ensure the well-being of the workforce.
AI-powered systems are revolutionizing how manufacturers approach safety and security, moving beyond reactive measures to proactive risk mitigation. This involves a multi-faceted approach encompassing hazard identification, cybersecurity enhancements, and advanced access control.
AI-Powered Hazard Identification and Risk Mitigation
AI algorithms can analyze vast amounts of real-time data from various sources – sensors embedded in machinery, environmental monitoring systems, and even worker wearable devices – to identify potential hazards before they lead to accidents. For instance, an AI system might detect anomalies in machine vibrations indicating impending failure, alerting maintenance personnel before a catastrophic breakdown occurs. Predictive maintenance, enabled by AI, reduces downtime and prevents accidents caused by malfunctioning equipment. Furthermore, AI can analyze historical accident data to identify patterns and predict high-risk situations, allowing for proactive interventions such as retraining programs or improved safety protocols. This proactive approach shifts the focus from responding to incidents to preventing them altogether.
AI’s Role in Cybersecurity for Manufacturing
The manufacturing sector handles sensitive data, from intellectual property to supply chain information, making it a prime target for cyberattacks. AI is proving to be a powerful tool in enhancing cybersecurity. AI-driven intrusion detection systems can analyze network traffic in real-time, identifying anomalies that might indicate malicious activity. Machine learning algorithms can learn to recognize patterns of normal network behavior and flag deviations, significantly improving the speed and accuracy of threat detection. Moreover, AI can automate incident response, isolating compromised systems and minimizing the impact of attacks. For example, an AI system might detect a suspicious login attempt from an unusual location and automatically block access, preventing a potential breach.
AI-Driven Surveillance Systems for Access Control
AI is transforming access control systems in manufacturing facilities, moving beyond traditional methods like keycards and security guards. AI-powered video analytics can monitor facility entrances and exits, identifying unauthorized personnel or suspicious behavior. Facial recognition technology can verify the identity of employees, ensuring only authorized individuals gain access to restricted areas. AI-powered systems can also learn and adapt to changing security needs, automatically adjusting access permissions based on real-time risk assessments. This dynamic approach enhances security while minimizing the need for extensive human oversight.
AI-Enhanced Ergonomic Assessments and Risk Prediction
AI can significantly improve worker safety by conducting ergonomic assessments and predicting potential musculoskeletal injuries. By analyzing data from wearable sensors that track worker movements and postures, AI algorithms can identify repetitive motions or awkward postures that might lead to injuries. This allows for proactive interventions such as workstation redesign or adjustments to work processes, minimizing the risk of work-related musculoskeletal disorders (WMSDs). Predictive models can also be developed to identify workers at high risk of injury based on their individual characteristics and work patterns, enabling targeted interventions to prevent incidents. For example, an AI system might flag a worker who consistently performs a specific task in an inefficient manner, suggesting modifications to improve their posture and reduce strain.
Best Practices for Ethical and Responsible AI in Manufacturing
Implementing AI in manufacturing requires a commitment to ethical and responsible practices. Here are some key considerations:
- Data Privacy and Security: Implement robust data security measures to protect sensitive worker data collected by AI systems.
- Transparency and Explainability: Ensure that AI algorithms are transparent and explainable, allowing for understanding of their decision-making processes.
- Bias Mitigation: Actively work to mitigate biases in data and algorithms to prevent unfair or discriminatory outcomes.
- Human Oversight and Accountability: Maintain human oversight of AI systems and establish clear lines of accountability for their actions.
- Worker Training and Reskilling: Provide adequate training and reskilling opportunities for workers to adapt to the changing workplace.
Last Word
The integration of AI and automation in manufacturing isn’t just a trend; it’s the new normal. While challenges remain, the potential benefits—increased efficiency, improved quality, and enhanced safety—are too significant to ignore. The future of manufacturing is intelligent, automated, and undeniably exciting. Companies that embrace this transformation will not only survive but thrive in the competitive landscape of tomorrow. The question isn’t *if* this will happen, but *how* quickly companies can adapt and leverage these powerful tools to reshape their operations.