The Role of Robotics in Revolutionizing Manufacturing Automation is no longer a futuristic fantasy; it’s the present, reshaping industries at breakneck speed. From the clunky automatons of yesteryear to the sleek, collaborative robots of today, the journey has been remarkable. This transformation isn’t just about faster production; it’s about smarter, more efficient, and ultimately, more sustainable manufacturing. We’re diving deep into this robotic revolution, exploring its impact, challenges, and the exciting future it promises.
This deep dive explores the various types of robots used in modern manufacturing, from the heavy-lifting industrial arms to the nimble collaborative bots working hand-in-hand (literally!) with human workers. We’ll examine the significant boost in productivity and efficiency these robots bring, while also acknowledging the challenges – like initial investment costs and workforce adaptation – and exploring solutions. Think skyrocketing ROI, minimized waste, and a whole new level of precision. But it’s not all sunshine and roses; we’ll also address the ethical considerations and the need for responsible implementation.
The Rise of Robotics in Manufacturing
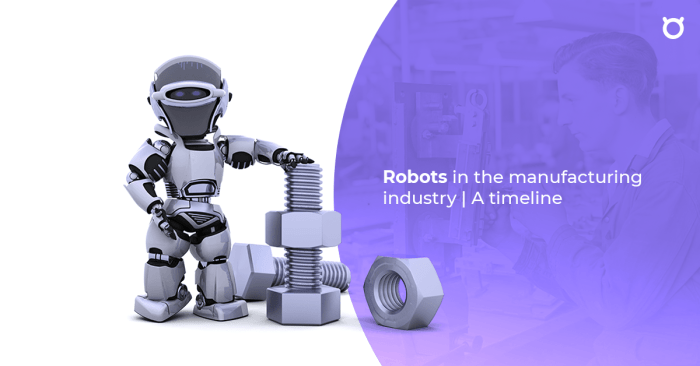
Source: provenrobotics.ai
Robotics is totally reshaping manufacturing, boosting efficiency and precision. This automation wave extends beyond factories; the same tech powers the rise of autonomous delivery, as explored in this insightful piece on The Rise of Autonomous Delivery Robots and Their Impact on Logistics. Ultimately, the advancements in robotics across various sectors promise a future of streamlined operations and smarter logistics, benefiting both production and consumption.
The integration of robots into manufacturing processes isn’t a futuristic fantasy; it’s a steadily unfolding revolution. From humble beginnings as simple programmable arms, robotics has dramatically reshaped how goods are produced, driving efficiency and impacting global economies. This evolution is marked by significant milestones and continues to accelerate at a breathtaking pace.
The adoption of robotics in manufacturing has been a gradual yet transformative process. Early industrial robots, appearing in the late 1950s and 1960s, were primarily used for simple, repetitive tasks like welding and painting. These early models lacked the sophistication and dexterity of their modern counterparts. However, they laid the groundwork for future advancements. Subsequent decades witnessed exponential growth in computing power, sensor technology, and artificial intelligence, leading to increasingly complex and adaptable robots capable of performing a wider array of tasks with greater precision and speed.
Robotics Adoption Across Manufacturing Sectors
The current state of robotics adoption varies significantly across different manufacturing sectors. Automotive manufacturing has historically been a major adopter, leveraging robots extensively for tasks such as assembly, painting, and welding. Electronics manufacturing, with its high-precision requirements and need for consistent quality, has also embraced robotics, particularly in areas like circuit board assembly and component placement. Other sectors, including food processing, pharmaceuticals, and logistics, are witnessing increasing adoption rates, driven by the need to improve efficiency, reduce costs, and enhance product quality. The trend is clear: robotics is no longer confined to a few specialized industries; its application is becoming increasingly widespread.
Economic Drivers of Increased Automation
The surge in automation within manufacturing is largely fueled by compelling economic incentives. Labor costs, particularly in developed nations, have risen steadily, making automation a cost-effective alternative for many businesses. Robots offer the advantage of 24/7 operation without breaks, overtime pay, or health benefits, leading to significant cost savings over the long term. Furthermore, robots can achieve higher levels of precision and consistency than human workers, reducing waste, improving product quality, and minimizing defects. This leads to reduced material costs and improved product yields, boosting profitability. The pursuit of increased productivity and competitiveness in the global marketplace further fuels the adoption of robotic automation. Companies are increasingly investing in robotics to maintain their competitive edge and meet the demands of a rapidly evolving global economy. For example, the rise of e-commerce has driven a need for faster and more efficient order fulfillment, leading to increased automation in warehousing and logistics.
Types of Robots Used in Manufacturing Automation
The rise of automation in manufacturing is inextricably linked to the diverse range of robots now deployed across various industries. From the precision of micro-assembly to the brute strength of heavy lifting, robots are reshaping the manufacturing landscape. Understanding the different types of robots and their specific capabilities is crucial for businesses seeking to optimize their production processes. This section will delve into the key robot types prevalent in modern manufacturing, highlighting their strengths and limitations.
Robot Type | Applications | Advantages | Disadvantages |
---|---|---|---|
Articulated Robots | Welding, painting, material handling, assembly, machine tending | High degree of freedom, versatility, high payload capacity (depending on model), can reach complex areas | Complex programming, can be expensive, potentially less precise than other types for delicate tasks |
SCARA Robots | Pick and place operations, assembly, packaging, electronic component insertion | Fast and precise movements in a horizontal plane, relatively simple programming, cost-effective for specific applications | Limited reach and dexterity outside the horizontal plane, less versatile than articulated robots for complex tasks |
Collaborative Robots (Cobots) | Machine tending, assembly, packaging, quality inspection, working alongside human operators | Safe interaction with humans, easy programming and deployment, relatively low cost, increased flexibility in production lines | Lower payload capacity compared to industrial robots, slower speeds than traditional robots, requires careful safety considerations |
Articulated Robot Capabilities and Limitations
Articulated robots, resembling a human arm, are characterized by their multiple rotating joints, granting them significant dexterity and reach. Their versatility makes them suitable for a wide array of tasks, from welding intricate parts to handling heavy materials. However, their complex design also leads to increased programming complexity and higher costs. Their precision can also be a limiting factor in highly delicate operations compared to other, more specialized robot types. For example, while capable of handling heavy car parts in assembly, they might not be the optimal choice for assembling microchips.
SCARA Robot Capabilities and Limitations
SCARA robots excel in tasks requiring fast and precise movements within a horizontal plane. Their simple design and relatively straightforward programming make them a cost-effective solution for high-speed pick-and-place operations, particularly in electronics manufacturing and packaging. However, their limited reach and dexterity outside the horizontal plane restrict their applications. They are not ideal for tasks requiring complex three-dimensional manipulation. Think of them as highly efficient for repetitive, planar tasks, but not suited for tasks requiring significant vertical movement or manipulation.
Collaborative Robot Capabilities and Limitations
Collaborative robots, or cobots, are designed for direct interaction with human workers. Their inherent safety features allow them to operate alongside humans without the need for extensive safety guarding, increasing production line flexibility. Cobots are relatively easy to program and deploy, making them attractive for smaller businesses and applications requiring quick setup. However, cobots typically have lower payload capacities and slower speeds than traditional industrial robots. Careful safety protocols and risk assessments are still essential to ensure a safe working environment, despite their inherent safety features. For instance, a cobot might assist in assembly but wouldn’t be appropriate for handling heavy machinery or materials.
Emerging Trends in Robotic Design and Functionality
The field of robotics is constantly evolving. Emerging trends include the development of more sophisticated AI-powered robots capable of learning and adapting to new tasks, robots with enhanced sensory capabilities for improved perception and interaction with their environment, and the increasing integration of robots into smart factories enabled by IoT technologies. We are also seeing a shift towards more modular and flexible robotic systems that can be easily reconfigured for different tasks, mirroring the increasing need for adaptable and agile manufacturing processes. Companies like Boston Dynamics are pushing the boundaries with increasingly advanced mobile robots capable of navigating complex environments, potentially revolutionizing logistics and material handling within manufacturing facilities.
Impact on Productivity and Efficiency
The integration of robotics into manufacturing has dramatically reshaped productivity and efficiency, leading to significant improvements across various metrics. This transformation isn’t just about faster production; it encompasses enhanced quality control, minimized waste, and ultimately, a stronger return on investment. Let’s delve into the specifics of how robots are revolutionizing the manufacturing landscape.
Robotics significantly boosts productivity by automating repetitive, high-precision tasks previously performed manually. This frees up human workers to focus on more complex and value-added activities, leading to overall operational improvements. The speed and accuracy of robotic systems are unparalleled, resulting in faster production cycles and reduced error rates. Furthermore, the consistent performance of robots ensures a higher level of quality control, minimizing defects and rework, which directly translates to cost savings.
Increased Production Speed and Throughput
Robotic automation significantly accelerates production processes. For instance, in automotive manufacturing, robotic welding systems can complete welds much faster than human welders, increasing vehicle production throughput considerably. Similarly, in electronics assembly, robots can perform intricate soldering and component placement tasks with exceptional speed and precision, leading to a substantial increase in the number of units produced per hour. The continuous operation of robots, without breaks or fatigue, further contributes to increased output. A study by the Boston Consulting Group estimated that the adoption of industrial robots can increase manufacturing output by 20-30% within 3-5 years.
Enhanced Quality Control and Reduced Defects
The precision and repeatability of robotic systems lead to a dramatic reduction in product defects. Robots perform tasks with consistent accuracy, eliminating human error which is a significant contributor to quality issues in many manufacturing processes. For example, in pharmaceutical manufacturing, robots handle delicate tasks like pill counting and packaging with impeccable precision, ensuring uniformity and minimizing the risk of contamination or errors. This increased quality translates directly into reduced waste, lower rework costs, and improved customer satisfaction. Furthermore, many robotic systems are equipped with sensors and vision systems that allow for real-time quality checks, instantly identifying and rejecting defective products.
Waste Reduction and Resource Optimization
Robotic automation contributes to significant waste reduction through improved precision and optimized material usage. Robots can perform tasks with minimal material waste, compared to manual processes that may involve more errors or less efficient material handling. For example, in cutting and shaping operations, robotic systems can precisely cut materials to the required dimensions, minimizing scrap and maximizing material utilization. This translates to direct cost savings on raw materials and reduced environmental impact through decreased waste disposal. Additionally, the optimized processes driven by robotics often lead to reduced energy consumption and lower overall operational costs.
Return on Investment (ROI) from Robotic Automation
While the initial investment in robotic systems can be substantial, the long-term ROI is often significant. The increased productivity, reduced labor costs, improved quality, and minimized waste contribute to a faster payback period. A typical ROI calculation would consider factors such as the initial investment cost, installation costs, maintenance costs, increased production output, reduced labor costs, and decreased waste. For example, a manufacturing plant automating a packaging line might see a 20% increase in output and a 15% reduction in labor costs, leading to a substantial ROI within a few years. Many case studies demonstrate that the ROI from robotic automation can exceed 100% over the lifespan of the robotic systems. Factors such as the specific application, the scale of implementation, and the efficiency of integration will influence the exact ROI achieved.
Addressing Challenges and Limitations
The seemingly unstoppable march of robotics in manufacturing isn’t without its hurdles. While the potential benefits are immense, successful implementation requires careful consideration of significant challenges related to cost, integration, and workforce adaptation. Overcoming these obstacles is crucial for realizing the full transformative power of robotic automation.
Integrating robotic systems into existing manufacturing processes isn’t a simple plug-and-play operation. It demands substantial upfront investment, encompassing not only the robots themselves but also specialized software, integration expertise, and potentially facility modifications. This high initial cost can be a major deterrent, particularly for smaller businesses or those with tighter budgets. Moreover, the complexity of integrating robots into pre-existing workflows can lead to unforeseen delays and increased expenses, necessitating careful planning and skilled technicians. The potential displacement of human workers is another significant concern, demanding proactive strategies for reskilling and workforce transition.
High Initial Investment Costs and Return on Investment (ROI)
The substantial capital expenditure required for robotic systems is a significant barrier to entry. Purchasing robots, integrating them into existing infrastructure, and training personnel all contribute to high upfront costs. However, a well-planned implementation can yield a strong return on investment (ROI) through increased productivity, reduced operational costs (such as labor and material waste), and improved product quality. For example, a car manufacturer might see a significant ROI within a few years by automating welding processes, leading to faster production times and fewer defects. Careful financial modeling and a clear understanding of long-term operational savings are crucial for justifying the initial investment.
Integration Complexities and System Compatibility
Integrating robots seamlessly into existing production lines can be a complex undertaking. This often requires modifications to the factory layout, specialized software development for robot control and data integration, and potentially the retraining of existing personnel. Compatibility issues between different robotic systems and existing machinery can also lead to significant delays and increased costs. A well-defined integration plan, involving careful assessment of existing infrastructure and thorough testing of the robotic system, is essential for minimizing disruptions and ensuring smooth operation. For instance, a company might need to upgrade its existing network infrastructure to accommodate the increased data flow generated by the robots.
Worker Displacement and Workforce Reskilling, The Role of Robotics in Revolutionizing Manufacturing Automation
The automation of manufacturing processes through robotics can lead to job displacement for some workers. This necessitates proactive strategies for workforce reskilling and upskilling to prepare employees for new roles within the automated environment. This could involve training programs focused on robot maintenance, programming, and system operation, as well as developing new skills relevant to other aspects of the manufacturing process. Companies that successfully navigate this transition often experience improved employee morale and increased productivity as workers adapt to new, more specialized roles. For example, a factory might retrain assembly line workers to become robot technicians or data analysts, creating new high-skilled jobs within the organization.
Robotic Malfunctions and Safety Concerns
Malfunctions in robotic systems can lead to production downtime, damage to equipment, and potentially injuries to workers. Implementing robust safety protocols, including emergency stop mechanisms, safety sensors, and protective barriers, is crucial for mitigating these risks. Regular maintenance and preventative measures, such as software updates and component inspections, can further minimize the likelihood of malfunctions. Furthermore, the use of advanced safety technologies, such as collaborative robots (cobots) designed to work safely alongside humans, can enhance workplace safety. For example, a manufacturing facility might use light curtains to create safety zones around robots, automatically halting operation if a worker enters the restricted area.
Human-Robot Collaboration Strategies
Effective human-robot collaboration is key to maximizing the benefits of robotic automation. This involves designing workspaces and processes that allow humans and robots to work safely and efficiently together. Cobots, with their inherent safety features and ability to work alongside humans without protective barriers, are becoming increasingly popular for collaborative tasks. Careful task allocation, where robots handle repetitive or hazardous tasks and humans focus on more complex or creative aspects of the process, can optimize productivity and job satisfaction. For instance, a company might use robots to handle heavy lifting and repetitive welding tasks, while humans oversee quality control and troubleshoot any issues.
The Future of Robotics in Manufacturing: The Role Of Robotics In Revolutionizing Manufacturing Automation
The integration of robotics in manufacturing is no longer a futuristic fantasy; it’s rapidly becoming the new normal. Looking ahead, we can envision a manufacturing landscape dramatically reshaped by advancements in artificial intelligence, machine learning, and collaborative robotics, leading to unprecedented levels of automation and efficiency. This shift will not only redefine production processes but also significantly impact the workforce and the global economy.
Imagine a sprawling factory of the future, a symphony of coordinated robots working in perfect harmony with human colleagues. Autonomous mobile robots navigate the factory floor, seamlessly transporting materials between workstations. Advanced AI-powered systems monitor production in real-time, predicting potential issues and optimizing processes before they become problems. Collaborative robots, or cobots, work alongside human workers, augmenting their capabilities and handling repetitive or dangerous tasks. This isn’t science fiction; elements of this vision are already being implemented in modern factories, and the pace of innovation suggests a complete transformation is within reach.
Technological Advancements in Manufacturing Automation
The next decade will witness a surge in several key technological advancements that will further propel the robotic revolution in manufacturing. These improvements will significantly enhance the capabilities and efficiency of robotic systems, leading to more flexible, adaptable, and intelligent factories.
One key area is the development of more sophisticated AI and machine learning algorithms. These advancements will allow robots to learn from experience, adapt to changing conditions, and perform more complex tasks with greater autonomy. For instance, robots will be able to identify and resolve unforeseen issues on the production line, minimizing downtime and maximizing output. Furthermore, the integration of advanced sensor technologies, such as computer vision and tactile sensing, will enable robots to perceive and interact with their environment with greater precision and dexterity. This will be crucial for handling delicate or complex components, opening up new possibilities for automation in industries currently reliant on manual labor.
Another significant advancement will be the proliferation of collaborative robots (cobots). Cobots are designed to work safely alongside human workers, enhancing productivity and efficiency without replacing human involvement. Their increasing affordability and ease of programming will make them accessible to a wider range of manufacturers, accelerating the adoption of automation across various industries. For example, imagine a cobot assisting a human worker in assembling intricate electronic components, handling the repetitive tasks while the human focuses on quality control and more complex aspects of the assembly process. This collaborative approach ensures the strengths of both humans and robots are leveraged for optimal results.
Societal Implications of Widespread Robotic Automation
The widespread adoption of robotic automation in manufacturing will undoubtedly have profound societal implications. While increased productivity and efficiency are clear benefits, the potential displacement of human workers is a serious concern that needs careful consideration. This necessitates proactive measures, such as retraining programs and investment in new job creation in sectors that complement and leverage robotic technologies. The focus should shift from simply replacing human workers to augmenting their capabilities and creating new, higher-skilled roles within the manufacturing ecosystem.
Furthermore, the increased efficiency and automation will likely lead to changes in global manufacturing patterns. Countries with advanced robotic technologies and skilled workforces will likely gain a competitive advantage, while others may face economic challenges. This necessitates international collaboration and strategies to ensure a just and equitable transition for all nations. For instance, governments could invest in education and training programs to prepare workers for the changing job market, fostering a workforce capable of operating and maintaining advanced robotic systems. This proactive approach will help mitigate the potential negative consequences of widespread automation and ensure a smoother transition to a more automated future.
Case Studies
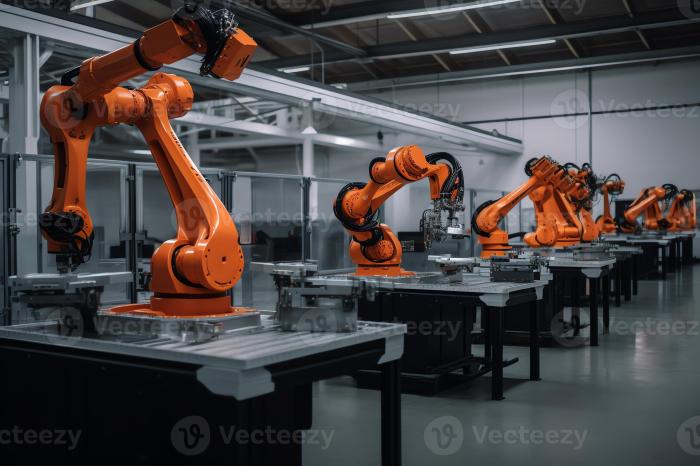
Source: vecteezy.com
Real-world examples showcase the transformative power of robotics in manufacturing. Let’s delve into specific instances where robotic implementation yielded significant improvements, highlighting both successes and contrasting approaches.
FANUC’s Impact on Toyota’s Production
FANUC, a leading robotics company, has a long-standing partnership with Toyota. Their collaboration demonstrates the profound impact of integrated robotic systems on automotive manufacturing. Toyota’s extensive use of FANUC robots across its assembly lines has resulted in dramatically increased production rates, improved product quality, and enhanced worker safety. Specific metrics are difficult to obtain publicly due to competitive reasons, but industry analysts estimate that the integration of FANUC’s robots has contributed to a significant percentage increase in Toyota’s overall manufacturing efficiency, measured in units produced per hour and defect rates reduced by double digits. This collaboration is a testament to the synergy between a top-tier robotics provider and a global automotive giant, demonstrating the scalability and reliability of advanced robotic automation in high-volume production environments. The consistent deployment of robots across multiple Toyota plants showcases the long-term commitment to robotic automation for sustained improvements in efficiency and output.
Comparison: Tesla vs. Ford Robotics Strategies
The adoption of robotics in electric vehicle (EV) manufacturing presents a compelling comparison. Tesla and Ford, while both utilizing robots extensively, have taken distinct approaches.
The key differences in approach and outcomes are:
- Tesla: Emphasizes highly flexible, adaptable robotic systems integrated with AI-driven control systems. This allows for rapid reconfiguration of production lines to accommodate new models or production changes. The outcome has been a faster introduction of new vehicle models, but potentially higher initial investment costs and a steeper learning curve for maintenance and programming.
- Ford: Focuses on a more traditional, modular robotic approach, prioritizing reliability and proven technology. This approach generally leads to lower initial investment costs and easier maintenance, but may offer less flexibility in adapting to rapid changes in product design or production volume. The outcome is a more stable, predictable production process, but potentially slower adaptation to new technologies and market demands.
Innovative Manufacturing Techniques Enabled by Robotics
Robotic automation has fueled innovations in several key areas. One prime example is the rise of additive manufacturing, or 3D printing, on an industrial scale. Robots are now used to precisely control the deposition of materials in 3D printing processes, leading to more complex and intricate part designs previously impossible with traditional subtractive manufacturing methods. This has enabled the creation of lighter, stronger, and more customized products, leading to improved performance and reduced material waste. Another example is the implementation of collaborative robots (cobots) working alongside human workers. This has not only improved efficiency but has also allowed for more ergonomic workspaces and reduced the risk of repetitive strain injuries for human employees. Cobots are particularly useful in tasks requiring precision and dexterity, such as assembly or inspection, where human oversight is still valuable. The development of advanced sensor technologies integrated with robots has also enabled the creation of “smart factories,” where real-time data analysis leads to optimized production schedules, predictive maintenance, and improved overall operational efficiency.
Safety and Ethical Considerations
The integration of robots into manufacturing, while promising increased productivity and efficiency, necessitates a careful consideration of safety and ethical implications. Ignoring these crucial aspects can lead to accidents, worker displacement, and social unrest. A proactive approach, incorporating robust safety protocols and ethical frameworks, is paramount for the successful and responsible implementation of robotic automation.
Safety protocols and ethical considerations are intertwined. A safe working environment, achieved through proper implementation of safety standards, is a prerequisite for ethical operation. Conversely, an ethical approach to automation prioritizes worker well-being and societal impact, influencing the design and deployment of safety measures.
Industrial Robot Safety Protocols and Regulations
Stringent safety protocols and regulations are crucial for mitigating risks associated with industrial robots. These range from physical barriers and emergency stop mechanisms to sophisticated sensor systems and risk assessments. Compliance with standards like those set by ISO (International Organization for Standardization) and OSHA (Occupational Safety and Health Administration) is mandatory in many countries. These regulations often specify requirements for robot design, installation, operation, and maintenance, aiming to minimize the potential for accidents involving humans and robots collaborating in the same workspace. For instance, light curtains and pressure-sensitive mats can detect human presence and trigger an automatic robot shutdown. Furthermore, regular maintenance and thorough risk assessments are critical for identifying and addressing potential hazards before they materialize.
Ethical Implications of Automation in Manufacturing
The rise of robotics in manufacturing raises significant ethical concerns, primarily centered on job displacement and the need for workforce retraining. While automation boosts productivity, it simultaneously displaces human workers from certain roles. This displacement can lead to unemployment, economic hardship, and social inequality. Addressing this challenge requires a proactive approach, including investing in retraining programs that equip displaced workers with the skills needed for emerging roles in the automated manufacturing environment, such as robot maintenance and programming. Furthermore, ethical considerations extend to the equitable distribution of the benefits of automation, ensuring that the gains are not concentrated solely in the hands of a few, while others bear the brunt of job losses. A just transition, prioritizing human well-being alongside technological advancement, is essential.
Best Practices for Safe and Ethical Robotics Implementation
Implementing robotics in manufacturing ethically and safely requires a multi-faceted approach. This includes thorough risk assessments prior to deployment, ensuring compliance with all relevant safety regulations, and investing in comprehensive training programs for both robot operators and maintenance personnel. Furthermore, open communication and collaboration between management, workers, and stakeholders are crucial. Transparency about automation plans, coupled with proactive efforts to address worker concerns, can build trust and foster a smoother transition. Companies should also consider incorporating ethical considerations into the design and development phases of robotic systems, prioritizing worker safety and minimizing potential negative societal impacts. Regular audits and continuous improvement processes can ensure ongoing compliance with safety and ethical standards. Finally, investing in research and development focused on human-robot collaboration technologies that prioritize safety and minimize the risk of job displacement is vital for a future where humans and robots work together harmoniously.
Final Review
The integration of robotics in manufacturing isn’t just a trend; it’s a fundamental shift. While challenges remain, the potential benefits – increased productivity, enhanced quality, and a safer work environment – are undeniable. The future of manufacturing is undeniably robotic, promising a more efficient, innovative, and potentially even more human-centric industry. The key lies in embracing the change, adapting to the new landscape, and ensuring ethical and responsible implementation for a future where humans and robots work together seamlessly.