How Robotics is Assisting with High-Risk Tasks in Hazardous Environments? It’s a question that’s shaping the future of work, safety, and exploration. Forget the image of clunky, slow robots – we’re talking about sophisticated machines tackling jobs too dangerous for humans. From defusing bombs to exploring the deepest ocean trenches, robots are pushing boundaries and saving lives. This deep dive explores the tech, the challenges, and the incredible potential of robotic intervention in environments that would otherwise be off-limits.
This isn’t just about cool gadgets; it’s about fundamentally changing how we approach hazardous work. Think about the risks involved in nuclear cleanup, deep-sea exploration, or search and rescue operations. Robots, with their ability to withstand extreme conditions and perform complex tasks autonomously, are offering a safer and more efficient alternative. We’ll uncover the different types of robots used, the cutting-edge technology behind them, and the ethical considerations that come with deploying these incredible machines.
Introduction to Robotics in Hazardous Environments
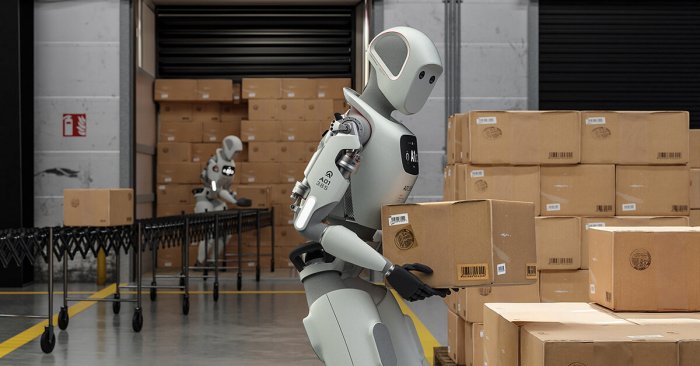
Source: designboom.com
Working in hazardous environments presents significant challenges to human workers. These environments, characterized by extreme conditions or the presence of dangers, pose risks of injury, illness, or even death. The inherent dangers often necessitate specialized, expensive, and time-consuming safety protocols, significantly impacting productivity and operational costs. Human error, despite rigorous training, remains a persistent factor, increasing the likelihood of accidents. The need for efficient and safe operation in these environments drives the adoption of robotic solutions.
The advantages of using robots for high-risk tasks are numerous and compelling. Robots can operate continuously without fatigue or the need for breaks, enhancing productivity and efficiency. They are unaffected by extreme temperatures, radiation, or toxic substances, making them ideal for environments too dangerous for humans. Their precision and repeatability minimize errors, leading to improved consistency and quality of work. Furthermore, robots can be remotely controlled, allowing human operators to remain at a safe distance, mitigating the risks to human life and health. The initial investment in robotic systems is often offset by long-term cost savings in safety measures, reduced downtime, and improved operational efficiency.
Examples of Hazardous Environments Utilizing Robots
Robots are deployed in a wide variety of hazardous environments to perform tasks deemed too dangerous for humans. These environments present unique challenges, requiring specialized robotic designs and control systems.
Nuclear power plants are one prime example. Robots are used for inspection, maintenance, and repair tasks inside the containment vessels, handling radioactive materials and operating in high-radiation areas. These robots are often equipped with radiation-hardened sensors and manipulators to withstand the harsh conditions. Similarly, robots are invaluable in disaster response scenarios, such as searching for survivors in collapsed buildings after earthquakes or exploring hazardous areas following chemical spills or industrial accidents. Their ability to navigate treacherous terrain and assess dangerous situations remotely provides invaluable support to emergency responders. Deep-sea exploration also heavily relies on robots, allowing scientists to study underwater volcanic vents or explore the ocean floor at depths inaccessible to human divers. These underwater robots, or remotely operated vehicles (ROVs), are equipped with specialized cameras and manipulators to collect samples and conduct research in extreme pressure and low-light conditions. Finally, the mining industry utilizes robots for tasks such as drilling, blasting, and transporting materials in underground mines, reducing risks to human miners from cave-ins, explosions, and exposure to harmful dust and gases. These robots are typically robustly built to withstand harsh conditions and operate autonomously or semi-autonomously.
Types of Robots Used in Hazardous Environments
Robots are increasingly vital in tackling hazardous environments, offering a safer alternative to human intervention. Their deployment significantly reduces risks to human life and allows for the completion of complex tasks previously deemed too dangerous. Different robot types are tailored to specific environmental challenges and operational needs.
Manipulators
Manipulators, essentially robotic arms, are designed for precise manipulation in hazardous settings. These robots excel at tasks requiring dexterity and control, such as handling radioactive materials, defusing bombs, or performing delicate repairs in confined spaces. Their strength lies in their ability to perform intricate movements with high accuracy, even in environments where human access is impossible or extremely risky. A key feature is their ability to be remotely controlled, allowing operators to maintain a safe distance while performing critical operations. Advanced manipulators often incorporate force feedback sensors, providing the operator with a sense of touch and enhancing the precision of the operation. For instance, manipulators are used in nuclear power plants to handle spent fuel rods, minimizing human exposure to radiation.
Mobile Robots, How Robotics is Assisting with High-Risk Tasks in Hazardous Environments
Mobile robots, including wheeled, tracked, and legged robots, navigate hazardous environments autonomously or with remote guidance. These robots are crucial for tasks such as exploration, inspection, and material transport in areas too dangerous for humans. Their mobility allows them to access remote or inaccessible locations, such as collapsed buildings after a disaster or the deep sea for underwater exploration. Features such as obstacle avoidance sensors, advanced navigation systems, and robust construction enable them to operate effectively in challenging terrains and conditions. For example, mobile robots equipped with cameras and sensors are used to inspect pipelines for leaks or structural damage, reducing the need for human entry into potentially hazardous environments.
Drones
Unmanned aerial vehicles (UAVs), commonly known as drones, offer a unique perspective in hazardous environments. Their aerial capabilities allow for inspection, surveillance, and data acquisition from a safe distance. Equipped with high-resolution cameras, thermal imaging, and other sensors, drones provide valuable information for tasks such as search and rescue operations, environmental monitoring, and infrastructure inspection. Their maneuverability and ability to access confined spaces make them particularly useful in situations where other robotic systems may be limited. For example, drones are used to inspect bridges and power lines, identifying potential hazards before they escalate into major incidents. This minimizes the risk to human inspectors and allows for proactive maintenance.
Robot Type | Application | Advantages | Limitations |
---|---|---|---|
Manipulator | Handling radioactive materials, bomb disposal, precise repairs | High dexterity, precise control, remote operation | Limited mobility, restricted reach, potential for damage in extreme environments |
Mobile Robot | Exploration, inspection, material transport in hazardous areas | Mobility, autonomous navigation, access to inaccessible locations | Slower speed compared to drones, potential for damage to the robot itself, limited dexterity |
Drone | Inspection, surveillance, data acquisition from a distance | Aerial perspective, maneuverability, access to confined spaces | Limited payload capacity, weather dependent, regulatory restrictions |
Applications of Robotics in High-Risk Tasks
Robots are increasingly vital in handling tasks too dangerous for humans, pushing the boundaries of what’s possible in hazardous environments. Their deployment significantly reduces risks to human life and allows for more efficient and thorough completion of challenging operations. These advancements are transforming industries and improving safety protocols across various sectors.
Bomb Disposal
Robots have become indispensable in bomb disposal, significantly reducing the risk to human bomb technicians. These robots, often equipped with manipulators, cameras, and X-ray systems, allow technicians to remotely assess and disarm explosive devices. A successful case study involves the use of a PackBot robot in Iraq, where it successfully neutralized numerous improvised explosive devices (IEDs), preventing numerous casualties. The robot’s ability to navigate complex terrains and handle delicate procedures proved crucial in these high-stakes situations. The PackBot’s small size and maneuverability allowed it to access tight spaces, while its robust construction ensured it could withstand the potential blasts of nearby detonations.
Nuclear Cleanup
The aftermath of nuclear accidents presents extremely hazardous environments requiring specialized robotic solutions. Robots are used for tasks such as inspecting damaged reactors, removing radioactive debris, and monitoring radiation levels. For example, during the Fukushima Daiichi nuclear disaster, robots played a crucial role in assessing the damage within the reactors, providing invaluable data for cleanup strategies. These robots, designed to withstand high levels of radiation, performed tasks that would have been impossible or far too dangerous for human workers. The data gathered by these robots allowed engineers to better understand the extent of the damage and develop safer and more effective cleanup procedures.
Deep-Sea Exploration
The crushing pressures and extreme conditions of the deep ocean make human exploration incredibly challenging. Remotely Operated Vehicles (ROVs) and Autonomous Underwater Vehicles (AUVs) are extensively used to explore the ocean depths, conduct scientific research, and perform underwater maintenance on oil rigs and pipelines. The exploration of the Titanic wreckage serves as a compelling example. ROVs equipped with high-definition cameras and manipulators allowed researchers to thoroughly document the wreck’s condition and recover artifacts, offering unprecedented insights into maritime history without risking human lives. The advanced imaging and data-gathering capabilities of these robots provided researchers with detailed information that would have been impossible to obtain through traditional methods.
Search and Rescue Operations
In disaster scenarios such as earthquakes, building collapses, or floods, robots can be deployed to search for survivors in dangerous and unstable environments. These robots, often equipped with cameras, sensors, and microphones, can navigate rubble, detect signs of life, and provide vital information to rescue teams. A notable example is the use of robots during the rescue efforts following the World Trade Center collapse. Robots were deployed to search for survivors in the unstable debris, allowing rescuers to work more safely and efficiently. The robots’ ability to access confined spaces and transmit real-time data proved invaluable in the search and rescue efforts. This technology drastically improved the efficiency and safety of search and rescue operations in a highly hazardous environment.
Typical Workflow of a Robotic System in a Hazardous Environment
The following flowchart illustrates a generalized workflow:
[Imagine a flowchart here. The flowchart would begin with “Mission Planning & Risk Assessment,” leading to “Robot Selection & Equipment Preparation.” This would branch to “Deployment to Hazardous Environment” and “Remote Operation & Data Acquisition.” “Data Analysis & Reporting” would follow, ultimately leading to “Mission Completion & Post-Mission Analysis.”]
Technologies Enabling Robotics in Hazardous Environments
Robots tackling perilous tasks in hazardous environments aren’t just brave; they’re technologically brilliant. Their ability to navigate and operate safely relies on a sophisticated interplay of advanced sensors, robust control systems, and cleverly engineered power sources. Let’s delve into the tech that makes it all possible.
The successful deployment of robots in hazardous environments hinges on their ability to perceive, understand, and react to their surroundings. This requires a powerful combination of hardware and software working in perfect harmony. The following sections explore the key technological components that empower these robotic heroes.
Robots are tackling dangerous jobs, from deep-sea exploration to nuclear cleanup, minimizing human risk. This shift towards automation mirrors the revolution happening in property transactions; check out how How Blockchain is Shaping the Future of Real Estate Transactions is increasing transparency and security. Ultimately, both robotics and blockchain aim to streamline complex processes and enhance safety, creating a more efficient and secure future for various industries.
Advanced Sensors for Perception and Navigation
Advanced sensors are the eyes, ears, and even touch sensors of robots operating in hazardous environments. They provide the crucial data needed for robots to understand their surroundings, avoid obstacles, and perform their tasks effectively. Cameras provide visual information, allowing robots to identify objects and navigate using visual cues. Lidar (Light Detection and Ranging) uses lasers to create detailed 3D maps of the environment, crucial for precise navigation, especially in cluttered or poorly lit areas. Sonar (Sound Navigation and Ranging) uses sound waves to detect objects, particularly useful underwater or in environments with limited visibility. These sensors work in concert, providing a comprehensive understanding of the robot’s environment, even in conditions that would be impossible for humans. For example, in a nuclear power plant, cameras might identify damaged pipes, while lidar would map the precise location and extent of the damage, guiding a repair robot.
Robust Control Systems and AI Algorithms for Autonomous Operation
Simply having sensors isn’t enough; robots need sophisticated control systems to process the sensory data and make intelligent decisions. Robust control systems ensure the robot’s stability and safe operation, even in unpredictable conditions. Advanced AI algorithms are vital for autonomous navigation, task planning, and decision-making. Machine learning algorithms allow robots to learn from experience, improving their performance over time. For instance, a robot tasked with defusing a bomb might use AI to analyze the bomb’s structure, identify potential hazards, and determine the safest course of action. The combination of robust control systems and AI ensures the robot can adapt to changing conditions and complete its task efficiently and safely.
Power Sources for Robots in Hazardous Environments
The choice of power source is critical for robots operating in hazardous environments. The ideal source must be reliable, safe, and suitable for the specific application. Several options exist, each with its own set of advantages and disadvantages:
The selection of a power source is critical, balancing energy density, operational lifespan, and safety considerations within the specific hazardous environment.
- Batteries (Lithium-ion, etc.): Offer high energy density and relatively long operational times, but have limited lifespans and may require frequent recharging or replacement. Their safety is also a concern, especially in environments with high temperatures or potential for damage.
- Fuel Cells (Hydrogen): Provide longer operational times compared to batteries and offer higher power output, but require safe storage and handling of hydrogen fuel, posing risks in certain environments.
- Tethered Power: Provides continuous power supply, eliminating the need for battery replacements or refueling, but limits the robot’s mobility and range of operation. This is often a practical solution in controlled environments like factories or mines.
- Nuclear Batteries (RTGs): Offer extremely long operational lifetimes and high power density, ideal for long-duration missions in remote or hazardous locations, but involve the handling of radioactive materials, necessitating stringent safety protocols.
Safety and Ethical Considerations
Deploying robots in hazardous environments offers immense potential, but it also introduces a complex web of safety and ethical challenges. Balancing the benefits of automation with the need to protect both human workers and the robots themselves requires careful consideration and robust protocols. The potential for accidents, malfunctions, and unforeseen consequences necessitates a proactive approach to risk management and ethical decision-making.
Potential Safety Risks
The integration of robots into hazardous environments presents a range of safety risks. These risks can be broadly categorized as those impacting human workers and those affecting the robots themselves. Failing to address these risks adequately can lead to serious injury, equipment damage, and project failure.
Human Safety Risks
Human safety remains paramount. Malfunctions in robotic systems, unexpected movements, or failures in safety mechanisms can directly endanger human personnel. For instance, a robotic arm malfunctioning during a demolition task could cause debris to fly unexpectedly, injuring nearby workers. Similarly, communication failures between a human operator and a remote-controlled robot could lead to errors with potentially disastrous consequences. Even seemingly minor issues, such as a robot unexpectedly shutting down in a confined space, could create hazardous conditions for human rescue teams.
Robotic Safety Risks
Protecting the robots themselves is also crucial, not only for economic reasons but also for operational continuity. Damage to a robot operating in a hazardous environment can lead to costly repairs or complete loss of the machine. Exposure to extreme temperatures, corrosive chemicals, or radiation can severely damage robotic components, reducing their lifespan and effectiveness. Furthermore, the very nature of hazardous environments (e.g., unstable terrain, unpredictable events) increases the risk of mechanical damage or failure.
Ethical Considerations
The deployment of robots in high-stakes situations, such as disaster response or bomb disposal, raises significant ethical concerns. Central to these concerns is the question of accountability in the event of an accident or failure. Determining responsibility when a robot malfunctions and causes harm becomes a complex legal and ethical issue. Furthermore, the use of AI-powered robots introduces the potential for biases embedded in the algorithms to influence decision-making, potentially leading to unfair or discriminatory outcomes. For example, an algorithm trained on biased data might prioritize rescuing individuals from one demographic over another in a disaster scenario.
Safety Protocols and Regulations
Numerous safety protocols and regulations are designed to mitigate the risks associated with robotic operations in hazardous environments. These include stringent testing and certification procedures for robotic systems, the implementation of multiple safety layers (e.g., emergency stops, redundant systems), and the development of comprehensive safety manuals and training programs for human operators. Regulations often mandate regular inspections and maintenance of robotic equipment, ensuring compliance with safety standards and minimizing the likelihood of malfunctions. Furthermore, risk assessments are frequently conducted to identify and address potential hazards before robotic deployment. These protocols, combined with strict adherence to safety procedures, aim to create a safer working environment for both humans and robots.
Future Trends and Developments
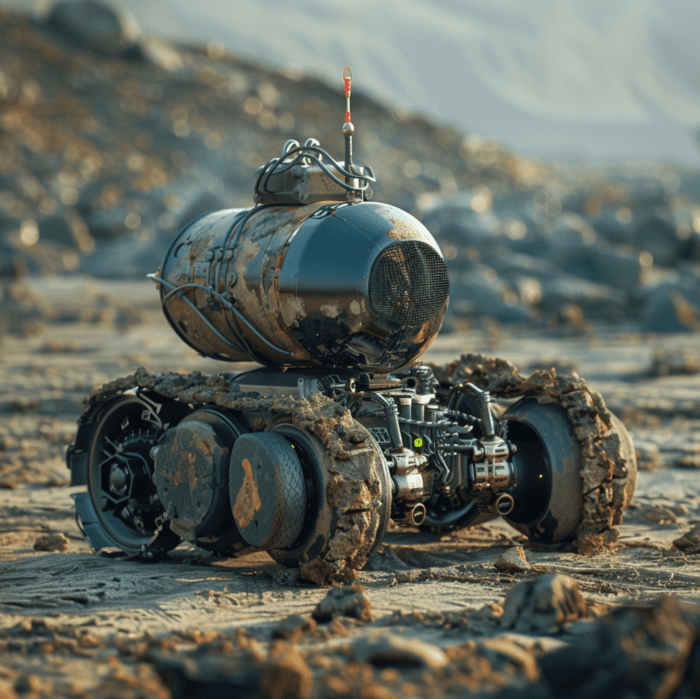
Source: website-files.com
The future of robotics in hazardous environments is bright, fueled by rapid advancements in various technologies. These innovations promise not only to enhance the capabilities of existing robotic systems but also to unlock entirely new possibilities for mitigating risks and improving worker safety across a range of industries. We’re on the cusp of a revolution where robots become increasingly sophisticated, autonomous, and collaborative, transforming how we approach dangerous tasks.
The convergence of several key technologies is driving this transformation. Advanced materials, for example, are enabling the creation of robots that are more resilient, durable, and adaptable to the harsh conditions found in hazardous environments. Simultaneously, breakthroughs in artificial intelligence and swarm robotics are paving the way for more complex and coordinated robotic operations, while advancements in human-robot collaboration are fostering safer and more efficient working relationships between humans and machines.
Advanced Materials and Enhanced Durability
The development of new materials is crucial for expanding the operational capabilities of robots in hazardous environments. Imagine robots constructed from advanced composites that can withstand extreme temperatures, pressures, and radiation levels far exceeding the limits of current materials. Such advancements would allow robots to operate in environments previously deemed inaccessible, such as nuclear power plants following accidents or deep-sea exploration in extreme pressure zones. For instance, the use of carbon nanotubes and graphene could lead to robots with significantly improved strength-to-weight ratios, enabling them to carry heavier payloads and navigate challenging terrains. Similarly, self-healing materials are being developed that can automatically repair minor damage sustained during operation, extending the lifespan and reliability of these robots.
Swarm Robotics and Coordinated Operations
Swarm robotics, inspired by the collective intelligence of insect colonies, offers a powerful approach to tackling complex tasks in hazardous environments. Instead of relying on a single, large robot, swarm robotics utilizes multiple smaller, simpler robots that cooperate to achieve a common goal. This approach offers several advantages: increased redundancy (if one robot fails, others can compensate), enhanced adaptability (the swarm can adjust to changing conditions), and the ability to tackle tasks that are too complex or dangerous for a single robot. Consider, for example, a swarm of robots working together to clean up a toxic spill or inspect a large-scale infrastructure project. Each robot could specialize in a specific task, working collaboratively to complete the operation efficiently and safely.
Human-Robot Collaboration and Enhanced Safety
The future of robotics in hazardous environments is not about replacing human workers but rather augmenting their capabilities. Human-robot collaboration (HRC) focuses on designing systems where humans and robots work side-by-side, leveraging the strengths of each. Robots can handle the most dangerous or physically demanding tasks, while humans retain control and oversight, providing expertise and judgment. This collaborative approach improves safety by reducing human exposure to hazardous conditions, while simultaneously increasing efficiency and productivity. For example, a human operator could remotely control a robot performing demolition work in a damaged building, reducing the risk of injury to the human worker. Advanced haptic feedback systems could further enhance this collaboration, allowing the operator to feel the forces and textures experienced by the robot, providing a more intuitive and effective control interface.
Impact on Various Industries
The advancements discussed above will have a profound impact across various sectors. In the nuclear industry, robots will play a critical role in decommissioning aging plants and handling radioactive materials. In oil and gas exploration, robots will enable safer and more efficient drilling operations in challenging environments. In disaster relief, robots will be invaluable for search and rescue operations, hazardous material handling, and infrastructure assessment. Even in less hazardous environments, the principles of HRC and swarm robotics can be applied to increase efficiency and safety in manufacturing, construction, and agriculture. The potential for improved worker safety, reduced downtime, and increased productivity is immense. For instance, construction sites could utilize collaborative robots to assist with heavy lifting and repetitive tasks, reducing the risk of workplace accidents and improving overall efficiency.
Illustrative Examples
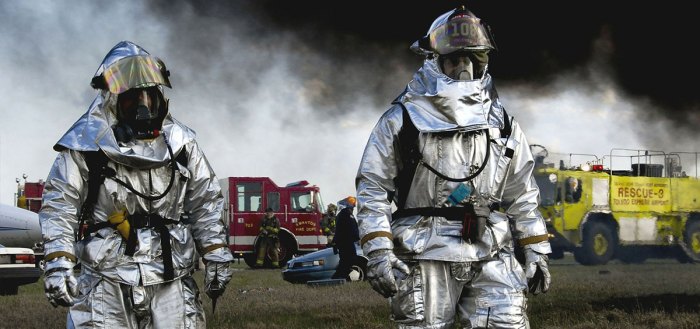
Source: sastrarobotics.com
Real-world applications showcase the transformative impact of robotics in hazardous environments. These examples highlight the diverse capabilities of robots and the critical roles they play in protecting human lives and ensuring efficient operations in challenging settings.
Let’s delve into specific scenarios to illustrate the practical benefits of robotic assistance in high-risk tasks.
Robot-Assisted Nuclear Waste Cleanup
Imagine a scenario inside the Chernobyl Exclusion Zone. Radiation levels are dangerously high, making human entry extremely risky. A specialized robotic arm, equipped with a high-resolution camera and radiation sensors, is deployed. The arm, roughly the size of a small car, is remotely controlled by an operator located several kilometers away in a shielded control room. The operator uses the camera feed to navigate the arm through the debris-strewn landscape, carefully maneuvering it to collect samples of radioactive material. The arm’s sensors constantly monitor radiation levels, providing real-time feedback to the operator. The robotic arm’s robust construction protects its internal components from radiation damage, while its multi-jointed design allows for precise manipulation in confined spaces. The samples collected are then carefully sealed and transported away for analysis, minimizing human exposure to dangerous radiation. The success of this operation highlights the potential of robotics to safely manage hazardous waste in high-radiation environments, preventing long-term health risks to human personnel.
Underwater Inspection with an Autonomous Underwater Vehicle (AUV)
Now, picture a different scene: a deep-sea oil rig experiencing a potential leak in a subsea pipeline. The water depth and strong currents make diving extremely dangerous for human divers. An Autonomous Underwater Vehicle (AUV), a torpedo-shaped robot approximately 3 meters long, is deployed. This AUV is equipped with sonar, high-definition cameras, and sensors to detect pressure, temperature, and chemical composition of the water. The AUV autonomously navigates to the pipeline using pre-programmed waypoints and its internal navigation system, adjusting its course to avoid obstacles. High-intensity underwater lights illuminate the pipeline, allowing the cameras to capture detailed images and video of the suspected leak area. The AUV’s sensors detect a slight increase in methane concentration near the pipeline, confirming the presence of a leak. This information is transmitted wirelessly to the surface, allowing engineers to assess the situation and plan a repair strategy, potentially preventing a major environmental disaster. The AUV’s ability to operate autonomously in harsh underwater environments saves time, reduces risk to human life, and provides crucial data for informed decision-making.
Closing Notes: How Robotics Is Assisting With High-Risk Tasks In Hazardous Environments
The integration of robotics into high-risk environments is not merely a technological advancement; it’s a revolution in safety and efficiency. As we’ve seen, the capabilities of these machines are constantly evolving, driven by advancements in AI, sensor technology, and materials science. From bomb disposal to deep-sea exploration, robots are rewriting the rules of engagement in hazardous environments, protecting human lives, and pushing the boundaries of what’s possible. The future is robotic, and it’s looking increasingly safer and more efficient.