How 3D Printing is Disrupting Traditional Manufacturing Processes? It’s not just a buzzword; it’s a revolution. For decades, manufacturing relied on subtractive methods—shaving away material to create a product. 3D printing, or additive manufacturing, flips the script, building objects layer by layer from a digital design. This shift is impacting everything from prototyping speed to product customization, shaking up industries and forcing companies to rethink their entire production pipelines. Prepare for a deep dive into this game-changing technology.
This shift towards additive manufacturing offers unprecedented speed and efficiency. Prototyping, once a lengthy and expensive process, becomes a rapid affair. Imagine designing a complex part and having a functional prototype within hours, not weeks. This agility allows for faster iteration, quicker problem-solving, and ultimately, a much faster time-to-market for new products. Plus, the reduced need for extensive tooling slashes upfront costs significantly.
The Rise of 3D Printing in Manufacturing
For decades, traditional manufacturing reigned supreme, relying on subtractive methods—carving away material to create a desired shape. Think milling machines meticulously shaving down blocks of metal, or lathes spinning wood into intricate forms. This approach, while effective, often involved significant material waste, lengthy production times, and high setup costs. The emergence of 3D printing, or additive manufacturing, marked a seismic shift in this landscape. This revolutionary technology builds objects layer by layer from a digital design, offering a fundamentally different approach to production.
The core difference between traditional and additive manufacturing lies in their processes. Traditional methods, like casting, forging, and machining, remove material to achieve the final product. Additive manufacturing, on the other hand, adds material in a precisely controlled manner, creating complex geometries impossible with traditional techniques. This allows for greater design freedom, reduced waste, and the potential for highly customized products.
Industries Embracing 3D Printing
The impact of 3D printing is already being felt across various sectors. The aerospace industry utilizes 3D printing to create lightweight, high-strength components for aircraft and spacecraft, reducing weight and improving fuel efficiency. Medical professionals are using it to produce personalized prosthetics and implants tailored to individual patient needs, improving fit and functionality. The automotive industry employs 3D printing for rapid prototyping and the creation of customized parts, streamlining the design and production process. Furthermore, the consumer goods sector is leveraging 3D printing for on-demand manufacturing, personalized products, and shorter production cycles. For example, companies are now able to create highly customized phone cases or small-scale personalized toys on demand. The possibilities are expanding rapidly, with new applications constantly emerging.
Speed and Efficiency
Forget the agonizing waits of traditional manufacturing. 3D printing is injecting a shot of adrenaline into the production process, dramatically speeding up prototyping and slashing production times. This leap in efficiency isn’t just about faster turnaround; it’s a fundamental shift in how we design, build, and bring products to market.
The speed advantage of 3D printing stems from its digital nature and additive manufacturing process. Unlike subtractive methods that require carving away material, 3D printing builds objects layer by layer, directly from a digital design. This eliminates many time-consuming steps, resulting in significant time savings across the entire production lifecycle.
Prototyping Speed Comparison
Traditional prototyping methods, like CNC machining or injection molding, often involve complex tooling, setup, and multiple iterations. This can easily stretch prototyping timelines into weeks or even months. 3D printing, on the other hand, can produce functional prototypes in a matter of hours or days, depending on the complexity and size of the design. This rapid prototyping capability allows for faster design iteration, quicker feedback loops, and ultimately, a more efficient product development process. Imagine a scenario where engineers can test and refine multiple design variations within a single day, instead of waiting weeks for each iteration.
3D printing’s shaking up manufacturing, offering personalized products and on-demand production. This level of customization mirrors the travel industry’s shift, where virtual experiences are becoming increasingly prevalent, as seen in this article on How Virtual Reality is Revolutionizing the Travel Industry. Both industries are embracing digital tools to redefine their processes, ultimately leading to more efficient and innovative outcomes.
The future of manufacturing, like travel, is undeniably digital.
Impact on Production Lead Times, How 3D Printing is Disrupting Traditional Manufacturing Processes
The impact on production lead times is equally transformative. Traditional manufacturing often involves lengthy setup times for tooling, extensive production runs, and complex supply chains. 3D printing, especially in low-volume production, can significantly reduce these lead times. This is particularly advantageous for customized products or small batches, where traditional methods become inefficient and costly. For example, a customized medical implant can be produced much faster using 3D printing than through conventional casting or machining, potentially saving valuable time for patients needing urgent treatment.
Reduced Need for Extensive Tooling
One of the most significant cost and time savings associated with 3D printing is the drastically reduced need for extensive tooling. Traditional manufacturing often requires costly and time-consuming tooling creation for each product, a process that can take weeks or even months. 3D printing eliminates this step, as the only “tool” required is the 3D printer itself. This allows for on-demand production, reduces upfront investment, and enables faster response to market changes or customer demands. Think about a small company designing a new phone case – they can test several designs and quickly manufacture small batches without the hefty upfront cost of traditional mold making.
Prototyping and Production Time Comparison
Method | Prototyping Time | Production Time (Low Volume) | Production Time (High Volume) |
---|---|---|---|
3D Printing | Hours to Days | Days to Weeks | Weeks to Months (depending on printer capacity and design complexity) |
Injection Molding | Weeks to Months (including tooling design and manufacture) | Weeks to Months | Weeks to Months (depending on production run size) |
CNC Machining | Days to Weeks | Weeks to Months | Months (depending on production run size and material) |
Cost Reduction and Material Optimization
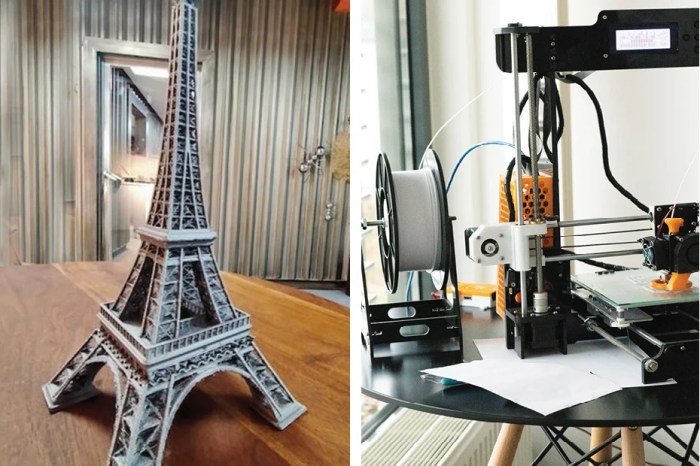
Source: gulfbusiness.com
3D printing isn’t just about speed and efficiency; it’s a game-changer for manufacturing costs. By drastically reducing material waste, streamlining production, and minimizing labor, it offers a compelling alternative to traditional methods. This section dives into the significant cost savings associated with additive manufacturing, showcasing how it optimizes both material usage and overall expenses.
The cost savings from 3D printing stem from several key advantages. Firstly, it significantly reduces material waste. Traditional subtractive manufacturing, like milling or turning, involves removing large amounts of material to create a final product. 3D printing, on the other hand, adds material only where needed, resulting in minimal waste. This translates directly to lower material costs and a smaller environmental footprint. Secondly, 3D printing minimizes labor costs. While setting up and monitoring the 3D printer requires some expertise, the actual production process is often automated, reducing the need for extensive manual labor involved in traditional methods. This is especially impactful for complex parts requiring intricate machining or assembly.
On-Demand Production and Inventory Management
On-demand production is a major advantage 3D printing offers. Unlike traditional manufacturing, which often necessitates large-scale production runs and subsequent inventory storage, 3D printing allows for the creation of parts only when needed. This eliminates the substantial costs associated with warehousing, storage, and potential obsolescence of inventory. Companies can respond quickly to fluctuating demands, producing only the necessary quantities, leading to significant savings in inventory holding costs and reducing the risk of wasted materials due to outdated designs or low demand.
Material Optimization and Waste Reduction
3D printing’s ability to create complex geometries with internal structures allows for significant material optimization. Traditional manufacturing often results in designs that are structurally over-engineered to compensate for limitations in manufacturing processes. 3D printing enables the creation of lightweight, high-strength parts with optimized internal structures, using less material while maintaining or even exceeding the strength of traditionally manufactured components. This leads to considerable cost savings on material purchases and reduced transportation costs due to lighter weight. Furthermore, the ability to easily modify designs and test different iterations digitally before printing reduces the risk of costly mistakes and material waste during the production process.
Hypothetical Case Study: Custom Orthotics
Let’s consider a hypothetical case study comparing the production of custom orthotics using traditional methods versus 3D printing. Assume a traditional method involves casting, molding, and trimming, requiring skilled labor and specialized equipment. The material cost per orthotic might be $20, labor cost $50, and equipment amortization $10, totaling $80 per orthotic. Now, consider 3D printing. The material cost might be $15, with minimal labor involved, say $10, and minimal equipment amortization. This results in a total cost of approximately $25 per orthotic. In this scenario, 3D printing results in a cost reduction of 68.75% ($55 savings per orthotic). While the initial investment in a 3D printer might be significant, the long-term savings, especially for high-volume or customized orders, are substantial. This illustrates how 3D printing can dramatically reduce manufacturing costs and improve profitability.
Customization and Mass Personalization
Forget cookie-cutter products – 3D printing is revolutionizing manufacturing by allowing for unparalleled levels of customization and mass personalization. This technology moves beyond simply producing identical items in bulk; it empowers businesses to create unique products tailored to individual customer needs and preferences, opening up exciting new possibilities for both businesses and consumers.
3D printing, or additive manufacturing, achieves mass personalization by building objects layer by layer from a digital design. This means that creating a slightly modified version of a product, or even a completely unique design, requires minimal additional cost and effort compared to traditional manufacturing methods. This flexibility allows companies to cater to niche markets and offer highly personalized experiences, leading to increased customer satisfaction and brand loyalty.
Examples of Personalized Products Enabled by 3D Printing
Several companies are already leveraging the power of 3D printing to create personalized products. Consider hearing aid manufacturers who can now produce custom-fitted devices based on individual ear scans, ensuring optimal comfort and sound quality. Similarly, the dental industry uses 3D printing to create highly accurate and personalized dental prosthetics, significantly improving patient outcomes. In the fashion industry, designers are experimenting with 3D-printed clothing and accessories, offering bespoke designs tailored to individual body shapes and preferences. These are just a few examples of how 3D printing is transforming various industries by enabling mass personalization.
Impact on Consumer Preferences and Market Dynamics
The ability to personalize products significantly impacts consumer preferences. Customers increasingly value unique and customized items that reflect their individual tastes and needs. This trend is driving a shift towards a more individualized and experience-driven marketplace. The ability to easily customize products also fosters a sense of ownership and connection between the consumer and the brand. This leads to stronger brand loyalty and increased willingness to pay a premium for personalized products. The market is responding with a growing demand for customized goods, creating new opportunities for businesses that embrace 3D printing technology.
Industries Benefiting from 3D Printing’s Customization Capabilities
A wide range of industries are benefiting from 3D printing’s ability to offer mass customization.
- Healthcare: Personalized prosthetics, medical implants, surgical guides, and custom-fitted medical devices.
- Aerospace: Customized aircraft parts, lightweight components, and tooling for specialized applications.
- Automotive: Personalized car parts, custom-designed interiors, and tooling for small-batch production.
- Consumer Goods: Personalized jewelry, toys, and fashion accessories.
- Dental: Custom-made dental crowns, bridges, and aligners.
The flexibility and cost-effectiveness of 3D printing in creating customized products are driving significant growth in these and other industries, reshaping how products are designed, manufactured, and delivered to consumers. The ability to meet individual customer demands is no longer a luxury but a crucial competitive advantage in today’s market.
Design Flexibility and Complex Geometries
Traditional manufacturing methods, reliant on subtractive processes like milling and casting, or forming processes like stamping and forging, often struggle with intricate designs. These techniques impose significant limitations on the complexity and freedom of form achievable. 3D printing, however, offers a revolutionary approach, enabling the creation of parts with geometries previously deemed impossible or prohibitively expensive. This additive manufacturing process builds objects layer by layer, liberating designers from the constraints of traditional tooling and fabrication methods.
The design freedom offered by 3D printing is transformative. Imagine designing a part with internal channels for cooling, intricate lattice structures for weight reduction, or seamlessly integrated features that would be impossible to achieve through conventional techniques. This level of design freedom translates directly into improved performance, reduced weight, and enhanced functionality.
Complex Geometries Achievable Through 3D Printing
3D printing allows for the creation of parts with internal cavities, undercuts, and complex interlocking features—elements that would be extremely difficult, if not impossible, to produce using traditional subtractive manufacturing. For instance, consider a turbine blade with internal cooling channels optimized for airflow. Traditional methods would require complex and expensive tooling to create these channels, while 3D printing allows for their direct fabrication. Another example is the creation of intricate lattice structures, which provide high strength-to-weight ratios. These structures are impossible to create using traditional casting or machining techniques due to their complexity and the need for intricate support structures.
Lightweight and High-Strength Components
One of the key advantages of 3D printing lies in its ability to create lightweight yet incredibly strong components. By utilizing lattice structures or other optimized designs, engineers can reduce the weight of a part without compromising its structural integrity. This is particularly beneficial in aerospace and automotive applications, where weight reduction directly translates to improved fuel efficiency and performance. For example, the aerospace industry is leveraging 3D printing to create lightweight yet strong components for aircraft, reducing fuel consumption and improving overall efficiency. Similarly, the automotive industry uses 3D printing to manufacture lightweight parts, leading to improved vehicle performance and reduced emissions.
Example of a Complex Part
Let’s visualize a hypothetical part: a bio-inspired hip implant.
* Interlocking Structure: The implant features an intricate, interlocking lattice structure designed to mimic the natural porous structure of bone. This promotes bone ingrowth and integration, leading to a more secure and stable implant.
* Internal Channels: Micro-channels are integrated within the lattice structure to allow for the delivery of medication or growth factors directly to the bone tissue. This could accelerate healing and reduce the risk of complications.
* Customizable Geometry: The implant’s geometry is fully customizable to match the patient’s unique anatomy, ensuring a perfect fit and optimal functionality. This level of customization would be impossible to achieve using traditional manufacturing techniques.
* Lightweight and Biocompatible Material: The implant is 3D printed from a lightweight, biocompatible titanium alloy, minimizing stress on the surrounding bone and reducing the risk of rejection.
This hip implant exemplifies the possibilities offered by 3D printing. The intricate lattice structure, internal channels, and customizable geometry would be nearly impossible to create using traditional manufacturing methods. The result is a more effective, personalized, and durable medical implant.
Challenges and Limitations of 3D Printing in Manufacturing
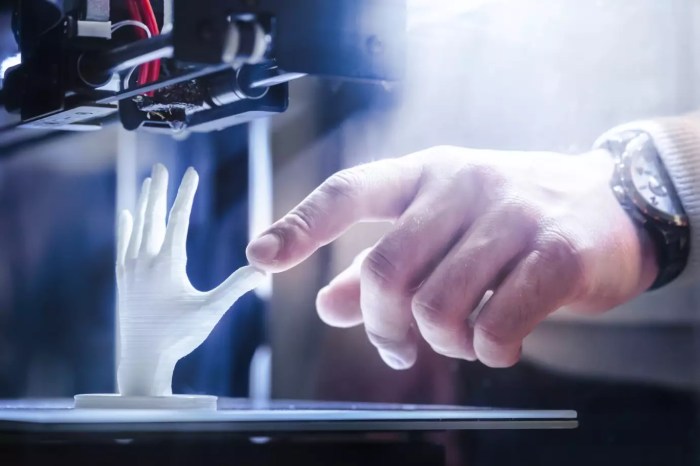
Source: emerj.com
3D printing, despite its revolutionary potential, isn’t a silver bullet for all manufacturing woes. While it offers incredible advantages, several limitations currently hinder its widespread adoption and full realization of its potential. These challenges are not insurmountable, and ongoing research and development are actively addressing them, but understanding these hurdles is crucial for realistic expectations and strategic implementation.
Material Limitations and Scalability
One of the biggest bottlenecks is the range of printable materials. While the selection is constantly expanding, it still lags behind traditional manufacturing processes in terms of variety, performance characteristics (like high-temperature resistance or extreme durability), and cost-effectiveness for certain applications. Furthermore, scaling up production to meet the demands of mass manufacturing remains a challenge. The speed at which a single 3D printer can produce parts often pales in comparison to traditional methods like injection molding, especially for large-scale projects. For instance, creating thousands of identical plastic components might be significantly faster and cheaper using injection molding than with multiple 3D printers. This limitation necessitates careful consideration of project scope and material requirements before opting for 3D printing.
Quality Control and Consistency
Ensuring consistent quality and precision across multiple 3D-printed parts is a significant challenge. Factors like variations in temperature, humidity, and even the subtle inconsistencies in the printing material itself can lead to dimensional inaccuracies and variations in surface finish. This makes rigorous quality control measures essential, often involving extensive post-processing steps such as sanding, polishing, or even additional machining. These extra steps add to the overall production time and cost, potentially negating some of the advantages of 3D printing. Imagine a scenario where a batch of 3D-printed medical implants shows slight variations – the implications for safety and efficacy are obvious.
Skilled Labor and Specialized Expertise
Operating and maintaining 3D printing equipment requires a specialized skill set. Unlike some traditional manufacturing processes that can be operated with relatively less training, 3D printing necessitates expertise in areas such as material selection, parameter optimization, post-processing techniques, and troubleshooting. The need for skilled technicians and engineers adds to the overall cost of implementation and can create a bottleneck in scaling up operations. Finding and training personnel with the necessary expertise is a critical factor in successfully integrating 3D printing into manufacturing workflows. A lack of skilled operators can lead to inefficiencies, production delays, and even faulty parts.
Addressing the Challenges Through Research and Development
The limitations of 3D printing are not static; significant research and development efforts are underway to overcome them. For example, advancements in materials science are continuously expanding the range of printable materials, including high-performance polymers, composites, and even metals with improved properties. New printing techniques, such as binder jetting and multi-material printing, are improving speed, precision, and scalability. Furthermore, the development of sophisticated software and automation systems is streamlining the workflow, improving quality control, and reducing the need for extensive manual intervention. Companies are investing heavily in these areas, aiming to make 3D printing a more efficient, cost-effective, and widely applicable technology.
The Future of 3D Printing in Manufacturing
The rapid evolution of 3D printing technology is poised to reshape manufacturing as we know it. Beyond the current applications, exciting advancements in materials, processes, and integration with other technologies promise a future where customized, high-performance products are produced efficiently and sustainably. This section explores the key trends and predictions shaping this transformative journey.
Emerging Trends in 3D Printing Materials, Processes, and Applications
The development of novel materials is a crucial driver of 3D printing’s growth. We’re seeing a shift beyond traditional plastics towards biocompatible materials for medical implants, high-temperature alloys for aerospace components, and sustainable bio-based polymers for consumer goods. In terms of processes, advancements in multi-material printing enable the creation of parts with complex functionalities and integrated features, eliminating the need for assembly. Applications are expanding rapidly, moving beyond prototyping into mass production of customized products, personalized medicine solutions, and on-demand manufacturing in diverse sectors like construction and automotive. For instance, the use of bioprinting to create living tissues and organs represents a significant leap forward in medical technology. Similarly, the ability to 3D print entire building components is revolutionizing construction practices.
Predictions for the Future Impact of 3D Printing on Various Manufacturing Sectors
3D printing is predicted to significantly impact various manufacturing sectors in the coming years. The automotive industry, for example, is already using additive manufacturing for producing lightweight, high-strength parts, leading to fuel efficiency improvements. In the aerospace industry, 3D printing is enabling the creation of complex, customized components with intricate geometries, reducing weight and improving performance. The healthcare sector will witness a revolution with personalized medical devices and implants, tailored to individual patient needs. Even the food industry is exploring 3D printing for creating customized food products with unique textures and nutritional profiles. These are not just predictions; many of these applications are already in various stages of development and implementation. For example, Airbus is already utilizing 3D printing for aircraft parts, and numerous companies are developing personalized prosthetics and implants.
The Influence of Artificial Intelligence and Automation on 3D Printing
The integration of artificial intelligence (AI) and automation is set to revolutionize 3D printing further. AI-powered design optimization tools can analyze complex designs, predict potential failures, and generate optimized geometries for improved performance and reduced material usage. Automated processes, such as robotic material handling and post-processing, will enhance efficiency and reduce human error. AI-driven quality control systems will monitor the printing process in real-time, identifying and correcting defects automatically. This combination of AI and automation will lead to higher throughput, improved product quality, and reduced production costs. We can envision a future where entire 3D printing factories operate autonomously, producing customized products on demand with minimal human intervention.
Anticipated Milestones in the Development and Adoption of 3D Printing Technologies
A timeline of anticipated milestones illustrates the rapid pace of development:
Within the next 5 years:
- Widespread adoption of multi-material 3D printing in various industries.
- Significant advancements in bioprinting and personalized medicine applications.
- Increased automation and AI integration in 3D printing processes.
Within the next 10 years:
- Development of new materials with enhanced properties, such as self-healing materials.
- Establishment of large-scale, automated 3D printing factories.
- Significant reduction in the cost of 3D printing, making it accessible to smaller businesses.
Beyond 10 years:
- The emergence of new 3D printing technologies, such as 4D printing (shape-changing materials).
- Integration of 3D printing with other advanced manufacturing technologies, such as robotics and nanotechnology.
- A paradigm shift in manufacturing, with on-demand production becoming the norm.
Closing Summary: How 3D Printing Is Disrupting Traditional Manufacturing Processes

Source: precious3d.com
The rise of 3D printing isn’t just about faster production; it’s about unlocking a new era of design freedom and customization. From personalized medicine to bespoke consumer goods, the possibilities are endless. While challenges remain in scalability and material limitations, ongoing innovation promises to overcome these hurdles. The future of manufacturing is undeniably 3D, a future where creativity isn’t constrained by the limitations of traditional methods, but empowered by the boundless potential of additive manufacturing. Get ready for a world built layer by layer.