The Role of Robotics in Revolutionizing Construction and Engineering is no longer a futuristic fantasy; it’s the present, rapidly reshaping how we build our world. From tiny drones surveying construction sites to massive robotic arms laying bricks with laser precision, automation is changing the game. Forget slow, expensive, and sometimes dangerous traditional methods – the future of building is here, and it’s robotic.
This isn’t just about speed and efficiency (though those are huge benefits!). It’s about tackling complex projects with previously unimaginable accuracy, boosting safety standards, and even opening up opportunities for innovative designs. We’ll explore the different types of robots making waves, their impact on the industry, and the exciting (and sometimes daunting) challenges ahead.
Introduction to Robotics in Construction and Engineering: The Role Of Robotics In Revolutionizing Construction And Engineering
The construction and engineering industries, traditionally reliant on manual labor and time-tested methods, are undergoing a significant transformation driven by the integration of robotics. While still in its relatively early stages, the adoption of robotics promises to revolutionize efficiency, safety, and precision across various construction and engineering tasks. This shift is fueled by advancements in artificial intelligence, sensor technology, and robotic manipulation capabilities, making previously impossible feats now within reach.
Current State of Robotics Adoption
Currently, the adoption of robotics in construction and engineering varies considerably depending on the specific application and geographic location. While fully automated construction sites are still a futuristic vision, the use of robots for specific tasks is steadily increasing. Companies are increasingly experimenting with robotic solutions for tasks such as bricklaying, welding, demolition, and 3D printing of building components. However, widespread adoption is hindered by factors such as high initial investment costs, the need for skilled technicians for operation and maintenance, and the inherent complexity of integrating robots into existing workflows. Nevertheless, the trend is undeniably towards greater integration.
Historical Evolution of Robotics in Construction and Engineering
The use of automation in construction and engineering isn’t entirely new. Early examples date back to the mid-20th century, with the introduction of automated machinery like excavators and cranes. However, these were primarily focused on enhancing the power and scale of human-operated equipment. The true emergence of robotics began in the late 20th and early 21st centuries, driven by advancements in computer processing power, sensor technology, and control systems. Early robotic applications focused on repetitive tasks like welding and painting in factory settings related to construction, but the field has since expanded dramatically.
Examples of Early Robotic Applications
Some of the earliest notable robotic applications in construction and engineering included automated welding systems used in the fabrication of steel structures. These robots increased both speed and consistency compared to manual welding, reducing human error and improving overall quality. Another early example involved the use of robotic arms for spray painting large structures, again improving efficiency and worker safety by minimizing exposure to hazardous materials. These early applications laid the groundwork for the more sophisticated robotic systems we see today.
Comparison of Traditional and Robotic-Assisted Construction Methods
The following table provides a comparison between traditional construction methods and those incorporating robotics:
Method | Speed | Cost | Safety | Precision |
---|---|---|---|---|
Traditional | Relatively slow | Can vary greatly, often high labor costs | Higher risk of accidents and injuries | Variable, subject to human error |
Robotic-Assisted | Significantly faster for specific tasks | High initial investment, but potential for long-term cost savings | Reduced risk of accidents in hazardous tasks | High precision and consistency |
Types of Robots Used in Construction and Engineering
The construction and engineering industries are undergoing a significant transformation, driven by the increasing adoption of robotics. These robots are not just futuristic fantasies; they’re actively improving efficiency, safety, and precision on construction sites and in engineering projects worldwide. From autonomous excavators to collaborative robots assisting human workers, the variety and capabilities are constantly expanding.
Categorization of Construction and Engineering Robots
Robots used in construction and engineering can be broadly categorized based on their functionality and application. This includes autonomous robots, remotely operated robots, and collaborative robots (cobots). Each type offers unique advantages and disadvantages, making them suitable for different tasks and environments. Understanding these differences is crucial for effective implementation in projects.
Autonomous Robots in Construction and Engineering
Autonomous robots operate independently, relying on sensors and sophisticated software for navigation and task execution. These robots often use technologies like GPS, LiDAR, and computer vision to perceive their surroundings and make decisions without human intervention. A prime example is autonomous bulldozers, capable of grading land with remarkable accuracy and efficiency. However, their reliance on advanced technology can make them expensive and susceptible to malfunctions in complex or unpredictable environments. Their strengths lie in their consistent performance and ability to handle repetitive tasks tirelessly, while their limitations include the need for robust infrastructure and sophisticated programming to function effectively.
Remotely Operated Robots in Construction and Engineering
Remotely operated robots, also known as teleoperated robots, are controlled by a human operator from a safe distance. This allows for complex tasks to be performed in hazardous environments, such as demolition or work in confined spaces. These robots can be equipped with various tools, such as cutting torches, demolition hammers, or grippers, depending on the specific application. While remotely operated robots offer flexibility and precision, they require a skilled operator and reliable communication links. Their strengths include the ability to perform intricate tasks in dangerous settings, while limitations include reliance on human operators and potential communication delays.
Collaborative Robots (Cobots) in Construction and Engineering
Collaborative robots, or cobots, are designed to work alongside human workers, sharing tasks and enhancing productivity. They are typically smaller and lighter than autonomous or remotely operated robots, making them easier to integrate into existing workflows. Cobots are often used for tasks like bricklaying, welding, or material handling. Their strength lies in their ability to improve safety by taking on physically demanding or repetitive tasks, and to augment human capabilities. Limitations include their relatively lower payload capacity compared to larger robots and the need for careful safety protocols to prevent accidents.
Comparison of Autonomous and Remotely Operated Robots
Autonomous robots excel in repetitive, predictable tasks, requiring minimal human intervention, while remotely operated robots are ideal for complex, unpredictable tasks in hazardous environments. Autonomous robots offer greater efficiency for large-scale operations, but remotely operated robots provide greater flexibility and control in challenging situations. The choice between the two depends heavily on the specific application and the level of risk involved.
Examples of Robots Used in Construction and Engineering
Robot Type | Manufacturer (Example) | Typical Applications |
---|---|---|
Autonomous Excavator | Caterpillar (Concept) | Earthmoving, site preparation |
Remotely Operated Demolition Robot | Brokk | Demolition of hazardous structures, confined space operations |
Collaborative Robot (Cobot) for Bricklaying | Boston Dynamics (Spot, potentially adapted) | Precise and efficient bricklaying |
Autonomous Concrete Pouring Robot | (Emerging Technology) | Precise and efficient concrete placement |
Impact on Productivity and Efficiency
The integration of robotics into construction and engineering is dramatically reshaping the industry’s productivity landscape. Robots are no longer futuristic fantasies; they’re actively tackling complex tasks, accelerating project timelines, and significantly reducing costs. This shift towards automation is leading to a more efficient, precise, and ultimately, safer working environment.
Robots are boosting efficiency in several key ways. Their tireless work ethic eliminates downtime associated with human fatigue and breaks. They can operate continuously, completing repetitive tasks faster and with greater consistency than human workers. This increased speed of operation translates directly into shorter project durations and faster returns on investment for construction companies. Furthermore, robots can perform tasks considered too dangerous or difficult for humans, like working at heights or in confined spaces, thus minimizing safety risks and project delays.
Increased Speed and Throughput in Construction Projects
The use of robotic systems has demonstrably sped up various construction processes. For instance, bricklaying robots can lay bricks at a rate significantly exceeding that of human bricklayers, resulting in faster completion of wall construction. Similarly, robots equipped with 3D printing capabilities are revolutionizing concrete structure construction, producing complex shapes and designs with remarkable speed and accuracy. A notable example is the use of robotic arms in the construction of the Shanghai Tower, where they were instrumental in accelerating the installation of curtain wall panels, a traditionally time-consuming process. The accelerated pace of construction offered by these robotic systems contributes to overall project efficiency and faster project completion.
Robotic Automation’s Effect on Labor Costs and Project Timelines
While the initial investment in robotic systems can be substantial, the long-term impact on labor costs and project timelines often results in significant savings. By automating repetitive and labor-intensive tasks, companies can reduce their reliance on a large human workforce, leading to lower labor costs. Simultaneously, the increased speed and efficiency provided by robots shorten project timelines, reducing overhead expenses and accelerating the return on investment. For example, a study conducted by the Construction Management Association of America (CMAA) found that the implementation of robotic welding in a large-scale infrastructure project resulted in a 30% reduction in labor costs and a 15% decrease in the overall project timeline. This demonstrates the substantial financial benefits of integrating robotics into construction projects.
Reduction of Human Error and Improved Precision
Robots excel at tasks requiring high precision and repeatability, areas where human error can be costly and potentially dangerous. The consistent performance of robots minimizes the risk of mistakes, leading to improved quality control and reduced rework.
- Robots perform tasks with greater precision than humans, leading to less material waste and improved structural integrity.
- Automated systems ensure consistent quality and adherence to specifications, minimizing the need for inspections and corrections.
- Robotics reduces errors associated with manual measurements and calculations, leading to more accurate construction designs.
- Repetitive tasks, prone to human fatigue and error, are executed flawlessly by robots, ensuring consistency and efficiency.
- Robots can operate in hazardous environments, reducing the risk of human injury and related delays.
Safety and Risk Mitigation
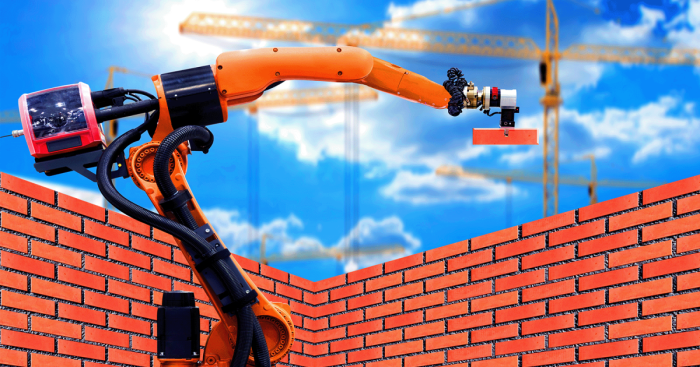
Source: builtin.com
The construction industry is notoriously dangerous, with high rates of workplace accidents and fatalities. Introducing robots into this environment offers a significant opportunity to improve safety and mitigate risks, protecting human workers from harm. By automating hazardous tasks and enhancing precision, robotics technology can dramatically reshape the safety landscape of construction and engineering projects.
Robots reduce workplace accidents and injuries by taking over tasks that are inherently risky for humans. This includes working at heights, handling heavy materials, operating in confined spaces, and exposure to dangerous substances. The precision and repeatability of robotic systems also minimize human error, a major contributor to accidents on construction sites. However, the implementation of robotic systems also introduces its own set of potential risks, which need careful consideration and mitigation strategies.
Benefits of Robots in Hazardous Environments
Robots excel in environments too dangerous for humans. They can operate in areas with high levels of radiation, extreme temperatures, or unstable ground conditions. For instance, robots can inspect and repair aging infrastructure like bridges or pipelines, minimizing the risk to human inspectors working at great heights or in confined spaces. In demolition projects, robots can safely handle explosive charges and remove hazardous materials, reducing the risk of injury or fatality for human workers. Their use in disaster relief scenarios, such as searching collapsed buildings, is another testament to their safety advantages.
Reducing Workplace Accidents and Injuries
The reduction in workplace accidents through robotics is multifaceted. Firstly, robots eliminate human exposure to dangerous situations. Imagine a robot dismantling a hazardous material containment unit; the human worker remains safely distanced, observing the operation remotely. Secondly, the inherent precision of robotic systems minimizes errors that could lead to accidents. A robot precisely placing a beam, for example, reduces the risk of a human miscalculation causing injury or damage. Finally, robots can work continuously without fatigue, reducing errors that might arise from human tiredness or distraction. This consistent performance contributes to a safer work environment.
Potential Risks and Mitigation Strategies
While robots enhance safety, their implementation also introduces new risks. Malfunctioning robots, programming errors, and cybersecurity vulnerabilities are all potential hazards. To mitigate these, robust safety protocols, regular maintenance, and rigorous testing are crucial. Furthermore, adequate training for personnel operating and maintaining these systems is paramount. Effective risk assessment and mitigation planning, which should be an integral part of any robotics integration strategy, is vital for a safe transition. This involves identifying potential hazards, analyzing their likelihood and severity, and implementing appropriate control measures.
Hazards and Robotic Solutions
Potential Hazard | Robotic Solution |
---|---|
Working at Heights | Automated aerial robots for inspection and maintenance |
Handling Heavy Materials | Robotic cranes and manipulators for precise lifting and placement |
Exposure to Hazardous Substances | Robots equipped with sensors and protective measures for handling hazardous materials |
Confined Space Entry | Small, remotely operated robots for inspection and repair in confined spaces |
Repetitive Strain Injuries | Robots automating repetitive tasks, reducing strain on human workers |
Economic and Social Implications
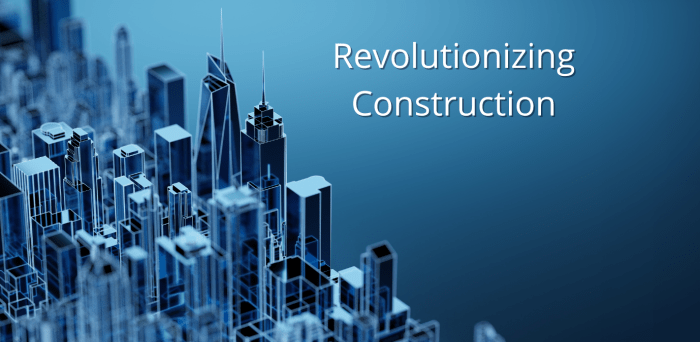
Source: connectedworld.com
Robotics is totally changing the game in construction and engineering, boosting efficiency and safety. Think faster builds, less human error – it’s a game-changer. This efficiency push extends beyond construction; consider how this relates to the future of infrastructure, like the seamless integration of autonomous systems discussed in The Future of Smart Transportation and Autonomous Public Transit.
Ultimately, robotic advancements in construction will pave the way for smarter, more efficient cities, improving overall infrastructure development.
The integration of robotics into construction and engineering presents a complex interplay of economic and social consequences. While offering significant potential for increased productivity and efficiency, the widespread adoption of robotic systems also raises concerns about job displacement and the need for substantial workforce adaptation. Understanding these implications is crucial for navigating this technological shift responsibly and ensuring a just transition for all stakeholders.
The economic impact of robotics on the construction and engineering job market is multifaceted. On one hand, automation can lead to increased efficiency and lower labor costs, potentially boosting overall profitability for companies. This can result in competitive advantages and stimulate economic growth within the sector. On the other hand, the displacement of human workers through automation is a legitimate concern. Certain repetitive or dangerous tasks are prime candidates for automation, potentially leading to job losses in the short term if not managed proactively.
Job Displacement and Workforce Retraining
The potential for job displacement due to robotics in construction and engineering necessitates a proactive approach to workforce retraining and upskilling. While some jobs may become obsolete, new roles will emerge requiring specialized skills in areas such as robotics operation, maintenance, programming, and data analysis. Investing in robust training programs that equip workers with these in-demand skills is essential to mitigating job losses and ensuring a smooth transition. For example, Germany’s “Industry 4.0” initiative has emphasized vocational training and apprenticeships to integrate digital technologies, including robotics, into the workforce, demonstrating a successful strategy for adapting to automation. This approach focuses on equipping workers with the skills necessary to operate and maintain robotic systems, creating new employment opportunities in the process.
Social Implications of Increased Automation
Increased automation in construction and engineering also carries significant social implications. Beyond the economic aspect of job displacement, there are concerns about the potential for increased income inequality, as highly skilled workers who can operate and maintain robotic systems may earn significantly more than those displaced by automation. This could exacerbate existing social disparities if not addressed effectively. Furthermore, the shift towards automation may alter the social dynamics within construction and engineering teams, potentially leading to a decline in interpersonal interactions and a feeling of alienation among workers. However, this could also lead to improvements in working conditions by removing workers from dangerous or physically demanding tasks. Successful integration requires strategies that consider the human element, fostering a collaborative environment between humans and robots.
Strategies for Integrating Robotics While Maintaining Employment
Successful integration of robotics in construction and engineering requires a multifaceted approach that prioritizes both efficiency and worker well-being. This includes investing in comprehensive retraining and upskilling programs, fostering collaboration between human workers and robotic systems, and implementing policies that support a just transition for workers affected by automation. Examples include companies partnering with educational institutions to develop specialized training programs, offering financial assistance for retraining, and providing opportunities for career advancement within the company for workers who adapt to the new technological landscape. Furthermore, focusing on the development of robots for tasks that are dangerous, repetitive, or require extreme precision, rather than simply replacing human labor entirely, can create a more harmonious integration. The construction company Skanska, for example, has successfully implemented robotic solutions while maintaining a focus on employee training and development, showcasing a positive example of responsible technological integration.
Future Trends and Challenges
The construction and engineering industries are on the cusp of a robotic revolution, but significant hurdles remain before widespread adoption becomes a reality. While current applications demonstrate impressive potential, future success hinges on addressing technological limitations and fostering a collaborative environment between humans and machines. This section explores the key trends shaping the future of robotics in these fields, alongside the challenges that must be overcome.
Predicting Future Trends in Robotics for Construction and Engineering
Several key trends are poised to reshape the role of robotics in construction and engineering. Autonomous systems will become increasingly sophisticated, moving beyond pre-programmed tasks to perform more complex operations with minimal human intervention. We can expect to see a rise in collaborative robots (cobots) designed to work safely alongside human workers, enhancing productivity and mitigating risks. Furthermore, the integration of digital twins – virtual representations of physical assets – will allow for precise robot control and improved project planning. For instance, a construction site might utilize a digital twin to simulate the movement of autonomous excavators, optimizing their paths to minimize disruption and maximize efficiency. This level of integration will significantly improve the precision and speed of construction projects.
Technological Challenges Hindering Wider Adoption
Despite the potential, several technological hurdles impede wider robotic adoption. The complexity and variability of construction sites pose significant challenges for robot navigation and task execution. Unpredictable environments, varying weather conditions, and the need for adaptability are key obstacles. Developing robust, reliable, and cost-effective robots capable of handling these challenges remains a significant undertaking. Power management, particularly for battery-powered robots operating in remote locations, is another crucial concern. Furthermore, the integration of various robotic systems into a cohesive workflow requires sophisticated software and communication protocols, adding to the complexity. Consider the difficulty of coordinating multiple autonomous vehicles on a large-scale construction project – ensuring seamless interaction without collisions or delays is a significant technological hurdle.
Enhancing Robotic Capabilities with AI and Machine Learning
Artificial intelligence (AI) and machine learning (ML) are crucial to unlocking the full potential of construction and engineering robots. AI can empower robots with greater autonomy, enabling them to adapt to unforeseen circumstances and learn from experience. ML algorithms can analyze vast datasets of construction data, optimizing robot performance and predicting potential problems. For example, an AI-powered robot might learn to identify and avoid obstacles autonomously, adjusting its path in real-time. Similarly, ML algorithms could analyze sensor data from a robotic excavator to predict potential equipment failures, enabling proactive maintenance and minimizing downtime. This predictive maintenance aspect, enabled by AI and ML, will drastically reduce operational costs and increase project predictability.
Advancements in Materials Science and Robotics, The Role of Robotics in Revolutionizing Construction and Engineering
Advancements in materials science are directly impacting the development of more robust and efficient robots. The use of lighter, stronger, and more durable materials allows for the creation of robots capable of performing more demanding tasks. Similarly, innovations in sensor technology and actuator design are enhancing robot dexterity and precision. For instance, the development of advanced composite materials allows for the construction of lighter and more agile robotic arms, capable of manipulating complex building components with greater accuracy. This synergy between materials science and robotics will lead to the creation of more versatile and capable robots, further revolutionizing the construction and engineering industries. Imagine robots capable of assembling prefabricated modular units with incredible speed and precision, drastically reducing construction time and costs.
Case Studies of Successful Robotic Implementations
The construction and engineering industries are increasingly embracing robotics to boost productivity, enhance safety, and improve overall project outcomes. Several successful projects showcase the transformative potential of these technologies, demonstrating tangible benefits across various aspects of construction and engineering. These case studies highlight not only the capabilities of the robots themselves but also the innovative strategies employed to integrate them effectively into complex workflows.
Automated Bricklaying with SAM
The construction of a 3D-printed house using SAM (Semi-Automated Mason), a robotic bricklaying system developed by Construction Robotics, exemplifies the potential for automation in masonry. SAM, a large, tracked robot, uses a robotic arm to pick up and place bricks with high precision and speed, significantly reducing labor costs and construction time. In one project, SAM laid 3,000 bricks in a single day, outpacing human bricklayers considerably. The system also improved accuracy, minimizing waste and ensuring consistent quality. Challenges included integrating SAM with existing construction processes and developing software capable of interpreting complex building designs. The outcome was a substantial reduction in labor costs (estimated at 60%) and a 20% reduction in construction time compared to traditional methods.
Automated Rebar Tying with Rebar-Tying Robots
Repetitive tasks like rebar tying are both time-consuming and potentially hazardous for human workers. Several companies now offer robotic solutions to automate this process. These robots typically use vision systems and robotic arms to precisely tie rebar, increasing speed and reducing the risk of worker injury. One project using such a robot on a large-scale commercial building reported a 50% increase in tying speed compared to manual labor, translating into substantial cost savings and accelerated project completion. The main challenge involved adapting the robots to handle varying rebar sizes and configurations. The project also highlighted the importance of proper safety protocols around the robots.
Drones for Site Surveying and Inspection
Drones equipped with high-resolution cameras and sensors are revolutionizing site surveying and inspection. These unmanned aerial vehicles (UAVs) can quickly and efficiently capture detailed images and 3D models of construction sites, enabling more accurate progress tracking, early detection of potential problems, and improved safety assessments. One large infrastructure project used drones to create regular site surveys, replacing traditional methods which were time-consuming and prone to inaccuracies. The resulting 3D models allowed project managers to monitor progress precisely, identify potential issues early, and optimize resource allocation. The drone surveys reduced surveying time by 75% and significantly improved the accuracy of progress reporting.
Project Type | Robot Type | Challenges Overcome | Outcomes |
---|---|---|---|
3D-Printed House Construction | Automated Bricklaying Robot (SAM) | Integration with existing processes, software development | 60% reduction in labor costs, 20% reduction in construction time |
Commercial Building Construction | Automated Rebar-Tying Robot | Adapting to varying rebar sizes, safety protocols | 50% increase in tying speed, reduced worker injury risk |
Large Infrastructure Project | Drones for Surveying and Inspection | Data processing and analysis, weather conditions | 75% reduction in surveying time, improved accuracy |
Ethical Considerations
The rise of robots in construction and engineering presents a fascinating, yet complex, ethical landscape. While promising increased efficiency and safety, the widespread adoption of these technologies necessitates a careful consideration of potential biases, accountability, and the very nature of human-robot collaboration in the built environment. Ignoring these ethical dimensions risks exacerbating existing inequalities and creating new challenges.
The integration of robots into construction and engineering raises several crucial ethical questions. These are not merely theoretical concerns; they have tangible impacts on workers, communities, and the overall sustainability of the industry. A proactive and comprehensive approach to ethical considerations is paramount to ensure responsible innovation and equitable benefits from this technological advancement.
Algorithmic Bias in Robotic Design and Deployment
Algorithmic bias, a pervasive issue in artificial intelligence, poses a significant ethical challenge in robotics. The algorithms that govern robotic behavior are trained on data, and if this data reflects existing societal biases (e.g., gender, racial, or socioeconomic), the robots will likely perpetuate and even amplify these biases in their actions. For instance, a robot designed to assess worker performance based on historical data might unfairly penalize workers from underrepresented groups if the historical data reflects pre-existing biases in hiring, promotion, or task assignments. This could lead to discriminatory outcomes and reinforce existing inequalities within the workforce. Mitigation strategies include careful data curation, algorithmic auditing, and the development of fairness-aware algorithms.
Automation and Decision-Making in Construction
Increasing reliance on automation for decision-making in construction projects raises concerns about transparency and accountability. As robots and AI systems take on more complex tasks, including planning, scheduling, and resource allocation, the human element in decision-making diminishes. This shift raises questions about responsibility when errors occur. Who is accountable if a robot makes a mistake that leads to a construction accident or cost overrun? Establishing clear lines of responsibility and developing robust oversight mechanisms are crucial to prevent the erosion of human oversight and accountability. This could involve creating independent auditing processes for robotic systems and establishing clear protocols for human intervention in critical situations.
Transparency and Accountability in Robotic Technologies
Transparency and accountability are essential for building public trust and ensuring the ethical use of robotic technologies in construction and engineering. This includes providing clear information about how robotic systems work, their limitations, and the potential risks associated with their deployment. Openness regarding data sources used to train algorithms and decision-making processes is crucial. Furthermore, mechanisms for redress and dispute resolution should be established in cases of harm or injustice caused by robotic systems. This might involve the development of industry-specific ethical guidelines and regulatory frameworks that promote transparency and accountability. Examples of such initiatives include the development of standardized testing procedures for robotic systems and the establishment of independent certification bodies to ensure compliance with ethical standards.
Closure
The integration of robotics in construction and engineering is not just a technological advancement; it’s a fundamental shift in how we approach building and infrastructure development. While challenges remain, the potential benefits—increased efficiency, improved safety, and innovative design possibilities—are undeniable. The future of construction is robotic, and it’s shaping up to be a remarkably efficient, safer, and innovative era of building.