How Robotics is Assisting in the Manufacturing of Consumer Goods? It’s not just sci-fi anymore; it’s the present and future of production. From tiny circuit boards to your morning coffee, robots are quietly revolutionizing how consumer goods are made, boosting efficiency, and upping the quality game. This deep dive explores the different types of robots making waves in factories worldwide, examining their impact on speed, cost, and the overall manufacturing process. We’ll also peek into the future of this fascinating intersection of technology and consumerism.
Get ready to uncover how collaborative robots (cobots) are teaming up with humans, how Automated Guided Vehicles (AGVs) are mastering material handling, and how AI is shaping the next generation of smart factories. We’ll cover everything from the challenges of integrating robotics into existing systems to the incredible potential of fully automated production lines. Buckle up, it’s going to be a ride!
Types of Robots in Consumer Goods Manufacturing
The rise of automation in consumer goods manufacturing is nothing short of revolutionary. From the intricate assembly of smartphones to the precise packaging of cosmetics, robots are transforming how products are made, increasing efficiency, and improving quality. This isn’t just about replacing human workers; it’s about creating a more synergistic partnership between humans and machines, leading to smarter, faster, and more adaptable production lines. Let’s delve into the diverse robotic workforce driving this change.
Industrial Robots in Consumer Electronics Assembly
Industrial robots are the workhorses of many consumer goods factories, particularly in electronics manufacturing. Their precision and speed are unmatched in high-volume production environments. They handle repetitive tasks with unwavering consistency, leading to fewer errors and higher output. Below is a table illustrating some key examples:
Robot Type | Application | Manufacturer (Example) | Advantages |
---|---|---|---|
Articulated Robot (6-axis) | Soldering, component placement, testing | FANUC | High dexterity, reach, and payload capacity, suitable for complex assembly tasks. |
SCARA Robot | Pick and place operations, assembly of small components | Yaskawa Motoman | Fast and precise movements in a horizontal plane, ideal for repetitive tasks. |
Delta Robot | High-speed picking and packing, particularly for small items | ABB | Exceptional speed and accuracy, perfect for applications requiring quick cycle times. |
Cartesian Robot | Material handling, dispensing, and precise movements along linear axes | KUKA | Simple design, high accuracy, and suitable for applications requiring large workspaces. |
Collaborative Robots (Cobots) in Consumer Goods Production
Collaborative robots, or cobots, are designed to work safely alongside human workers. Unlike traditional industrial robots, which are typically caged off for safety reasons, cobots utilize advanced sensors and safety features to allow for direct human-robot interaction. This collaborative approach enhances flexibility and efficiency in the manufacturing process.
Cobots in consumer goods production perform a variety of tasks, including:
* Assisted Assembly: Guiding workers through complex assembly steps, providing support and reducing strain. For example, a cobot might hold a component in place while a human worker attaches it.
* Quality Control: Inspecting products for defects, identifying inconsistencies, and ensuring quality standards are met. This can involve visual inspection or measurements using integrated sensors.
* Machine Tending: Loading and unloading machines, such as injection molding machines or CNC machines. This frees up human workers to focus on more complex tasks.
* Packaging and Palletizing: Assisting with the packaging and palletizing of finished products, ensuring efficient and consistent handling.
Automated Guided Vehicles (AGVs) in Material Handling
Automated Guided Vehicles (AGVs) play a crucial role in optimizing material flow within consumer goods factories. These autonomous vehicles navigate the factory floor, transporting materials and finished goods between different workstations. Their implementation significantly reduces manual handling, improves efficiency, and minimizes the risk of errors.
AGVs contribute to enhanced material handling through various applications, including:
- Transporting raw materials from storage to assembly lines.
- Moving work-in-progress between different manufacturing stages.
- Delivering finished goods to packaging and shipping areas.
- Efficiently managing inventory within the factory.
- Reducing congestion and improving overall workflow.
Impact on Production Efficiency and Speed
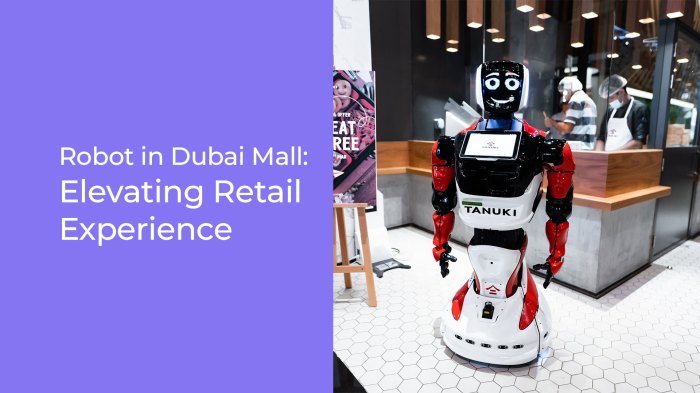
Source: provenrobotics.ai
The integration of robotics into consumer goods manufacturing has revolutionized production lines, dramatically increasing efficiency and speed. This shift from manual labor to automated systems has significantly impacted various aspects of the manufacturing process, resulting in higher output, lower costs, and improved product quality. Let’s delve into the specifics.
Robotic assembly lines boast significantly faster production speeds compared to their manual counterparts. Consider smartphone manufacturing, for example. A single robotic arm can perform multiple tasks – from precise component placement to intricate soldering – with incredible speed and consistency. A manual assembly line, on the other hand, relies on human workers performing these tasks individually, leading to bottlenecks and slower overall production. A robotic line can assemble several smartphones per minute, while a manual line might manage only a fraction of that. This difference in speed translates directly to increased output and shorter lead times for getting products to market.
Reduced Human Error and Improved Product Quality
Human error is an inevitable aspect of manual manufacturing processes. Robotic automation minimizes this risk, resulting in a considerable improvement in product quality. The precision and repeatability of robotic systems virtually eliminate many common manufacturing errors.
- Improper component placement: Robots ensure precise placement of components, avoiding misalignments or incorrect installations.
- Soldering defects: Robotic soldering systems offer consistent heat application and precise placement, minimizing defects like cold solder joints or bridging.
- Assembly inconsistencies: Robots maintain consistent assembly processes, reducing variations in product quality across units.
- Damage during handling: Robots handle components with care, reducing the risk of physical damage during the manufacturing process.
Production Output and Manufacturing Costs
The impact of robotics on production output is substantial. Increased speed and reduced errors translate to a significant rise in the number of units produced within a given timeframe. However, the initial investment in robotic systems is considerable. While the long-term cost savings can be significant, the upfront capital expenditure is a key factor to consider.
Factor | Robotic Assembly Line | Manual Assembly Line |
---|---|---|
Initial Investment | High (including robot purchase, integration, and programming) | Low (primarily labor costs) |
Production Speed | Very High (e.g., multiple smartphones per minute) | Low (e.g., significantly fewer smartphones per minute) |
Defect Rate | Very Low (near zero in many cases) | Relatively High (variable depending on worker skill and fatigue) |
Labor Costs | Low (reduced workforce) | High (significant workforce required) |
Maintenance Costs | Moderate (regular maintenance and occasional repairs) | Low (minimal maintenance) |
Long-Term Cost | Potentially Lower (due to increased output and reduced defects) | Potentially Higher (due to higher defect rates and labor costs) |
Robotics in Different Consumer Goods Sectors: How Robotics Is Assisting In The Manufacturing Of Consumer Goods
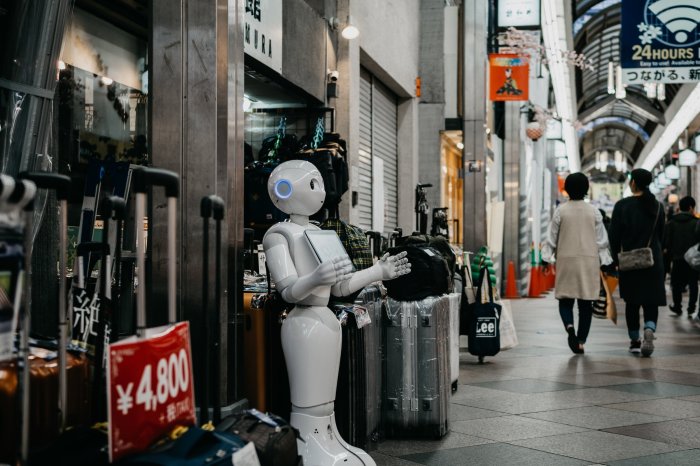
Source: squarespace-cdn.com
Robots are revolutionizing consumer goods manufacturing, boosting efficiency and precision. This automation trend extends beyond the factory floor; the same principles are driving advancements in other sectors, like the automotive industry where How 5G Will Enable Breakthroughs in Autonomous Vehicles is crucial for self-driving car development. Ultimately, the interconnectedness of these technological leaps – from robotic assembly lines to autonomous vehicles – points to a future of hyper-efficient production and delivery systems.
The rise of robotics isn’t just a sci-fi fantasy; it’s revolutionizing how we produce the everyday goods we consume. From the food on our plates to the clothes on our backs, robots are streamlining processes, boosting efficiency, and improving product quality across various sectors. Let’s dive into some specific examples.
Robotic Applications in the Food and Beverage Industry
The food and beverage industry, known for its demanding production lines and hygiene standards, is a prime beneficiary of robotic automation. Robots handle tasks ranging from picking and packing delicate produce to precise dispensing of ingredients and maintaining sterile environments. Imagine a robotic arm delicately placing strawberries into punnets, ensuring no bruising, or a fleet of automated guided vehicles (AGVs) swiftly transporting pallets of bottled drinks through a warehouse. These are not futuristic concepts; they’re everyday realities in many modern food production facilities. For instance, robotic palletizers are widely used to stack and unstack cases of beverages with incredible speed and accuracy, reducing labor costs and improving efficiency. Similarly, robotic arms are used in automated packaging lines for a wide variety of food products, ensuring consistent packaging speed and quality. Furthermore, in breweries, robots can handle the delicate task of cleaning and sanitizing equipment, maintaining the highest hygiene standards.
Robots in Apparel and Textile Manufacturing
The apparel and textile industry, traditionally associated with labor-intensive processes, is undergoing a significant transformation thanks to robotics. While fully automated clothing production remains a challenge due to the complex nature of fabric manipulation, robots are increasingly taking on specific tasks. These include cutting fabric with laser precision, sewing seams with consistent speed and accuracy, and handling the intricate process of quality control. For example, robotic arms equipped with advanced vision systems can inspect garments for defects, identifying flaws that might be missed by human eyes. Furthermore, robots are utilized in the automated dyeing and finishing processes, enhancing consistency and efficiency. Consider the repetitive task of sewing buttons – a robot can perform this consistently and tirelessly, eliminating human error and improving productivity. The adoption of collaborative robots (cobots), which work safely alongside human workers, is also gaining traction, allowing for a more flexible and efficient production line.
Hypothetical Robotic System for Automotive Part Manufacturing
Let’s envision a robotic system designed to automate the assembly of a crucial automotive component: the engine block. This system would incorporate a combination of industrial robots and cobots. Large industrial robots would handle the heavy lifting, precisely positioning engine block castings onto the assembly line. These robots would be equipped with advanced sensors to ensure accurate placement and orientation. Meanwhile, smaller, more agile cobots would perform the more delicate tasks, such as installing smaller components like sensors and gaskets. The cobots would work alongside human technicians, offering assistance with intricate tasks and ensuring a seamless workflow. The entire system would be monitored by a central control system, optimizing the assembly process and tracking production metrics in real-time. This system could significantly reduce assembly time, improve accuracy, and minimize the risk of human error, ultimately leading to higher quality and more efficient production of engine blocks. This is not just a hypothetical scenario; similar systems, albeit with variations depending on the specific component, are already being implemented in various automotive plants worldwide.
Challenges and Future Trends

Source: kudan.io
Integrating robotics into manufacturing isn’t a simple plug-and-play operation; it’s a complex undertaking that requires careful planning and significant investment. Successfully navigating the transition requires understanding the potential hurdles and envisioning the future landscape of automated production. This section delves into the challenges manufacturers face and explores the exciting trends shaping the future of robotics in consumer goods manufacturing.
The successful implementation of robotics in consumer goods manufacturing hinges on overcoming several key challenges. These obstacles, if not addressed proactively, can significantly hinder the adoption and effectiveness of robotic systems.
Challenges in Robotics Integration
Several factors can complicate the integration of robotics into existing manufacturing facilities. These challenges often involve significant upfront costs, necessitate workforce retraining, and demand careful consideration of safety protocols.
- High Initial Investment Costs: Purchasing, installing, and maintaining robotic systems requires a substantial upfront investment. This can be a significant barrier for smaller manufacturers with limited budgets.
- Integration Complexity: Integrating robots into existing production lines often requires significant modifications to the factory layout and existing equipment. This process can be complex, time-consuming, and disruptive to ongoing operations.
- Workforce Retraining Needs: The introduction of robots necessitates retraining existing employees to work alongside and maintain these new technologies. This requires investment in training programs and can lead to temporary disruptions in productivity.
- Safety Concerns: Ensuring the safety of human workers alongside robots is paramount. Implementing robust safety protocols and safeguards is crucial to prevent accidents and maintain a safe working environment.
- Data Security and Privacy: The increasing reliance on data-driven robotics raises concerns about data security and the privacy of sensitive information. Robust cybersecurity measures are essential to protect against data breaches and unauthorized access.
Future Trends in Robotics for Consumer Goods Manufacturing, How Robotics is Assisting in the Manufacturing of Consumer Goods
The future of robotics in consumer goods manufacturing is bright, driven by advancements in artificial intelligence (AI) and machine learning (ML). These technologies are poised to revolutionize production processes, leading to greater efficiency, flexibility, and customization.
- AI-Powered Robotics: AI enables robots to adapt to changing conditions, learn from experience, and make decisions autonomously. This leads to improved efficiency and reduced reliance on human intervention.
- Increased Collaboration Between Robots and Humans: Future manufacturing facilities will likely see more collaborative robots (cobots) working alongside human workers, enhancing productivity and safety.
- Advanced Machine Learning for Predictive Maintenance: ML algorithms can analyze data from robotic systems to predict potential failures and schedule maintenance proactively, minimizing downtime and maximizing efficiency.
- Enhanced Customization and Personalization: Robotics, coupled with AI, will enable manufacturers to produce highly customized products tailored to individual consumer preferences at scale.
- Robotics-Driven Supply Chain Optimization: AI-powered robots can optimize logistics and supply chain management, improving efficiency and reducing costs throughout the entire production process.
A Futuristic Consumer Goods Manufacturing Facility
Imagine a sprawling, brightly lit factory humming with activity, yet devoid of human workers on the production floor. Sleek, autonomous robots glide effortlessly through the facility, assembling intricate components with precision and speed. AI-powered systems monitor every aspect of the production process, optimizing efficiency and predicting potential issues before they arise. Customized products are created on demand, tailored to individual consumer preferences. Data flows seamlessly through the system, providing real-time insights into production performance and supply chain logistics. This is not science fiction; it’s a glimpse into the future of consumer goods manufacturing powered by advanced robotics.
Safety and Human-Robot Collaboration
Integrating robots into consumer goods manufacturing demands a meticulous approach to safety, ensuring both worker well-being and operational efficiency. The successful implementation hinges on robust safety protocols and a thoughtful consideration of human-robot collaboration (HRC). This section delves into the crucial safety measures and explores the advantages and challenges inherent in HRC within this dynamic environment.
Safety Protocols and Measures for Robot Integration
Implementing robots in consumer goods manufacturing necessitates a multi-layered safety strategy. This begins with careful risk assessment, identifying potential hazards specific to the robots and their interactions with the workspace. This assessment should encompass the robot’s capabilities, the tasks it performs, and the proximity of human workers. Subsequently, appropriate safety measures are implemented, such as installing physical barriers (light curtains, safety fences), implementing emergency stop mechanisms readily accessible to operators, and employing speed and power limiting systems on the robots themselves. Regular maintenance and thorough operator training are also non-negotiable components of a comprehensive safety plan. Furthermore, adhering to industry standards and relevant safety regulations is crucial to minimizing risk and ensuring compliance. For example, ISO 10218-1 and ISO 10218-2 provide detailed guidelines for industrial robot safety.
Human-Robot Collaboration (HRC): Advantages and Disadvantages
Human-robot collaboration (HRC) presents a compelling approach to manufacturing, combining the precision and speed of robots with the adaptability and problem-solving skills of human workers. However, it’s not without its challenges.
Advantages | Disadvantages |
---|---|
Increased productivity through task sharing: Robots handle repetitive or dangerous tasks, freeing human workers for more complex operations. | Initial investment costs: Implementing HRC requires significant upfront investment in robots, safety systems, and training. |
Improved product quality through enhanced precision and consistency: Robots maintain a high level of accuracy, reducing errors. | Integration complexities: Integrating robots into existing workflows can be challenging and require significant modifications to the production line. |
Enhanced workplace safety by automating hazardous tasks: Robots can handle tasks that pose risks to human workers, such as working with heavy machinery or hazardous materials. | Job displacement concerns: Automation can lead to job displacement if not carefully managed, requiring retraining and upskilling initiatives. |
Greater flexibility and adaptability: HRC systems can be reconfigured and reprogrammed relatively easily to adapt to changing production needs. | Safety risks if protocols are not followed: Improperly implemented or maintained HRC systems can pose significant safety risks to human workers. |
Potential Hazards Associated with Improper Robot Integration and Operation
Improper integration and operation of robots in consumer goods manufacturing can lead to several serious hazards. These include:
- Collisions and injuries: Lack of adequate safety measures can result in collisions between robots and human workers, leading to serious injuries or fatalities.
- Malfunctioning equipment: Failure to conduct regular maintenance and inspections can lead to malfunctioning robots, causing unexpected movements or malfunctions, posing a risk to workers.
- Entrapment hazards: Workers can become entrapped in moving parts of the robot or its associated equipment if safety mechanisms are inadequate.
- Electrical hazards: Exposure to high-voltage equipment can lead to electrical shocks or burns if proper safety precautions are not taken.
- Ergonomic issues: Poorly designed HRC systems can lead to ergonomic issues for human workers, causing musculoskeletal disorders.
Ultimate Conclusion
The integration of robotics into consumer goods manufacturing is no longer a futuristic fantasy; it’s a rapidly evolving reality reshaping industries globally. From increased efficiency and reduced errors to the exciting possibilities of human-robot collaboration, the impact is undeniable. While challenges remain in implementation and safety, the future points towards increasingly sophisticated robotic systems, driven by AI and machine learning, creating a new era of manufacturing – one where speed, precision, and innovation converge to deliver higher-quality products at greater speed and lower costs. The question isn’t *if* robots will dominate manufacturing, but *how* we’ll best harness their potential to shape a more efficient and sustainable future.