How Robotics is Transforming the Future of Smart Manufacturing? Forget clunky assembly lines; the future of production is here, and it’s robotic. We’re talking about a revolution where machines aren’t just tools, but intelligent partners boosting efficiency, quality, and safety in ways you wouldn’t believe. Get ready for a deep dive into the smart factory, where robots aren’t just replacing humans, but empowering them.
This isn’t your grandpa’s factory. We’ll explore how robotic automation is supercharging productivity, crafting consistently perfect products, and making manufacturing safer than ever. We’ll also uncover the surprising ways AI and other smart technologies are working hand-in-hand with robots to create a truly interconnected and adaptable manufacturing ecosystem. Prepare to be amazed by the speed, precision, and intelligence of the modern smart factory.
Increased Efficiency and Productivity in Smart Manufacturing
Robotic automation is revolutionizing smart manufacturing, significantly boosting efficiency and productivity. The integration of robots into various manufacturing processes is streamlining operations, reducing lead times, and ultimately increasing output. This shift is driven by the robots’ ability to perform repetitive tasks with unwavering precision and speed, far surpassing human capabilities in certain areas. The result is a more agile and responsive manufacturing environment, better equipped to meet the demands of a dynamic global market.
Robotic automation improves manufacturing speed and output by automating repetitive, high-precision tasks previously performed manually. This translates to faster production cycles and a higher volume of goods produced within the same timeframe. Traditional methods, relying heavily on human labor, are inherently limited by factors such as fatigue, error rates, and the need for breaks. Robots, on the other hand, operate continuously, minimizing downtime and maximizing output. For instance, in the automotive industry, robots are extensively used for welding, painting, and assembly, resulting in significant improvements in production speed and quality. In electronics manufacturing, robots excel at tasks such as component placement and soldering, ensuring high precision and consistency. The food processing industry leverages robots for tasks like packaging and palletizing, increasing efficiency and hygiene standards.
Robotic Applications Across Manufacturing Sectors, How Robotics is Transforming the Future of Smart Manufacturing
The application of robotics varies widely across different manufacturing sectors, tailored to the specific needs and challenges of each industry. The common thread, however, is the enhancement of efficiency and productivity through automation. Here are a few prominent examples:
- Automotive: Robots perform welding, painting, assembly, and material handling, increasing production speed and consistency.
- Electronics: High-precision robots are crucial for component placement, soldering, and testing, minimizing errors and ensuring product quality.
- Food Processing: Robots handle packaging, palletizing, and material transfer, improving hygiene and efficiency.
- Pharmaceuticals: Robots assist in precise medication dispensing, packaging, and quality control, ensuring accuracy and sterility.
- Logistics and Warehousing: Robots automate tasks such as picking, packing, and sorting, optimizing warehouse operations and reducing labor costs.
Cost-Effectiveness of Robotic Systems vs. Human Labor
The decision to implement robotic systems involves a careful evaluation of costs and return on investment. While the initial investment in robotics can be substantial, the long-term benefits often outweigh the initial expense. The following table provides a simplified comparison, acknowledging that actual figures vary significantly depending on the specific robot, application, and operational context.
Smart manufacturing’s future hinges on robotics, automating processes and boosting efficiency. This tech-driven evolution mirrors the exciting advancements in other fields, like education, where immersive learning is revolutionized. Check out how augmented reality is shaping the future of learning by reading this insightful article: The Future of Augmented Reality in Education and Learning. Ultimately, both robotics in manufacturing and AR in education highlight a common thread: technology’s power to transform how we work and learn.
System Type | Initial Cost (USD) | Maintenance Cost (USD/year) | ROI (Years) |
---|---|---|---|
Simple Robotic Arm (e.g., for pick-and-place) | 20,000 – 50,000 | 2,000 – 5,000 | 2-5 |
Advanced Robotic System (e.g., for welding or painting) | 100,000 – 500,000 | 10,000 – 25,000 | 3-7 |
Automated Guided Vehicle (AGV) | 30,000 – 100,000 | 3,000 – 10,000 | 2-4 |
Human Labor (equivalent output) | (Salary & Benefits) | (Training & Benefits) | N/A |
Note: These figures are estimates and can vary greatly depending on specific factors. A comprehensive cost-benefit analysis is crucial before implementing robotic systems.
Case Studies Demonstrating Productivity Improvements
Several case studies highlight the quantifiable benefits of robotics in boosting manufacturing productivity. These examples demonstrate the tangible impact of robotic automation on efficiency and output.
- Company A (Automotive): Implemented robotic welding systems, resulting in a 25% increase in production output and a 15% reduction in defect rates.
- Company B (Electronics): Automated component placement using robots, leading to a 30% increase in production speed and a 10% reduction in labor costs.
- Company C (Logistics): Deployed AGVs in their warehouse, resulting in a 20% increase in order fulfillment speed and a 12% reduction in storage space requirements.
These are just a few examples of the many success stories showcasing the transformative potential of robotics in smart manufacturing. The consistent theme is a significant improvement in productivity, efficiency, and cost-effectiveness.
Enhanced Product Quality and Consistency
In today’s hyper-competitive manufacturing landscape, delivering consistently high-quality products is paramount. Robotics, with its inherent precision and repeatability, is revolutionizing quality control and pushing the boundaries of what’s achievable. This section explores how robotic systems are enhancing product quality and consistency in smart manufacturing.
Robotic precision and repeatability drastically reduce defects. Unlike human workers, robots don’t suffer from fatigue or inconsistencies in performance. They execute the same task repeatedly with unwavering accuracy, leading to a significant reduction in manufacturing errors. This translates directly to higher yields and lower scrap rates, boosting overall profitability. The integration of advanced vision systems and sensors further amplifies this effect, allowing for real-time monitoring and adjustments, ensuring consistent output even in complex manufacturing processes.
Vision Systems and Sensor Integration in Quality Control
Vision systems, equipped with high-resolution cameras and sophisticated image processing algorithms, act as the “eyes” of the robotic system. They can inspect products for defects such as scratches, dents, misalignments, or inconsistencies in color or texture with incredible speed and accuracy far exceeding human capabilities. Data from these vision systems, combined with data from other sensors (e.g., force sensors, proximity sensors), provides a comprehensive picture of the product’s quality. This rich data stream allows for immediate feedback, enabling the robot to make adjustments in real-time or flag products for further inspection. For instance, a robotic arm equipped with a vision system might identify a slightly misaligned component on a circuit board and automatically adjust its position before proceeding with the assembly process, preventing a potential defect.
Comparison of Traditional and Robotic Quality Control
Traditional quality control methods often rely on manual inspection, which is time-consuming, prone to human error, and often limited in scope. Sampling techniques are used, meaning that not every product undergoes rigorous inspection. Robotic-driven quality control, in contrast, offers 100% inspection in many cases. Robots can inspect every single product at every stage of the manufacturing process, identifying defects that might otherwise go unnoticed. This leads to significantly higher levels of quality and consistency. Moreover, robotic systems can collect and analyze vast amounts of data, providing valuable insights into the manufacturing process itself, enabling proactive adjustments to prevent future defects. This data-driven approach to quality control allows for continuous improvement and optimization of the manufacturing process.
Robotic Quality Inspection Process Flowchart
The following illustrates the typical steps in a robotic quality inspection process:
Raw Material Input –> Material Handling and Staging –> Robotic Inspection (Vision Systems and Sensors) –> Data Analysis and Defect Identification –> Defect Classification and Sorting –> Rework or Rejection –> Final Product Verification –> Packaging and Shipping
Improved Safety and Working Conditions
The integration of robots into smart manufacturing facilities isn’t just about boosting efficiency; it’s fundamentally reshaping workplace safety. By automating hazardous tasks and minimizing repetitive motions, robots are creating a safer and healthier environment for human workers, leading to a significant reduction in workplace accidents and improved overall well-being. This shift towards robotic automation represents a crucial step towards a more sustainable and humane manufacturing landscape.
Robots are adept at handling tasks that are inherently dangerous for humans. This includes working in extreme environments with high temperatures, toxic chemicals, or significant physical risks. For example, robots are increasingly used in welding operations, where sparks and intense heat pose a constant threat to human workers. Similarly, robots are employed in handling radioactive materials or working in confined spaces, significantly reducing the risk of exposure to hazardous substances or physical injury. The automotive industry, in particular, has extensively utilized robots for tasks such as painting car bodies (eliminating exposure to harmful solvents) and spot welding (reducing the risk of burns and electric shocks).
Hazardous Task Automation Examples
Robots effectively mitigate risks in several high-hazard industries. In the nuclear power industry, robots are deployed for tasks such as inspecting and maintaining equipment in highly radioactive areas, minimizing human exposure to harmful radiation. In the chemical processing industry, robots handle the mixing and transfer of hazardous chemicals, reducing the risk of spills and exposure. Furthermore, in demolition and construction, robots can safely dismantle hazardous structures, minimizing the risks associated with implosion and material handling. These examples showcase the transformative impact of robots in creating safer working environments across diverse sectors.
Ergonomic Benefits of Robotic Automation
Repetitive strain injuries (RSIs) are a significant concern in many manufacturing settings. Tasks involving repetitive movements, such as assembly line work or packaging, can lead to long-term musculoskeletal problems for workers. Robotic automation effectively addresses this issue by taking over these repetitive tasks, freeing up human workers for more engaging and less physically demanding roles. This reduces the incidence of RSIs, improving worker health and well-being and decreasing healthcare costs associated with work-related injuries. The ergonomic benefits extend beyond the elimination of repetitive strain; robots can also assist in lifting heavy objects, minimizing the risk of back injuries and other musculoskeletal problems.
Safety Features and Protocols for Human-Robot Collaboration
Safe human-robot collaboration is paramount in smart manufacturing. Implementing robust safety protocols and features is crucial to prevent accidents and ensure a harmonious working environment.
The implementation of effective safety measures is essential for successful human-robot collaboration. This involves a multifaceted approach that includes:
- Safety Sensors and Emergency Stops: Robots are equipped with sensors to detect the presence of humans in their workspace, automatically slowing down or stopping to prevent collisions. Emergency stop buttons are strategically placed to allow immediate cessation of robot operation in case of unforeseen events.
- Speed and Force Limiting: The speed and force of robotic movements are carefully controlled to minimize the risk of injury in case of contact with a human worker. These limitations are programmed to ensure that even accidental contact results in minimal impact.
- Protective Caging and Barriers: While not always necessary with collaborative robots, physical barriers or cages can be used to segregate robots from human workers in certain areas, particularly those involving high-speed or high-force operations.
- Robot Programming and Training: Thorough programming and regular maintenance are essential to ensure robots operate as intended and to prevent malfunctions. Comprehensive training for human workers on safe interaction procedures is also crucial.
- Risk Assessments and Safety Audits: Regular risk assessments and safety audits help identify potential hazards and implement necessary preventative measures. This continuous evaluation ensures that safety protocols remain effective and are adapted to evolving work processes.
Adaptability and Flexibility in Manufacturing Processes
The ability to swiftly adapt to fluctuating market demands is no longer a luxury but a necessity for modern manufacturers. Robotic systems, integrated with smart manufacturing principles, are at the forefront of this adaptability, offering unprecedented flexibility and efficiency in production lines. This adaptability stems from their inherent programmability and the integration of advanced technologies like AI and machine learning.
Robotic systems can be reprogrammed and reconfigured to adapt to changing product demands and manufacturing needs. This means that a single robotic cell can be easily adjusted to produce different products or handle variations in production volume, reducing the need for extensive capital investment in specialized equipment for each product line. This flexibility is achieved through modular design, where robotic arms, end-effectors (tools), and vision systems can be swapped or reprogrammed to suit the task at hand. For example, a flexible robotic cell used in automotive manufacturing might be configured to weld car bodies in the morning and then be reprogrammed in the afternoon to assemble dashboards, all within the same cell. The reprogramming often involves changing software parameters, adjusting the robot’s movements, and perhaps switching out the end-effector for a different tool. This eliminates the need to entirely rebuild the production line for each product variant.
Flexible Robotic Cells in Action
Flexible robotic cells are typically composed of several modular components. These include a programmable robot arm with multiple degrees of freedom, a vision system for part recognition and guidance, various end-effectors suited for different tasks (grippers, welding tools, etc.), and a control system integrating all components. The control system allows for seamless reprogramming and reconfiguration of the cell, enabling it to handle a wide variety of tasks. A common example is a robotic cell used in electronics assembly, where the robot might be programmed to pick and place components onto circuit boards, solder connections, and perform quality checks, all within a single, adaptable cell. The system can be reprogrammed to handle different circuit board designs and component types with minimal downtime.
The Role of AI and Machine Learning in Robotic Adaptation
The integration of AI and machine learning significantly enhances the adaptability of robotic systems. AI-powered robots can learn from data and adjust their actions accordingly, improving their performance over time. This learning capability enables robots to handle unforeseen situations and adapt to new tasks and environments without explicit reprogramming. For example, machine learning algorithms can be used to train a robot to identify and classify different parts, even if those parts have slight variations in shape or size. This eliminates the need for precise, pre-programmed instructions for each part and allows the robot to adapt to variations in incoming materials. Furthermore, AI can optimize the robot’s movements and actions, leading to increased efficiency and reduced production errors.
Hypothetical Scenario: Increased Demand for a Product Variant
Imagine a manufacturer producing two variants of a product, A and B, with a roughly equal demand. Suddenly, demand for variant A skyrockets. A traditional manufacturing line might struggle to meet this increased demand, potentially requiring significant investment in additional equipment. However, a smart manufacturing facility utilizing flexible robotic cells can adapt quickly. The robotic cells dedicated to variant A can be reprogrammed to operate at a higher speed or additional cells can be reconfigured from variant B production to handle the surge in demand for variant A. This dynamic allocation of resources, enabled by the flexibility of robotic systems and AI-driven optimization, ensures that the manufacturer can meet the increased demand without significant delays or additional capital expenditures. The AI could also analyze the production data to predict future demand fluctuations and proactively adjust the production schedule to prevent future bottlenecks.
Integration of Robotics with Other Smart Manufacturing Technologies
The true power of robotics in smart manufacturing isn’t just about individual robots performing tasks; it’s about their seamless integration into a larger, interconnected ecosystem. This ecosystem leverages the capabilities of other advanced technologies to create a truly intelligent and responsive manufacturing environment. The synergy between robotics and technologies like the Internet of Things (IoT), Big Data analytics, and cloud computing is driving unprecedented levels of efficiency and innovation.
Robotics, IoT, Big Data, and cloud computing work together to form a powerful synergy. Robots equipped with sensors constantly feed data into the system, providing real-time insights into production processes. This data is then analyzed using Big Data analytics to identify trends, predict potential issues, and optimize operations. Cloud computing provides the necessary infrastructure for data storage, processing, and sharing, enabling real-time collaboration and decision-making across the entire manufacturing network. This interconnected system allows for dynamic adjustments to production schedules, proactive maintenance, and improved overall efficiency.
Data-Driven Decision Making and Process Optimization
Data collected from robots, such as production rates, error rates, and equipment performance, is crucial for improving decision-making and process optimization. Imagine a robotic arm assembling circuit boards. Sensors embedded in the arm and the workpieces collect data on assembly speed, accuracy, and any potential malfunctions. This data is then transmitted to a central data analytics platform, which uses algorithms to identify bottlenecks, predict maintenance needs, and suggest improvements to the assembly process. For instance, if the system detects a higher-than-average error rate in a specific step, it can alert human operators and recommend adjustments to the robot’s programming or the workpiece design. This proactive approach minimizes downtime, reduces waste, and ensures consistent product quality. The data also informs longer-term strategic decisions, such as optimizing production schedules based on predicted demand and resource availability.
A Smart Factory Floor: A Visual Representation
Picture a modern, brightly lit factory floor. Sleek, collaborative robots, painted a vibrant yellow, work alongside human operators. These robots, with their six-axis arms and advanced grippers, are not enclosed in cages but operate safely within designated zones, their movements monitored by a network of sensors. These sensors, including proximity sensors, vision systems, and force/torque sensors, constantly gather data on the robots’ performance, the environment, and the condition of the equipment. The data is transmitted wirelessly via a robust IoT network to a central data analytics platform, housed in a secure server room. This platform uses sophisticated algorithms to analyze the data in real-time, generating visualizations and insights that are displayed on large screens throughout the factory. Human operators, equipped with augmented reality headsets, can interact with the system, receiving real-time updates and making informed decisions. The factory floor itself is organized in a modular fashion, allowing for flexible reconfiguration based on production needs. The overall environment is clean, organized, and safe, reflecting the advanced automation and integration of technologies.
Challenges and Future Trends in Robotics for Smart Manufacturing
The integration of robotics into smart manufacturing, while promising immense benefits, isn’t without its hurdles. Significant upfront investment, a shortage of skilled labor, and the ever-present threat of cybersecurity vulnerabilities all pose challenges to widespread adoption. However, exciting advancements in robotics technology are paving the way for a future where these challenges are mitigated, leading to even more efficient and innovative manufacturing processes.
Key Challenges in Robotics Implementation
Implementing robotics in smart manufacturing presents several significant obstacles. High initial capital expenditure is a major deterrent for many businesses, particularly smaller companies. Furthermore, the specialized skills needed to operate, maintain, and program these sophisticated systems are often lacking, creating a significant skill gap in the workforce. Finally, the increasing connectivity of robots within smart factories exposes them to potential cybersecurity threats, which can lead to production disruptions, data breaches, and even physical damage. Addressing these challenges is crucial for the successful integration of robotics into the manufacturing landscape.
Future Trends in Smart Manufacturing Robotics
The future of robotics in smart manufacturing is bright, driven by innovations in collaborative robots (cobots), AI-powered robots, and advanced sensor technologies. Cobots, designed to work safely alongside humans, are increasing flexibility and efficiency in collaborative workspaces. AI-powered robots are becoming more autonomous and adaptable, capable of learning and improving their performance over time, handling more complex tasks, and optimizing production processes. Advanced sensor technologies enable robots to perceive their environment with greater precision, leading to improved accuracy, safety, and responsiveness. These advancements are transforming the manufacturing landscape, making it more agile, efficient, and responsive to market demands. For example, Tesla’s use of AI-powered robots in its Gigafactories demonstrates the potential for increased automation and productivity.
Mitigation Strategies for Robotics Implementation Challenges
The following table Artikels potential solutions to the challenges of implementing robotics in smart manufacturing.
Challenge | Mitigation Strategy | Implementation Cost | Potential Benefits |
---|---|---|---|
High Initial Investment Costs | Lease or rent robots instead of purchasing them outright; explore government grants and subsidies; prioritize ROI on high-impact applications. | Variable, depending on chosen strategy; potentially lower than outright purchase. | Reduced upfront capital expenditure; access to advanced technology without significant initial investment; potential for faster ROI. |
Skill Gaps | Invest in training and development programs for existing employees; partner with educational institutions to develop specialized robotics curricula; recruit skilled technicians and engineers. | Moderate to high, depending on the scale of training and recruitment efforts. | Increased workforce skills and capabilities; improved robot utilization and maintenance; reduced downtime due to technical issues. |
Cybersecurity Concerns | Implement robust cybersecurity protocols, including network segmentation, intrusion detection systems, and regular software updates; conduct regular security audits and penetration testing. | Moderate to high, depending on the complexity of the implemented security measures. | Reduced risk of data breaches and production disruptions; enhanced data integrity and protection; improved overall factory security. |
Final Thoughts: How Robotics Is Transforming The Future Of Smart Manufacturing
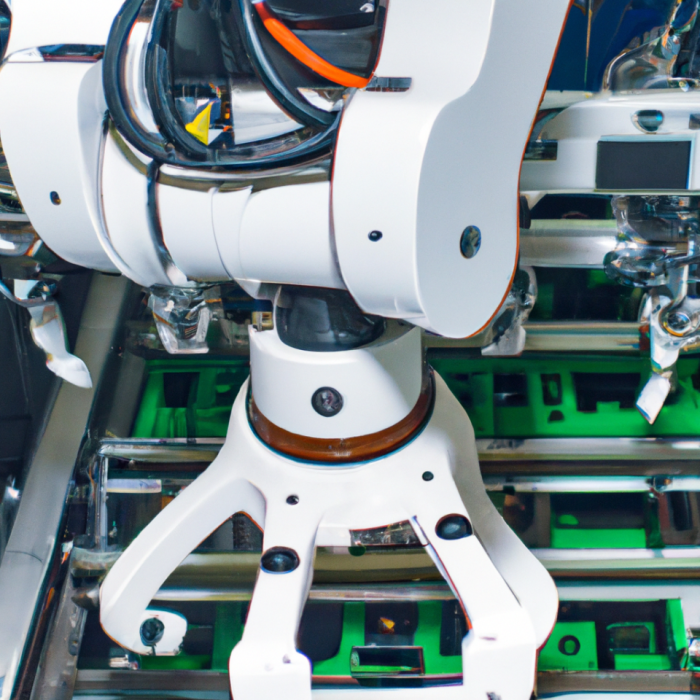
Source: robot.vin
The integration of robotics into smart manufacturing isn’t just a trend; it’s the future of production. From increased efficiency and higher quality products to enhanced safety and unparalleled adaptability, the benefits are undeniable. While challenges remain, the ongoing advancements in AI, collaborative robots, and sensor technologies promise an even brighter future where human ingenuity and robotic precision work together to create a truly revolutionary manufacturing landscape. The future is automated, and it’s looking incredibly efficient.