How Robotics is Redefining the Future of Industrial Automation? It’s not just about robots on assembly lines anymore. We’re talking collaborative robots (cobots) working *with* humans, AI-powered systems learning and adapting in real-time, and a complete overhaul of how we think about manufacturing, logistics, and even healthcare. This isn’t science fiction; it’s the rapidly evolving reality of today’s industrial landscape, impacting jobs, efficiency, and the very fabric of our working world. Get ready to dive into a future where humans and robots are partners in progress.
From the rise of collaborative robots seamlessly integrating into existing workflows to the sophisticated dance between AI and robotics, this technological revolution is reshaping industries at an unprecedented pace. We’ll explore the exciting possibilities, address the inevitable challenges, and ultimately paint a picture of a future where human ingenuity and robotic precision work hand-in-hand to drive innovation and productivity.
The Rise of Collaborative Robots (Cobots) in Industrial Settings
Forget the clunky, caged-in robots of yesteryear. The future of industrial automation is collaborative, and it’s happening now. Cobots, or collaborative robots, are changing the game, working alongside humans to boost productivity and improve safety. They’re smaller, more adaptable, and easier to program than their traditional counterparts, opening up a world of possibilities for businesses of all sizes.
Key Features and Benefits of Cobots Compared to Traditional Industrial Robots
Cobots are designed with safety as a paramount concern. Unlike traditional industrial robots, which often require safety cages to protect human workers, cobots are equipped with sensors and safety mechanisms that allow them to operate safely alongside people. This collaborative nature is their defining characteristic. They’re also generally easier to program and reprogram, requiring less specialized expertise. Their flexibility allows for quick adaptation to changing production needs, making them ideal for smaller batch sizes and customized production runs. This adaptability contributes to a significant reduction in downtime and overall improved efficiency. Furthermore, their smaller footprint means they can be integrated into existing production lines with minimal disruption.
Applications of Cobots Across Various Industries
The versatility of cobots extends across a wide range of industries. In manufacturing, they assist with assembly, welding, and material handling tasks, improving precision and speed. Logistics benefits from cobots for tasks like order picking and packing, increasing efficiency in warehouses and distribution centers. The healthcare sector is also seeing a rise in cobot adoption, with applications ranging from assisting surgeons in minimally invasive procedures to helping patients with rehabilitation exercises. Even the food and beverage industry utilizes cobots for tasks such as packaging and palletizing, ensuring consistent quality and speed. Amazon, for example, uses cobots extensively in their fulfillment centers, demonstrating their scalability and impact on large-scale operations.
Examples of Successful Cobot Implementments and Their Impact on Productivity and Safety
A Danish company, Universal Robots, is a leading manufacturer of cobots and has seen widespread adoption across numerous industries. Their cobots are used in automotive manufacturing for tasks like assembly and painting, resulting in increased production rates and reduced workplace injuries. Similarly, in the electronics industry, cobots are used for precise assembly tasks, minimizing errors and improving product quality. These examples showcase how cobots can not only increase productivity but also create a safer working environment for human employees by handling repetitive or hazardous tasks. The reduction in workplace accidents leads to lower insurance premiums and improved employee morale.
Cost-Effectiveness of Cobots Versus Traditional Robots, How Robotics is Redefining the Future of Industrial Automation
The initial investment in cobots is generally lower than that of traditional industrial robots. However, a complete cost analysis should also consider factors like maintenance, training, and integration costs. While maintenance for cobots can be less complex, leading to lower costs, training employees to operate cobots is typically simpler and quicker than training for traditional robots. This leads to faster return on investment (ROI).
Factor | Cobots | Traditional Robots |
---|---|---|
Initial Investment | Lower | Higher |
Maintenance | Lower | Higher |
Training | Easier and faster | More complex and time-consuming |
Integration | Simpler | More complex |
Advanced Robotics and AI Integration in Automation
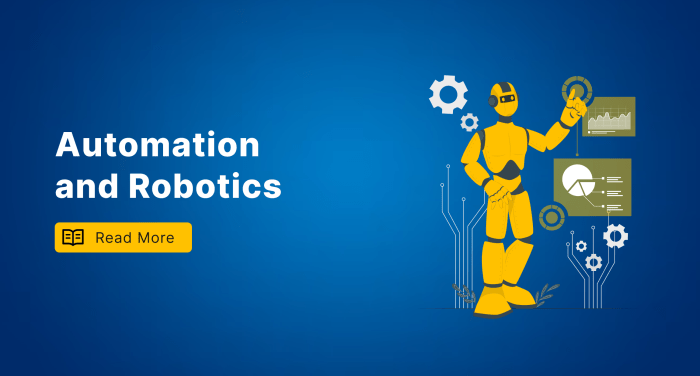
Source: dynocrm.com
Robots are revolutionizing industrial automation, boosting efficiency and precision like never before. But imagine training those robots, or designing complex assembly lines, using immersive simulations – that’s where the power of The Future of Virtual Reality in Creating Immersive Experiences comes in. This tech allows for cost-effective, risk-free training and design, ultimately enhancing the very future of robotic integration in factories.
The marriage of advanced robotics and artificial intelligence (AI) is revolutionizing industrial automation, pushing the boundaries of what’s possible and driving unprecedented levels of efficiency and precision. This synergy isn’t just about faster robots; it’s about robots that learn, adapt, and make intelligent decisions, leading to smarter, more responsive, and ultimately, more profitable operations.
AI significantly enhances the capabilities of industrial robots by imbuing them with cognitive functions previously exclusive to human operators. This allows for a level of automation previously unattainable, leading to increased productivity and reduced operational costs.
AI Enhancement of Industrial Robot Capabilities
AI empowers robots to handle complex and unpredictable tasks that were previously too challenging or economically unfeasible to automate. Through machine learning algorithms, robots can analyze vast datasets of sensor information, identifying patterns and making predictions to optimize their actions. This adaptive capability allows robots to adjust their behavior in response to changing conditions, ensuring consistent performance even in dynamic environments. For example, a robotic arm tasked with assembling electronics might learn to compensate for slight variations in component placement, reducing errors and improving throughput. This contrasts sharply with traditional robots which require precise, pre-programmed instructions and struggle with deviations from the norm.
Machine Learning for Optimized Robot Performance
Machine learning algorithms are the engine driving this adaptation. By analyzing operational data, these algorithms identify patterns and trends that optimize robot performance. This includes optimizing robot trajectories for faster cycle times, predicting potential equipment failures for proactive maintenance, and dynamically adjusting robot parameters to maximize efficiency based on real-time conditions. For instance, a robotic welding system could use machine learning to identify optimal welding parameters based on material type, thickness, and ambient temperature, ensuring consistent weld quality while reducing material waste.
Computer Vision and Sensor Technologies for Improved Precision and Decision-Making
Computer vision and advanced sensor technologies are crucial for enabling AI-powered robots to “see” and “understand” their environment. These systems provide the robots with a rich stream of data that informs their actions, allowing them to navigate complex spaces, identify objects, and make precise movements. For example, a robotic system equipped with 3D vision can accurately identify and pick parts from a bin of randomly oriented components, a task that was previously extremely difficult to automate. Similarly, force sensors allow robots to adjust their grip strength to avoid damaging delicate parts, enhancing the reliability and precision of their operations.
AI-Powered Robots Improving Efficiency in an Assembly Line
Consider an automotive assembly line. Traditional robotic systems perform repetitive, pre-programmed tasks. However, AI-powered robots can significantly enhance efficiency. Imagine a system where robots equipped with computer vision identify and sort components, dynamically adjusting their gripping mechanisms based on the component’s shape and size. These robots then work in conjunction with collaborative robots (cobots) to assemble the parts, with AI algorithms coordinating their movements to optimize the assembly process and ensure consistent quality. Machine learning algorithms analyze data from sensors monitoring the assembly process, identifying and correcting errors in real-time, minimizing production downtime and waste. This integrated AI-powered system leads to faster assembly times, improved product quality, and reduced production costs. The system can also predict potential bottlenecks or equipment failures, enabling proactive maintenance and preventing costly disruptions.
Impact on Human Workers and the Workforce
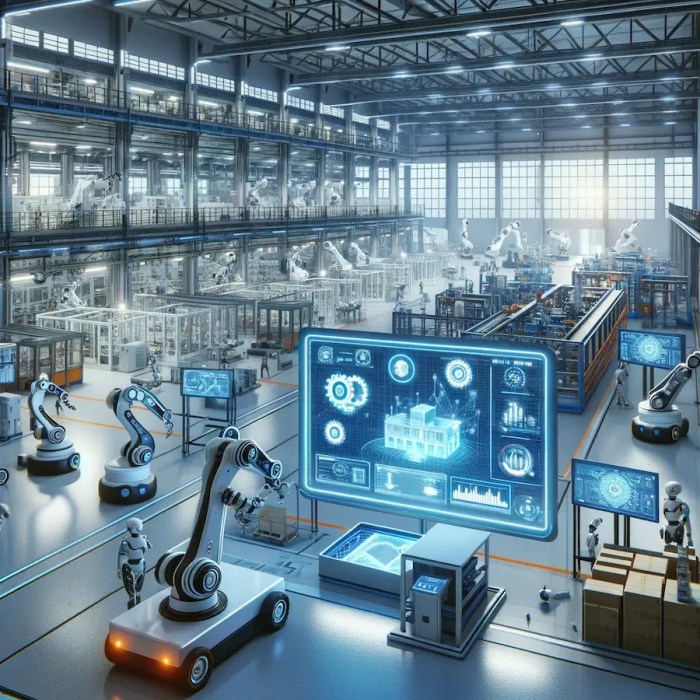
Source: techglints.com
The rise of robotics in industrial automation is undeniably transforming the landscape of work, sparking both excitement and apprehension. While the efficiency gains are significant, the impact on human workers requires careful consideration. The narrative isn’t simply one of robots replacing humans; it’s a complex interplay of displacement, adaptation, and the creation of entirely new opportunities.
The potential for job displacement due to automation is a legitimate concern. Repetitive, manual tasks, previously the domain of human workers, are increasingly being handled by robots, leading to workforce reductions in certain sectors. This is particularly evident in manufacturing, warehousing, and logistics, where robotic arms and automated guided vehicles are becoming commonplace. However, history shows that technological advancements, while initially disruptive, often create more jobs than they eliminate in the long run. The key lies in proactive adaptation and strategic reskilling.
Strategies for Workforce Reskilling and Upskilling
Addressing the potential for job displacement requires a proactive approach focused on equipping the workforce with the skills needed to thrive in the evolving job market. This involves a multi-pronged strategy encompassing government initiatives, industry partnerships, and individual commitment. Government-funded training programs can provide crucial support, focusing on areas such as robotics maintenance, programming, and data analysis – skills highly relevant to the new industrial landscape. Industries themselves can play a crucial role by investing in employee training and development programs, ensuring their workforce remains competitive. Finally, individual workers must embrace lifelong learning, actively seeking opportunities to acquire new skills and adapt to the changing demands of the job market. Examples of successful reskilling programs include those offered by manufacturing giants like Siemens and Bosch, which provide comprehensive training to their employees on the latest robotic technologies.
New Job Roles and Opportunities
The integration of robotics into industrial settings doesn’t just displace jobs; it creates them. The development, implementation, and maintenance of robotic systems require a skilled workforce. This includes roles such as robotics engineers, AI specialists, data scientists, technicians specializing in robot maintenance and repair, and even specialists in human-robot collaboration. The demand for these roles is expected to grow significantly in the coming years, presenting considerable opportunities for those willing to acquire the necessary skills. For example, the rapid growth of the e-commerce industry has fueled a significant demand for warehouse automation specialists, creating numerous high-skilled jobs in logistics and supply chain management.
Benefits of Human-Robot Collaboration
The future of industrial automation isn’t solely about robots replacing humans; it’s increasingly about humans and robots working together. This collaborative approach offers several benefits for workers:
- Reduced Workload: Robots can handle repetitive, strenuous tasks, freeing up human workers to focus on more complex and engaging activities.
- Improved Safety: Robots can undertake hazardous jobs, reducing the risk of workplace injuries for human employees. This is especially important in environments involving heavy machinery or toxic substances.
- Increased Productivity and Efficiency: Human-robot collaboration can significantly boost productivity and efficiency by optimizing workflows and reducing downtime.
- Enhanced Job Satisfaction: By automating tedious tasks, robots can make work more engaging and fulfilling for human employees, leading to higher job satisfaction and retention.
- Higher-Skill, Higher-Wage Jobs: The shift towards automation necessitates a workforce capable of managing and maintaining robotic systems, leading to the creation of higher-skilled, better-paying jobs.
The Future Trends in Industrial Robotics
The industrial robotics landscape is evolving at a breakneck pace, driven by advancements in artificial intelligence, machine learning, and materials science. We’re moving beyond the traditional, caged robots of yesteryear towards a future where robots are more collaborative, adaptable, and intelligent, seamlessly integrating into diverse industrial settings. This shift promises to reshape entire industries, creating new opportunities while simultaneously presenting unique challenges.
The integration of emerging technologies will be the key driver of this transformation, pushing the boundaries of what’s possible in industrial automation. These advancements aren’t just incremental improvements; they represent a paradigm shift in how we approach automation and manufacturing.
Emerging Technologies Revolutionizing Industrial Automation
Several groundbreaking technologies are poised to further revolutionize industrial automation. These advancements offer solutions to complex tasks previously considered impossible for robots, opening doors to new levels of efficiency and precision.
- Swarm Robotics: Imagine a coordinated team of small, relatively simple robots working together to accomplish a complex task, like inspecting a vast infrastructure or assembling intricate components. This distributed approach offers robustness and adaptability, as the failure of one robot doesn’t necessarily compromise the entire operation. Examples include collaborative drone swarms for infrastructure inspection or micro-robots working together in micro-assembly processes.
- Soft Robotics: Traditional industrial robots are rigid and often unsuitable for tasks requiring delicate handling or interaction with unpredictable environments. Soft robotics, utilizing flexible materials and compliant actuators, offer a solution. These robots can adapt to varying shapes and forces, making them ideal for applications like handling fragile objects, assisting in surgery, or working in unstructured environments. Consider the potential for soft robotic grippers handling delicate fruits in a food processing plant, or assisting in minimally invasive surgery.
- Artificial Intelligence (AI) and Machine Learning (ML): AI and ML are already transforming industrial robotics, enabling robots to learn from experience, adapt to changing conditions, and make decisions autonomously. This will lead to more flexible and efficient automation systems capable of handling complex and unpredictable tasks, ultimately reducing human intervention and increasing productivity. For example, AI-powered robots in a warehouse can learn optimal routes for picking and packing orders, adapting to changing inventory levels and customer demands.
Impact on Various Industries and Sectors
The impact of these advancements will be far-reaching, affecting various industries and sectors in profound ways.
- Manufacturing: Swarm robotics and soft robotics will enable the automation of complex assembly processes and the handling of delicate or irregularly shaped components. AI-powered robots will optimize production lines, predict maintenance needs, and improve quality control.
- Logistics and Warehousing: Autonomous mobile robots (AMRs) guided by AI will optimize warehouse operations, increasing efficiency and reducing labor costs. Drone swarms could revolutionize delivery systems, providing faster and more efficient transportation of goods.
- Agriculture: Robots equipped with AI and computer vision can automate tasks such as planting, harvesting, and weeding, increasing yields and reducing the need for manual labor. Soft robots could handle delicate fruits and vegetables without damage.
- Healthcare: Soft robotics and AI-powered surgical robots will improve the precision and accuracy of medical procedures. Robots could also assist with patient care and rehabilitation.
Ethical Considerations Surrounding Increased Robot Use
The increasing use of robots in the workplace raises several ethical considerations that require careful attention.
- Job Displacement: Automation has the potential to displace workers, necessitating retraining programs and social safety nets to support those affected.
- Algorithmic Bias: AI systems trained on biased data can perpetuate and amplify existing inequalities. It’s crucial to ensure fairness and transparency in the design and implementation of robotic systems.
- Data Privacy and Security: The increasing amount of data collected by robots raises concerns about privacy and security. Robust data protection measures are essential to prevent misuse or unauthorized access.
- Responsibility and Accountability: Determining responsibility in case of accidents or malfunctions involving robots is a complex issue that requires careful consideration of legal and ethical frameworks.
Projected Growth and Adoption of Industrial Robotics
A visual representation would show a steeply upward-sloping line graph, projecting the growth of industrial robot installations over the next decade. The x-axis would represent years (2024-2034), and the y-axis would represent the number of industrial robots installed globally (in millions). The line would start at a point representing the current number of installations and steadily increase, perhaps showing an exponential growth curve in the later years. Key data points could highlight projected milestones, such as the year in which a specific number of installations is reached. The graph could be color-coded to represent different robot types (e.g., collaborative robots, traditional industrial robots, mobile robots), showcasing the relative growth of each category. A legend would clearly explain the different lines and data points. The overall visual style would be clean and modern, using a clear color palette and minimal visual clutter to emphasize the data and its upward trend. The graph could also include annotations highlighting significant technological advancements or industry trends that contribute to the projected growth.
Addressing Challenges and Limitations in Robotic Automation: How Robotics Is Redefining The Future Of Industrial Automation

Source: zarantech.com
The rapid advancement of robotics in industrial settings is undeniably transformative, but the journey isn’t without its bumps. Implementing robotic systems presents a unique set of hurdles, ranging from significant upfront costs to complex integration processes and crucial cybersecurity concerns. Understanding these challenges is key to fostering wider adoption and realizing the full potential of robotic automation.
High Initial Investment and Ongoing Maintenance Costs
The cost of robotic automation is a significant barrier to entry for many businesses, particularly smaller companies. Initial investments include purchasing the robots themselves, which can range from tens of thousands to hundreds of thousands of dollars depending on complexity and capabilities. This cost doesn’t end with the purchase; substantial expenditures are required for installation, programming, and integration with existing infrastructure. Furthermore, ongoing maintenance, including regular servicing, software updates, and potential repairs, adds a considerable recurring expense. For example, a small manufacturing company might find the cost of a single advanced robotic arm prohibitive compared to employing human workers for a similar task, hindering the immediate adoption of automation despite long-term potential benefits. This economic reality necessitates careful cost-benefit analyses before implementing robotic systems.
Integration Complexity and Skilled Labor Requirements
Integrating robots into existing production lines isn’t a simple plug-and-play process. It demands significant expertise in robotics, programming, and industrial automation. Companies often need to invest in specialized training for their workforce or hire external consultants, adding to the overall cost. The integration process itself can be time-consuming and disruptive, potentially halting production while adjustments are made. Successfully integrating robots requires meticulous planning and coordination to ensure seamless interaction with existing equipment and processes. A poorly planned integration can lead to inefficiencies, downtime, and ultimately, a poor return on investment. Therefore, robust planning and skilled labor are indispensable for a successful robotic automation implementation.
Cybersecurity Risks and Mitigation Strategies
Industrial robots are increasingly connected to networks, making them vulnerable to cyberattacks. A successful attack could disrupt operations, compromise sensitive data, or even cause physical damage. The interconnected nature of modern industrial environments amplifies these risks, potentially creating cascading failures across multiple systems. Protecting robotic systems requires robust cybersecurity measures, including network segmentation, intrusion detection systems, and regular software updates. Furthermore, establishing clear security protocols and training employees on safe practices are crucial for minimizing vulnerabilities. The automotive industry, for instance, has seen instances where attempts to compromise connected robotic systems have been made, highlighting the urgent need for proactive cybersecurity measures in this sector.
Strategies for Overcoming Challenges and Promoting Wider Adoption
Several strategies can help overcome the challenges and accelerate the adoption of robotic automation. These include government incentives and subsidies to reduce initial investment costs, the development of more affordable and user-friendly robotic systems, and increased access to training and educational programs to develop a skilled workforce. Collaborative efforts between industry, academia, and government are essential for fostering innovation and developing standardized security protocols. Furthermore, promoting open-source robotics platforms can encourage greater participation and innovation, driving down costs and expanding accessibility. By addressing these challenges proactively, we can unlock the transformative potential of robotics and pave the way for a more efficient and productive industrial future.
Final Summary
The future of industrial automation is undeniably robotic, but it’s far from dystopian. By embracing the potential of collaborative robots, AI integration, and strategic workforce development, we can navigate the challenges and harness the immense power of this technological leap. The key lies in recognizing the symbiotic relationship between humans and robots, creating a future where technology empowers workers and drives unprecedented levels of efficiency and innovation across industries. The robots are coming, and they’re bringing a whole lot of opportunity with them.