How Machine Learning is Optimizing Supply Chain Logistics? Forget clunky spreadsheets and guesswork – the future of supply chain management is here, and it’s powered by AI. From predicting equipment failures to optimizing delivery routes and even anticipating market shifts, machine learning is revolutionizing how goods move around the globe. This isn’t just about efficiency; it’s about creating a more resilient, responsive, and profitable supply chain for everyone.
This deep dive explores how machine learning algorithms are tackling age-old supply chain challenges. We’ll uncover the magic behind predictive maintenance, the power of AI-driven inventory management, and the strategic advantages of smarter route optimization. Get ready to witness how data is transforming logistics, one algorithm at a time.
Introduction

Source: acropolium.com
Machine learning is seriously upgrading supply chain logistics, predicting demand and optimizing routes with crazy accuracy. This AI-powered efficiency isn’t just limited to shipping; it’s also transforming other sectors, like real estate, as seen in this insightful article on The Role of AI in Revolutionizing the Real Estate Market. Ultimately, the core principle – leveraging data for smarter decisions – benefits all industries, further streamlining supply chain management and boosting overall productivity.
Supply chain logistics is the backbone of modern commerce, encompassing the intricate network of planning, sourcing, production, inventory management, and delivery of goods and services. It’s a complex dance involving multiple stakeholders, from raw material suppliers to end consumers, and its smooth operation is crucial for profitability and customer satisfaction. However, this intricate network faces numerous challenges, including unpredictable demand fluctuations, geopolitical instability, natural disasters, and ever-increasing transportation costs. Optimizing this complex system requires sophisticated strategies and technologies.
Machine learning (ML), a subset of artificial intelligence, offers a powerful new approach to tackling these supply chain challenges. Unlike traditional methods that rely heavily on historical data and rule-based systems, ML algorithms can analyze massive datasets, identify complex patterns, and make predictions with greater accuracy. This allows for more proactive and adaptive strategies, leading to significant improvements in efficiency and profitability. ML’s ability to learn and adapt from new data makes it particularly well-suited for the dynamic and unpredictable nature of global supply chains.
Machine Learning’s Impact on Supply Chain Optimization
Integrating machine learning into supply chain management promises a range of benefits, including improved forecasting accuracy, optimized inventory levels, reduced transportation costs, and enhanced risk management. For instance, ML algorithms can analyze historical sales data, weather patterns, and economic indicators to predict future demand with far greater accuracy than traditional forecasting methods. This enables companies to optimize their inventory levels, reducing storage costs and minimizing the risk of stockouts or overstocking. Similarly, ML can optimize transportation routes, scheduling, and fleet management, leading to significant cost savings and improved delivery times. By identifying potential disruptions early on, ML can help companies mitigate risks and ensure business continuity.
Comparison of Traditional and ML-Driven Approaches
The table below illustrates the key differences between traditional methods and machine learning approaches in supply chain management.
Method | Cost | Time Efficiency | Accuracy |
---|---|---|---|
Traditional Forecasting (e.g., time series analysis) | Relatively low initial cost, but high operational costs due to manual adjustments and potential inaccuracies. | Can be time-consuming, especially for complex scenarios requiring manual data analysis and interpretation. | Moderate accuracy; prone to errors due to reliance on historical data and assumptions. |
Machine Learning (e.g., deep learning, regression models) | Higher initial investment in software, hardware, and expertise, but lower long-term operational costs due to automation and improved accuracy. | Significantly improves time efficiency through automation and real-time analysis, allowing for quicker decision-making. | High accuracy due to the ability to identify complex patterns and adapt to changing conditions. Predictive capabilities lead to proactive adjustments. |
Predictive Maintenance using Machine Learning
Imagine a world where warehouse breakdowns and transportation delays are predicted, not just reacted to. That’s the power of predictive maintenance fueled by machine learning, revolutionizing supply chain logistics and saving businesses significant costs. By analyzing data from various sources, machine learning algorithms can anticipate equipment failures before they occur, allowing for proactive maintenance and preventing costly downtime.
Predictive models leverage historical maintenance data, sensor readings, and operational parameters to identify patterns and anomalies indicative of impending failures. This proactive approach minimizes disruptions, optimizes resource allocation, and ultimately strengthens the entire supply chain’s resilience.
Sensor Data Integration and Predictive Modeling, How Machine Learning is Optimizing Supply Chain Logistics
The foundation of predictive maintenance lies in the seamless integration of sensor data from various equipment within warehouses and transportation fleets. Sensors embedded in machinery, vehicles, and infrastructure collect real-time data on temperature, vibration, pressure, and other crucial parameters. This data is then fed into machine learning algorithms, specifically those suited for time-series analysis like Recurrent Neural Networks (RNNs) or Long Short-Term Memory networks (LSTMs), which are adept at identifying patterns over time. These algorithms learn from historical data to create predictive models that forecast the likelihood of equipment failure within a specific timeframe. The models consider factors such as operating conditions, usage patterns, and environmental influences to provide accurate and timely predictions. This allows for scheduled maintenance to be performed before a failure occurs, minimizing disruption and maximizing operational efficiency.
Cost Savings through Predictive Maintenance
Let’s consider a hypothetical scenario: a large e-commerce company utilizes predictive maintenance in its warehouse. Historically, unexpected forklift breakdowns resulted in an average of 5 hours of downtime per incident, costing approximately $5,000 per breakdown (including repair costs, lost productivity, and potential order delays). With predictive maintenance, the company implemented sensor monitoring and machine learning algorithms. The system accurately predicted 80% of forklift breakdowns one week in advance. This allowed for scheduled maintenance, reducing downtime by 80%, saving approximately $4,000 per incident. Over a year, with an average of 10 forklift breakdowns, the company achieved cost savings of $40,000. Furthermore, the proactive approach prevented potential damage to goods, minimized safety risks, and improved overall operational efficiency. This example showcases how the integration of machine learning into predictive maintenance can significantly reduce operational costs and enhance the reliability of supply chain operations. The savings extend beyond just financial aspects, encompassing improved safety, enhanced operational efficiency, and increased customer satisfaction due to consistent on-time deliveries.
Optimizing Inventory Management with Machine Learning
Inventory management is the backbone of any efficient supply chain. Getting it right means balancing the cost of holding too much stock against the risk of running out and losing sales. Machine learning offers a powerful toolkit to fine-tune this delicate balance, leading to significant cost savings and improved customer satisfaction. By leveraging data-driven insights, businesses can move from reactive inventory strategies to proactive, optimized systems.
Machine learning significantly enhances demand forecasting accuracy by analyzing historical sales data, incorporating external factors like seasonality, economic trends, and even social media sentiment. This allows for more precise predictions of future demand, leading to better inventory planning and reduced waste. Furthermore, machine learning algorithms can identify hidden patterns and relationships in data that might be missed by traditional forecasting methods, resulting in more accurate and reliable predictions. This accuracy translates directly into cost savings and improved operational efficiency.
Improved Demand Forecasting with Machine Learning
Machine learning algorithms excel at analyzing complex datasets to predict future demand with greater accuracy than traditional methods. By considering a wider range of variables, including external economic indicators and even social media trends, these algorithms can identify subtle patterns and seasonal fluctuations that would otherwise be missed. This leads to more precise forecasts, enabling businesses to optimize their inventory levels and avoid both overstocking and stockouts. For example, a retailer using machine learning might predict a surge in demand for a specific product based on an upcoming holiday or a trending social media campaign, allowing them to proactively adjust their inventory levels accordingly.
Inventory Optimization and Cost Reduction
The application of machine learning in inventory optimization extends beyond just forecasting. Machine learning models can analyze various factors, such as lead times, storage costs, and product perishability, to determine optimal stock levels for each item. This dynamic approach minimizes storage costs by preventing overstocking while simultaneously mitigating the risk of stockouts. For instance, a company might use machine learning to optimize its warehouse layout, minimizing the distance traveled by picking staff and reducing labor costs. Similarly, machine learning can predict potential stockouts and trigger automated replenishment orders, ensuring continuous supply and preventing disruptions to the supply chain.
Machine Learning Models for Inventory Management
Several machine learning models are effectively employed for inventory management. The choice of model depends on the specific needs and data available.
- Time Series Analysis: These models, such as ARIMA (Autoregressive Integrated Moving Average) and Prophet, are particularly well-suited for forecasting demand based on historical sales data. They capture temporal dependencies and seasonal patterns to predict future demand. For example, a grocery store might use an ARIMA model to predict weekly demand for milk, considering past sales and seasonal variations.
- Regression Models: Models like linear regression and support vector regression can incorporate various factors beyond historical sales data, such as price changes, promotions, and economic indicators, to create more comprehensive demand forecasts. A clothing retailer might use a regression model to predict demand for a new clothing line, considering factors like marketing spend and competitor pricing.
- Deep Learning Models: Recurrent Neural Networks (RNNs) and Long Short-Term Memory (LSTM) networks are capable of handling complex, long-term dependencies in time series data, making them suitable for forecasting demand in situations with significant seasonality or irregular patterns. An online retailer might use LSTMs to predict demand for electronics, considering factors such as product life cycles and technological advancements.
Enhancing Transportation and Route Optimization
The heart of any efficient supply chain beats with the rhythm of optimized transportation. Getting goods from point A to point B quickly, cost-effectively, and reliably is paramount. Machine learning is revolutionizing this process, offering sophisticated solutions that far surpass traditional methods. By analyzing vast datasets and identifying patterns invisible to the human eye, ML algorithms are transforming how companies plan, execute, and monitor their transportation networks.
Machine learning algorithms are transforming route optimization by dynamically considering multiple variables in real-time. This contrasts sharply with static route planning, which often fails to adapt to unexpected events such as traffic congestion or road closures. The ability to adapt to these real-world complexities leads to significant gains in efficiency and cost savings.
Real-time Route Optimization with Machine Learning
ML algorithms, particularly those based on reinforcement learning, can create optimal routes by processing data from various sources. This includes real-time traffic data from GPS devices, historical traffic patterns, weather forecasts, and even delivery time windows. The algorithm learns to predict the fastest and most efficient routes by analyzing past delivery data and continuously adjusting its strategy based on new information. For example, a delivery company using a machine learning-based route optimization system might dynamically reroute a truck to avoid a sudden traffic jam, ensuring on-time delivery despite the unexpected event. This dynamic adjustment is impossible with traditional static route planning. Imagine a scenario where a major accident blocks a highway. A traditional system would stick to the pre-planned route, resulting in significant delays. A machine learning system, however, would instantly reroute the delivery truck, minimizing delays and ensuring customer satisfaction.
Real-time Shipment Tracking and Monitoring
Real-time tracking and monitoring of shipments are crucial for maintaining transparency and accountability throughout the supply chain. Machine learning enhances this process by providing predictive capabilities. By analyzing data from GPS trackers, sensors, and other sources, ML algorithms can predict potential delays, identify areas of risk, and even detect anomalies that might indicate theft or damage. For instance, an unexpected stop outside the planned route could trigger an alert, prompting investigation and potentially preventing a loss. This proactive approach allows for faster responses to unforeseen circumstances and improved overall efficiency. A company using machine learning might predict a potential delay based on historical weather patterns and current forecasts, allowing them to proactively inform customers and adjust delivery schedules accordingly.
Comparison of Route Optimization Methods
The benefits of machine learning-based route optimization are undeniable. A comparison with traditional methods highlights the significant improvements achieved.
Method | Fuel Consumption | Delivery Time | Route Efficiency |
---|---|---|---|
Traditional (Static) Routing | Higher (due to longer routes and idling) | Longer (due to unforeseen delays and inflexible routes) | Lower (less efficient use of resources) |
Machine Learning-based Routing | Lower (due to shorter routes and reduced idling) | Shorter (due to real-time adjustments and proactive planning) | Higher (optimized resource utilization and improved delivery times) |
Improving Supply Chain Visibility and Risk Management

Source: isu.pub
Machine learning is revolutionizing supply chain management by providing unprecedented levels of visibility and enabling proactive risk mitigation. By analyzing vast amounts of data from various sources, ML algorithms can create a real-time, holistic view of the entire supply chain, from raw material sourcing to final product delivery. This enhanced visibility allows businesses to identify potential problems early on, minimizing disruptions and maximizing efficiency.
Real-time visibility across the supply chain is achieved through the integration of various data sources, including sensor data from transportation vehicles, warehouse management systems, and even social media sentiment analysis. Machine learning algorithms process this data to identify patterns, predict potential delays, and provide alerts for immediate action. This proactive approach minimizes the impact of unforeseen events and improves overall supply chain resilience.
Real-time Tracking and Monitoring
Machine learning algorithms process data from various sources, such as GPS trackers on shipments, warehouse inventory systems, and production line sensors, to provide a comprehensive, real-time view of the entire supply chain. This allows businesses to monitor the location and status of goods at every stage of the process, enabling immediate responses to potential delays or disruptions. For example, if a shipment is delayed due to unforeseen circumstances, the system can automatically alert relevant stakeholders and initiate contingency plans to minimize the impact on delivery timelines.
Risk Identification and Mitigation
Machine learning can identify potential risks and disruptions by analyzing historical data and current market trends. For example, by analyzing weather patterns, ML algorithms can predict potential delays caused by extreme weather events, allowing businesses to proactively reroute shipments or adjust production schedules. Similarly, analysis of geopolitical events, economic indicators, and even social media sentiment can help identify potential disruptions and allow for proactive mitigation strategies. This proactive approach significantly reduces the impact of unforeseen circumstances.
Predicting and Responding to Disruptions: A Hypothetical Scenario
Imagine a major manufacturer of electronics whose supply chain relies heavily on components sourced from a specific factory in a region prone to earthquakes. Using machine learning, the company has developed a predictive model that analyzes seismic activity data, historical weather patterns, and real-time news feeds. When the model detects an increased probability of a significant earthquake within a specific timeframe, it automatically triggers a series of actions. This might include: alerting relevant personnel, initiating the rerouting of shipments of critical components from alternative suppliers, and adjusting production schedules to minimize the impact of potential component shortages. The system might even automatically negotiate contracts with backup suppliers based on pre-defined parameters, ensuring business continuity despite the disruption. This proactive response, enabled by machine learning, minimizes production downtime and financial losses.
Case Studies
Real-world applications showcase the transformative power of machine learning in supply chain logistics. These examples highlight how businesses are leveraging data-driven insights to overcome persistent challenges and achieve significant improvements in efficiency, cost reduction, and customer satisfaction. Let’s delve into some compelling case studies that illustrate the practical impact of this technology.
Walmart’s Optimized Inventory Management
Walmart, a retail giant, faced the persistent challenge of managing vast inventories across thousands of stores while minimizing waste and maximizing availability. To tackle this, they implemented a machine learning model that predicted demand with remarkable accuracy. This model analyzed historical sales data, weather patterns, local events, and even social media trends to forecast demand for specific products in particular locations. The result? Significant reductions in stockouts and overstocking, leading to substantial cost savings and improved customer satisfaction. Walmart’s system utilizes a combination of time series analysis, regression models, and deep learning techniques to achieve its predictive power.
- Improved forecast accuracy leading to reduced waste and increased sales.
- Optimized inventory levels across its vast network of stores.
- Enhanced customer satisfaction through improved product availability.
DHL’s Route Optimization and Delivery Efficiency
DHL, a global logistics leader, employed machine learning to optimize its delivery routes and improve overall efficiency. Their system analyzes real-time traffic data, weather conditions, and delivery schedules to dynamically adjust routes, minimizing delivery times and fuel consumption. This sophisticated system utilizes algorithms based on graph theory and reinforcement learning to find the optimal path for each delivery, considering various constraints and dynamic conditions. The implementation has resulted in substantial cost savings and improved on-time delivery rates.
- Reduced delivery times and improved on-time delivery rates.
- Significant fuel cost savings due to optimized routes.
- Enhanced overall delivery efficiency and operational effectiveness.
Amazon’s Predictive Maintenance for Warehouses
Amazon, known for its extensive warehouse network, utilizes machine learning for predictive maintenance of its automated systems. By analyzing sensor data from various warehouse equipment, their system identifies potential failures before they occur, allowing for proactive maintenance and minimizing downtime. This approach utilizes anomaly detection techniques and predictive modeling to anticipate equipment malfunctions. The results have been impressive, leading to a significant reduction in equipment failures and improved operational uptime within their fulfillment centers.
- Reduced equipment downtime and improved operational efficiency.
- Minimized unexpected maintenance costs and disruptions.
- Improved the overall lifespan and reliability of warehouse equipment.
The Future of Machine Learning in Supply Chain Logistics
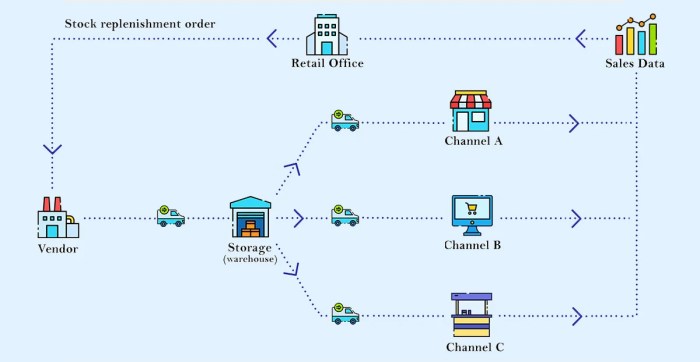
Source: retalon.com
Machine learning’s impact on supply chain logistics is only just beginning. As the technology matures and data availability increases, we can expect even more profound transformations in the coming years. The integration of advanced algorithms and innovative technologies will redefine efficiency, resilience, and profitability across the entire supply chain ecosystem.
The next decade will witness a surge in the sophistication and application of machine learning within the logistics sector. This evolution will be driven by both advancements in the underlying technology and the increasing availability of data, allowing for more accurate and insightful predictions and optimizations.
Emerging Trends and Technologies
Several emerging trends and technologies promise to significantly enhance the capabilities of machine learning in supply chain optimization. These advancements will move beyond current applications, offering more proactive and intelligent solutions. For instance, the rise of generative AI is poised to revolutionize aspects such as demand forecasting and route planning, generating multiple scenarios and solutions to complex problems far faster than humans. Furthermore, advancements in edge computing will enable real-time analysis of data at the point of collection, minimizing latency and improving responsiveness to dynamic changes within the supply chain. The increased use of digital twins, virtual representations of physical assets and processes, will facilitate predictive maintenance and allow for simulations to test different scenarios and optimize operations before implementation. Finally, the integration of blockchain technology offers the potential for increased transparency and security, enabling greater trust and efficiency in tracking goods and managing transactions throughout the supply chain.
Challenges and Limitations of Widespread Adoption
Despite the immense potential, the widespread adoption of machine learning in supply chain management faces several challenges. One major hurdle is the need for high-quality, clean data. Machine learning algorithms rely heavily on accurate and comprehensive data; incomplete or inaccurate data can lead to flawed predictions and suboptimal decisions. Furthermore, integrating machine learning systems into existing infrastructure can be complex and expensive, requiring significant investment in both technology and expertise. Data security and privacy concerns are also paramount, especially with the increasing reliance on sensitive data regarding customer orders, inventory levels, and transportation routes. Finally, the lack of skilled professionals capable of developing, implementing, and maintaining machine learning systems poses a significant barrier to widespread adoption. Many companies lack the internal expertise to effectively leverage these advanced technologies.
Vision for the Future of Machine Learning in Supply Chain Logistics
In the next 5-10 years, machine learning will likely transform supply chain logistics into a highly automated, predictive, and resilient system. We can expect near real-time visibility into every stage of the supply chain, enabling proactive risk management and immediate responses to disruptions. AI-powered systems will optimize inventory levels with remarkable accuracy, minimizing waste and maximizing efficiency. Autonomous vehicles and drones will revolutionize transportation and delivery, reducing costs and improving delivery times. Predictive maintenance will become the norm, minimizing downtime and extending the lifespan of equipment. The overall result will be a more agile, efficient, and sustainable supply chain, capable of adapting to unforeseen events and delivering goods to consumers faster and more reliably than ever before. For example, imagine a future where a self-driving truck, equipped with sensors and AI, can autonomously navigate complex routes, avoiding traffic and optimizing fuel consumption. This scenario, once a futuristic fantasy, is rapidly becoming a reality thanks to the rapid advancements in machine learning and related technologies.
Outcome Summary: How Machine Learning Is Optimizing Supply Chain Logistics
The integration of machine learning into supply chain logistics isn’t just a trend; it’s a necessity. As data continues to explode and algorithms become more sophisticated, the potential for optimization is limitless. Companies that embrace this technology will gain a significant competitive edge, achieving greater efficiency, reduced costs, and unparalleled agility in a rapidly evolving global marketplace. The future of supply chain is intelligent, predictive, and undeniably powered by the insights of machine learning.