The Role of Robotics in Redefining Manufacturing Efficiency is no longer a futuristic fantasy; it’s the present reality reshaping industries. From assembly lines humming with collaborative robots to warehouses navigating autonomous mobile units, robotics is revolutionizing how we produce goods. This isn’t just about increased speed; it’s about precision, consistency, and a whole new level of operational efficiency that’s pushing the boundaries of what’s possible. We’re diving deep into the heart of this transformation, exploring the different types of robots, their applications, and the challenges – and triumphs – of integrating them into the modern manufacturing landscape.
This deep dive will explore how robotics impacts key performance indicators (KPIs) like production output, defect rates, and cycle times. We’ll also examine the synergy between robotics and other automation technologies, like AI and the Internet of Things (IoT), while addressing the hurdles of implementation, including cost, integration, and workforce training. Prepare for a journey into the future of manufacturing – a future powered by intelligent machines.
The Evolving Landscape of Manufacturing
For centuries, manufacturing has been the backbone of economic growth, evolving from rudimentary handcrafts to complex, automated systems. The Industrial Revolution marked a pivotal shift, introducing mass production and the assembly line, dramatically increasing output and altering the very fabric of society. However, this progress wasn’t without its limitations. The 20th and early 21st centuries saw manufacturing grapple with increasing complexities, rising labor costs, and the ever-growing demand for customization and speed.
Traditional manufacturing processes, often reliant on manual labor and rigid, inflexible systems, faced significant challenges. Maintaining consistent quality across large production runs proved difficult, leading to higher rates of defects and wasted materials. Adapting to changing market demands and consumer preferences was a slow and expensive process, hindering competitiveness. Furthermore, maintaining a skilled workforce and ensuring workplace safety became increasingly pressing concerns. These factors combined to create a need for a more efficient, adaptable, and cost-effective approach to manufacturing.
The emergence of robotics offered a compelling solution to these challenges. Robots, initially deployed for simple, repetitive tasks, gradually evolved into sophisticated machines capable of performing complex operations with precision and speed far exceeding human capabilities. This technological advancement offered the potential to address many of the limitations of traditional manufacturing, paving the way for a new era of increased efficiency and productivity.
The Rise of Industrial Robots and Their Capabilities
The integration of industrial robots significantly enhanced manufacturing efficiency. Early robotic arms, primarily used for welding and painting, laid the foundation for more advanced applications. Modern robots are equipped with advanced sensors, sophisticated control systems, and artificial intelligence (AI), allowing them to perform a wide range of tasks, from intricate assembly processes to complex quality control inspections. For instance, in the automotive industry, robots are extensively used for welding car bodies, applying paint, and installing components with remarkable precision and speed, reducing production time and improving product quality. The development of collaborative robots, or “cobots,” further expanded the possibilities, enabling humans and robots to work safely and efficiently alongside each other on shared tasks.
Impact of Robotics on Manufacturing Efficiency Metrics
The impact of robotics on key manufacturing efficiency metrics is undeniable. Through automation of repetitive and dangerous tasks, robots reduce labor costs and improve workplace safety. Their precision and consistency lead to lower defect rates and reduced material waste. Furthermore, robots enable faster production cycles, allowing manufacturers to meet increasing demand and respond quickly to market changes. Consider a case study of a leading electronics manufacturer that implemented robotic assembly lines. The company reported a 25% increase in production output, a 15% reduction in defect rates, and a 10% decrease in labor costs within the first year of implementation. These quantifiable improvements demonstrate the significant positive impact of robotics on manufacturing efficiency.
Addressing Challenges in Robotic Integration
Despite the significant advantages, integrating robotics into manufacturing processes presents challenges. The initial investment costs for robots and related infrastructure can be substantial. Moreover, integrating robots requires specialized expertise for programming, maintenance, and troubleshooting. Furthermore, concerns about job displacement due to automation necessitate careful planning and workforce retraining initiatives. However, these challenges are being actively addressed through advancements in robot technology, the development of user-friendly programming interfaces, and the growth of collaborative robotics, which focuses on human-robot collaboration rather than complete replacement of human workers.
Types of Robots in Manufacturing and Their Applications
The rise of automation in manufacturing has led to a diverse range of robots, each designed for specific tasks and contributing uniquely to increased efficiency and productivity. Understanding these different types and their applications is crucial for businesses looking to optimize their production processes. This section will explore the key categories of robots currently transforming the manufacturing landscape.
Industrial Robots
Industrial robots are the workhorses of automated manufacturing. These are typically large, powerful, and highly precise robotic arms programmed to perform repetitive tasks with speed and accuracy. They’re often found working in isolated cells or cages for safety reasons. Their versatility allows them to be adapted for various applications through the use of different end-effectors (tools attached to the robot arm).
Industrial robots excel in high-volume, repetitive tasks where consistency and speed are paramount. For example, in automotive manufacturing, industrial robots are extensively used for welding car bodies, painting vehicles, and assembling components. Their precision ensures consistent quality across thousands of units, significantly improving production efficiency compared to manual labor. In electronics manufacturing, they handle delicate components with speed and precision, placing tiny parts onto circuit boards with incredible accuracy. This reduces the error rate, increases throughput, and ultimately lowers production costs.
Collaborative Robots (Cobots)
Unlike their industrial counterparts, collaborative robots, or cobots, are designed to work alongside human workers. They are smaller, lighter, and often equipped with safety features that allow them to operate in shared workspaces without the need for safety cages. Cobots are programmed to assist humans with tasks, not replace them entirely. This collaborative approach enhances productivity and allows for a more flexible manufacturing environment.
Cobots are particularly well-suited for tasks requiring human-robot interaction, such as assembly, machine tending, and quality inspection. In a manufacturing setting, a cobot might assist a worker by handing them tools, holding parts in place during assembly, or performing repetitive sub-tasks, freeing up the human worker to focus on more complex or value-added activities. For instance, in the food processing industry, cobots can assist in packaging or quality control, working alongside human inspectors to ensure product consistency and safety. Their collaborative nature allows for a more efficient workflow, combining the strengths of both human dexterity and robotic precision.
Autonomous Mobile Robots (AMRs)
Autonomous mobile robots (AMRs) are revolutionizing material handling in manufacturing facilities. Unlike automated guided vehicles (AGVs) which follow pre-programmed paths, AMRs use advanced sensors and AI to navigate dynamically around obstacles and people, creating a more flexible and efficient material flow. They can be programmed to transport materials, parts, and finished goods across a facility, optimizing logistics and reducing transportation time.
AMRs are particularly valuable in large manufacturing plants where materials need to be moved between different workstations or departments. Imagine a scenario in a large electronics factory where AMRs autonomously transport circuit boards between assembly lines, ensuring a continuous flow of materials without the need for human intervention. This not only improves efficiency but also reduces the risk of human error and accidents associated with manual material handling. Their flexibility and adaptability allow for efficient re-routing in response to changing production needs. They can also be integrated with other systems, such as warehouse management systems (WMS), for optimized material flow and inventory management.
Comparison of Robot Types
Robot Type | Capabilities | Limitations | Approximate Cost (USD) |
---|---|---|---|
Industrial Robot | High speed, precision, payload capacity; suitable for high-volume, repetitive tasks. | Requires safety cages; limited flexibility; high initial investment. | $50,000 – $250,000+ |
Collaborative Robot (Cobot) | Safe human-robot interaction; flexible deployment; easier programming. | Lower payload capacity than industrial robots; slower speed. | $25,000 – $75,000 |
Autonomous Mobile Robot (AMR) | Autonomous navigation; flexible routing; efficient material handling. | Requires sophisticated software and sensors; may be susceptible to environmental changes. | $15,000 – $50,000+ |
Impact of Robotics on Manufacturing Efficiency Metrics
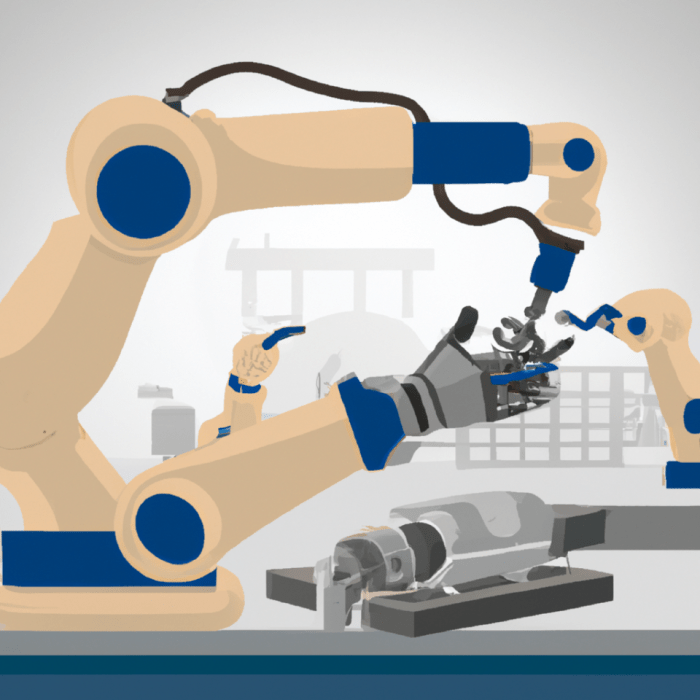
Source: robot.vin
The integration of robotics into manufacturing processes significantly impacts key performance indicators (KPIs), ultimately driving substantial improvements in overall efficiency. By automating tasks, robots enhance speed, precision, and consistency, leading to measurable gains across various aspects of production. Let’s delve into how specific KPIs are affected.
Manufacturing efficiency is often measured using a combination of metrics that reflect different aspects of the production process. Analyzing these metrics before and after robotic implementation provides a clear picture of the impact of automation.
Key Performance Indicators in Manufacturing
Several key performance indicators (KPIs) are crucial for evaluating manufacturing efficiency. These metrics provide a comprehensive assessment of the production process, allowing for informed decision-making and continuous improvement. Production output, defect rates, cycle times, and resource utilization are all critical factors.
Production Output
Robotics significantly boosts production output. Automated systems operate continuously, without breaks or fatigue, resulting in a higher volume of goods produced within a given timeframe. For example, a car manufacturing plant using robotic welding arms can complete more welding tasks per hour than a team of human welders, leading to a substantial increase in the number of cars produced daily. This increased output directly translates to higher profits and increased market share.
Defect Rates
Robots, programmed with high precision, consistently perform tasks according to specifications, minimizing errors and reducing defect rates. Unlike human workers, robots don’t suffer from fatigue or distractions, leading to fewer inconsistencies and a higher quality of output. A pharmaceutical company using robotic arms for precise pill dispensing will experience a dramatically lower rate of incorrect dosages compared to manual processes. This improved quality control reduces waste, rework, and customer complaints.
Cycle Times
Robotic automation drastically reduces cycle times—the time taken to complete a production cycle. Automated systems perform tasks faster and more efficiently than manual labor, accelerating the entire production process. Consider a factory using robots for palletizing finished goods. The robots can stack and wrap pallets much faster than human workers, reducing the time required for this stage of production and speeding up the overall delivery process.
Resource Utilization
Robotics improves resource utilization by optimizing the use of equipment, materials, and labor. Robots can work continuously, maximizing the utilization of machinery and reducing downtime. They also optimize material usage by minimizing waste and ensuring precise material handling. In a metal fabrication facility, robotic cutting systems precisely cut materials, minimizing scrap and maximizing material usage. This optimized resource utilization leads to cost savings and improved profitability.
Illustrative Chart: Efficiency Improvements Through Robotics
The following chart illustrates the potential improvements in efficiency metrics achieved through robotics integration in a hypothetical electronics assembly plant. The data is presented as a percentage change from pre-robotics implementation to post-robotics implementation.
Chart Description: A bar chart showing percentage change in KPIs. The x-axis represents the KPIs (Production Output, Defect Rate, Cycle Time, Resource Utilization). The y-axis represents the percentage change. Four bars are shown, one for each KPI. Production output shows a 30% increase, defect rate a 25% decrease, cycle time a 20% decrease, and resource utilization a 15% increase. The chart is titled “Impact of Robotics on Manufacturing Efficiency.” The bars are color-coded for easy visual comparison. Positive changes are shown in green, negative changes in red (for defect rate).
Robotics are revolutionizing manufacturing, boosting speed and precision. This efficiency surge is further amplified by seamless connectivity, which is precisely why understanding the role of The Future of 5G in Supporting IoT and Smart Devices is crucial. 5G’s speed and low latency are game-changers, allowing for real-time data exchange between robots and control systems, ultimately refining robotic manufacturing processes even more.
Robotics and Automation
The integration of robotics into manufacturing isn’t just about deploying robots; it’s about orchestrating a symphony of automation technologies working in harmony. This synergy, powered by advancements in artificial intelligence, machine learning, and the Internet of Things (IoT), is fundamentally reshaping manufacturing efficiency and productivity. However, this transformation isn’t without its hurdles. Understanding both the potential benefits and the inherent challenges is crucial for successful implementation.
The synergistic relationship between robotics and other automation technologies is undeniable. AI, for example, allows robots to adapt to dynamic environments and learn from experience, enhancing their flexibility and precision. Machine learning algorithms can optimize robot performance in real-time, predicting maintenance needs and adjusting processes for maximum efficiency. The IoT provides the connectivity backbone, enabling seamless data flow between robots, machines, and the overall manufacturing system, fostering greater transparency and control. Imagine a scenario where a robotic arm, equipped with sensors and connected to an IoT network, detects a quality defect. This data is instantly analyzed by AI, which adjusts the robotic arm’s parameters to prevent further defects, all while simultaneously notifying human operators. This level of interconnectedness and intelligence is simply unattainable with isolated robotic systems.
Initial Investment Costs and Integration Complexities
Implementing robotics in manufacturing requires significant upfront investment. The cost of purchasing, installing, and configuring robotic systems can be substantial, particularly for large-scale deployments. Moreover, integrating robots into existing manufacturing processes can be complex, demanding specialized expertise and potentially causing disruptions to production workflows. For instance, a small-to-medium sized enterprise (SME) might find the initial capital outlay for a collaborative robot (cobot) system, including the necessary software and training, to be a significant barrier. Furthermore, integrating this cobot into an existing assembly line might require adjustments to the line’s layout and the retraining of personnel to work alongside the robot.
Workforce Retraining Needs
The introduction of robotics can lead to concerns about job displacement, necessitating comprehensive workforce retraining initiatives. Workers need to acquire new skills to operate, maintain, and program robots, as well as to collaborate effectively with them in a shared workspace. Successful implementation requires a proactive approach to upskilling and reskilling the existing workforce, focusing on skills like programming, data analysis, and robotic maintenance. Consider a factory that automates its welding process with robotic arms. The welders previously employed might need retraining to become robotic maintenance technicians or to manage the robotic welding system, ensuring a smooth transition and minimizing job displacement anxieties.
Strategies for Overcoming Challenges
Addressing the challenges of robotics implementation requires a multi-pronged approach. Strategic planning is paramount, including a thorough assessment of current manufacturing processes, identification of areas suitable for automation, and careful selection of robotic systems based on specific needs and budget constraints. Phased implementation, starting with smaller-scale projects, can minimize risk and provide valuable learning experiences. Furthermore, partnerships with robotics integrators and technology providers can provide crucial expertise and support during the implementation process. Finally, investing in robust training programs for the workforce is essential to ensure a smooth transition and maximize the benefits of robotic automation. A well-structured training program might include on-site workshops, online courses, and mentorship opportunities, enabling workers to develop the necessary skills to thrive in a technologically advanced manufacturing environment.
The Future of Robotics in Manufacturing
The manufacturing landscape is poised for a dramatic transformation, driven by advancements in robotics and artificial intelligence. We’re moving beyond the era of simple, repetitive robotic tasks towards a future where robots are collaborative, adaptable, and deeply integrated into every aspect of the production process. This evolution promises unprecedented levels of efficiency, flexibility, and customization.
The next generation of manufacturing robots will be significantly more intelligent and autonomous than their predecessors. This intelligence will enable them to handle more complex tasks, adapt to changing conditions, and even learn from their experiences. This shift will not only increase productivity but also open up new possibilities for manufacturing processes and product design.
Collaborative Robots and Human-Robot Interaction, The Role of Robotics in Redefining Manufacturing Efficiency
The increasing sophistication of collaborative robots (cobots) will redefine the factory floor. Cobots, designed to work safely alongside humans, will handle tasks requiring dexterity and precision, freeing human workers to focus on more complex and creative aspects of production. Imagine a scenario where a human worker guides a cobot through a complex assembly process, teaching it the steps, and then the cobot independently repeats the task with high accuracy and speed. This synergistic relationship will optimize both human and robotic capabilities, leading to significant improvements in efficiency and quality.
Advanced Sensor Integration and AI-Powered Control Systems
Future robots will be equipped with advanced sensor technologies, including vision systems, force sensors, and proximity sensors, enabling them to perceive their environment with greater accuracy and precision. These sensors, combined with sophisticated AI-powered control systems, will allow robots to adapt to variations in materials, environmental conditions, and even unexpected events on the factory floor. For example, a robot equipped with advanced vision systems could identify defects in a product during assembly and automatically adjust its actions to correct the issue, minimizing waste and improving quality control.
Emerging Technologies Shaping the Future of Robotics in Manufacturing
The future of robotics in manufacturing will be significantly shaped by several key emerging technologies. These advancements will not only enhance existing robotic capabilities but also unlock entirely new possibilities.
- Artificial Intelligence (AI) and Machine Learning (ML): AI and ML algorithms will empower robots to learn from data, adapt to changing conditions, and make decisions autonomously. This will lead to more efficient and flexible manufacturing processes.
- Computer Vision: Advanced computer vision systems will allow robots to “see” and interpret their surroundings with greater accuracy, enabling them to perform more complex tasks and interact more effectively with their environment. This is crucial for tasks like quality inspection and parts recognition.
- Digital Twins and Simulation: Digital twins, virtual representations of physical systems, will be used to simulate and optimize robotic processes before deployment in real-world settings. This will reduce downtime, minimize errors, and accelerate the implementation of new robotic systems.
- 5G and Edge Computing: High-speed 5G networks and edge computing will enable faster data processing and communication between robots and other systems, leading to improved responsiveness and real-time control.
- Additive Manufacturing (3D Printing): The integration of 3D printing with robotics will allow for the creation of customized parts and tools on demand, reducing lead times and improving flexibility.
Case Studies: The Role Of Robotics In Redefining Manufacturing Efficiency
Real-world examples showcase the transformative power of robotics in manufacturing. These case studies highlight diverse approaches, challenges overcome, and the significant efficiency gains achieved through strategic robotic implementation. Analyzing these successes provides valuable insights for businesses considering similar transformations.
Fanuc’s Automated Machining Cell
Fanuc, a leading robotics company, has extensively implemented its own robots within its manufacturing processes. A prime example is their automated machining cell. The challenge was to increase the precision and speed of machining complex metal parts while minimizing human error and downtime. Fanuc addressed this by integrating a network of robots for various tasks, including material handling, machine loading and unloading, and quality inspection. These robots work collaboratively, seamlessly transferring parts between different machines with minimal human intervention. The result? A significant increase in throughput, reduced production time by approximately 30%, and a marked improvement in the consistency of part quality. The robots’ precision minimizes scrap, further boosting efficiency.
Amazon’s Kiva System (Now Amazon Robotics)
Amazon’s adoption of the Kiva system (now Amazon Robotics) revolutionized its warehouse operations. The challenge was to manage the rapidly growing volume of orders and optimize warehouse logistics to ensure timely delivery. The solution involved deploying hundreds of autonomous mobile robots (AMRs) to move shelves of products directly to human pickers. This eliminated the time-consuming task of workers walking long distances to retrieve items. The impact was dramatic. Order fulfillment speed increased significantly, reducing delivery times and improving customer satisfaction. The system also enhanced warehouse space utilization by optimizing storage and retrieval processes. The Kiva system demonstrates the potential of AMRs to reshape logistics and warehousing, significantly improving efficiency metrics like order fulfillment time and labor costs.
Tesla’s Gigafactory Automation
Tesla’s Gigafactories represent a bold vision of highly automated manufacturing. The challenge was to build a massive production facility for electric vehicles and batteries at an unprecedented scale and speed. Tesla’s solution involved extensive use of industrial robots for various tasks, from body assembly and painting to battery pack construction. This high level of automation reduced reliance on manual labor, enabling faster production rates and increased output. While Tesla’s approach has faced challenges related to the complexity of integrating such a large-scale robotic system, the resulting improvements in production volume and efficiency are undeniable. The Gigafactories demonstrate the potential of comprehensive automation to transform even the most complex manufacturing processes, although the initial investment and integration complexities are substantial.
Closing Summary
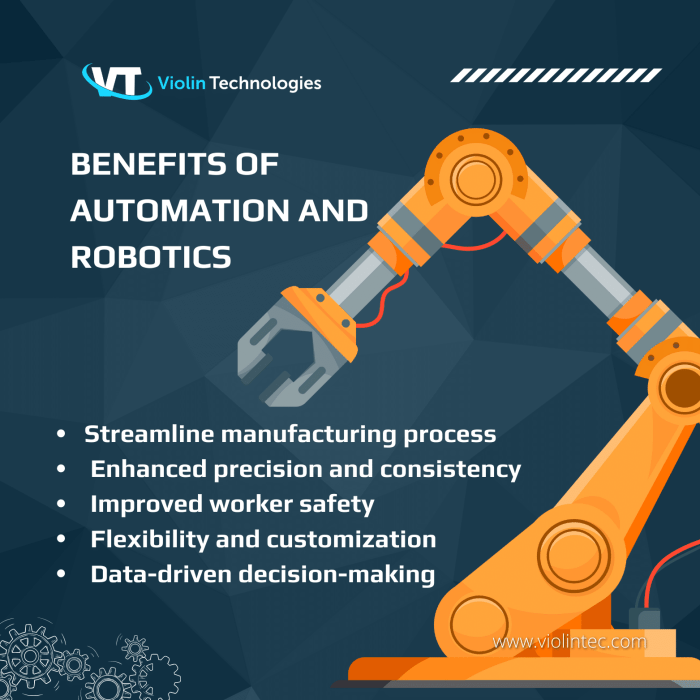
Source: violintec.com
The integration of robotics in manufacturing isn’t just about upgrading machinery; it’s about fundamentally reimagining the production process. From streamlining operations and boosting productivity to minimizing errors and maximizing resource utilization, the benefits are undeniable. While challenges exist, the potential rewards are immense, paving the way for a more efficient, adaptable, and ultimately, more sustainable manufacturing future. The journey towards fully automated, robotic-driven factories is ongoing, but the direction is clear: a future where efficiency and innovation go hand-in-hand.