How 3D Printing is Shaping the Future of Product Manufacturing? Forget clunky assembly lines and sprawling factories. We’re diving headfirst into a revolution where personalized products pop out of machines like magic, transforming everything from design to supply chains. This isn’t just about faster production; it’s about creating a whole new manufacturing landscape, one where customization reigns supreme and sustainability takes center stage. Get ready for a mind-blowing journey into the world of additive manufacturing.
From the intricate designs of aerospace components to the personalized prosthetics revolutionizing healthcare, 3D printing’s impact is undeniable. We’ll explore the various printing methods, dissecting their strengths and weaknesses, and examining how they’re disrupting traditional manufacturing processes. We’ll also look at the environmental impact, the future trends, and the hurdles this innovative technology still needs to overcome to fully unleash its potential.
The Rise of 3D Printing in Manufacturing
The manufacturing landscape is undergoing a dramatic transformation, driven by the rapid advancements and increasing accessibility of 3D printing technology. No longer a niche tool for prototyping, 3D printing, or additive manufacturing, is rapidly becoming a mainstream production method, impacting everything from customized consumer goods to complex industrial components. This shift is fueled by technological improvements, decreasing costs, and the growing demand for personalized and on-demand production.
Historical Development of 3D Printing Technologies
The origins of 3D printing can be traced back to the early 1980s with the development of stereolithography (SLA) by Chuck Hull. This groundbreaking technique, which uses a UV laser to cure liquid resin layer by layer, laid the foundation for many subsequent additive manufacturing processes. The following decades saw the emergence of other key technologies, including fused deposition modeling (FDM), selective laser sintering (SLS), and more recently, binder jetting and multi-jet modeling. Each iteration brought improvements in speed, material compatibility, and precision, steadily broadening the applications of 3D printing. The transition from primarily prototyping tools to production-ready systems has been marked by significant advancements in software, materials science, and automation.
Comparison of 3D Printing Methods
Several key 3D printing methods dominate the manufacturing landscape, each with its own strengths and limitations. Fused Deposition Modeling (FDM) is a relatively inexpensive and accessible method that uses a heated nozzle to extrude molten thermoplastic filament, creating layered objects. It’s well-suited for prototyping and low-volume production of parts in plastics. Stereolithography (SLA) offers higher resolution and smoother surface finishes compared to FDM, utilizing a UV laser to cure liquid photopolymer resin. SLA is ideal for intricate designs and applications requiring high precision, such as dental models or jewelry. Selective Laser Sintering (SLS) uses a laser to fuse powdered materials, such as nylon or metal, layer by layer, creating strong and durable parts. SLS is particularly well-suited for functional prototypes and small-batch production of robust components. The choice of method depends heavily on the desired material properties, required precision, production volume, and budget.
Industries Utilizing 3D Printing for Production
The aerospace industry is a prime example of 3D printing’s impact on manufacturing. Companies are using it to create lightweight, high-strength components for aircraft and spacecraft, reducing weight and improving fuel efficiency. The medical industry also benefits greatly; 3D printing enables the creation of customized prosthetics, surgical guides, and biocompatible implants tailored to individual patients’ needs. In the automotive sector, 3D printing is used for rapid prototyping of vehicle parts, as well as the production of customized interior elements and tooling. The consumer goods industry leverages 3D printing for personalized products, on-demand manufacturing, and the creation of complex designs that would be difficult or impossible to produce using traditional methods.
Cost-Effectiveness of 3D Printing vs. Traditional Manufacturing
The cost-effectiveness of 3D printing versus traditional manufacturing varies significantly depending on the production volume and complexity of the part. For low-volume production, 3D printing often offers a more economical solution, eliminating the need for expensive tooling and setup costs associated with traditional methods like injection molding. However, for high-volume production, traditional methods generally become more cost-effective due to economies of scale.
Production Volume | 3D Printing Cost | Traditional Manufacturing Cost | More Cost-Effective Method |
---|---|---|---|
1-10 units | Relatively High per unit | Very High due to tooling costs | 3D Printing |
10-100 units | Moderate per unit | High, but decreasing per unit | Potentially either, depending on part complexity |
100-1000 units | Decreasing per unit | Significantly lower per unit | Traditional Manufacturing |
>1000 units | High initial investment, then low per unit | Very low per unit | Traditional Manufacturing |
Impact on Product Design and Development
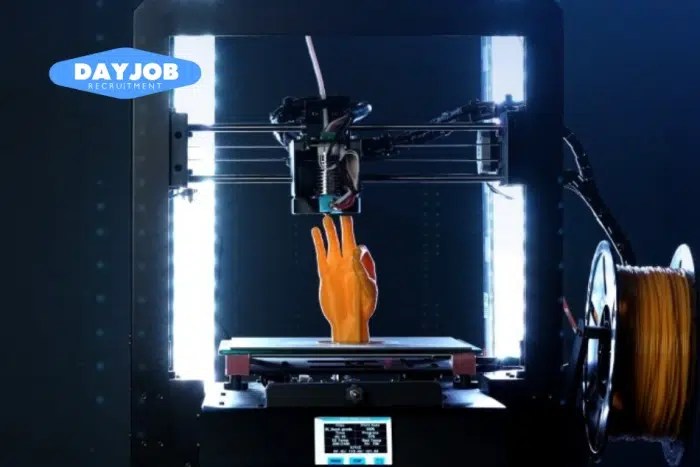
Source: com.au
3D printing’s on-demand production is revolutionizing manufacturing, slashing lead times and boosting customization. This localized production directly impacts global supply chain efficiency, as discussed in this insightful article on The Role of Technology in Enhancing Global Supply Chain Efficiency. Ultimately, 3D printing’s decentralized approach promises a more resilient and responsive future for product manufacturing.
3D printing is revolutionizing product design and development, pushing the boundaries of what’s possible and dramatically accelerating the process. It’s no longer a futuristic concept; it’s a tangible force reshaping industries from aerospace to healthcare. This transformative impact stems from its unique ability to create complex shapes and highly customized products, previously unattainable through traditional manufacturing methods.
The ability to produce intricate designs with ease is a game-changer. Traditional manufacturing processes often involve compromises in design to accommodate limitations in tooling and production techniques. 3D printing, however, allows designers to freely explore complex geometries, internal structures, and customized features, resulting in lighter, stronger, and more efficient products. This freedom unlocks a world of innovation, pushing the boundaries of creativity and functionality.
Rapid Prototyping and Iterative Design
3D printing significantly accelerates the prototyping phase of product development. Instead of waiting weeks or months for prototypes using traditional methods like injection molding, designers can now produce iterations within days, even hours. This rapid prototyping capability enables faster design iterations and allows for quicker feedback loops, ultimately leading to a shorter time-to-market. Companies can test various design concepts quickly and efficiently, identifying flaws and refining designs before committing to large-scale production. This iterative approach, enabled by 3D printing, results in better-optimized products and reduced development costs.
A Hypothetical Product: A Bio-Integrated Medical Implant, How 3D Printing is Shaping the Future of Product Manufacturing
Imagine a custom-designed, bio-integrated medical implant, tailored to the specific anatomical features of a patient. Traditional manufacturing would struggle to create such a personalized device with the required precision and complexity. However, 3D printing allows for the creation of a porous titanium implant with intricate internal channels for drug delivery and a surface texture optimized for bone integration. The design process involved several iterations, each refined using 3D printed prototypes. The ability to quickly create and test different lattice structures, pore sizes, and surface finishes using 3D printing was crucial in optimizing the implant’s biocompatibility and mechanical properties. The final design, created through this iterative process, is a highly personalized implant that integrates seamlessly with the patient’s body, significantly improving treatment outcomes.
Limitations of 3D Printing in Product Design
While 3D printing offers immense advantages, it also presents limitations. Material constraints are a significant factor. The range of printable materials is still narrower than those used in traditional manufacturing. While advancements are constantly being made, there are limitations in terms of material strength, durability, and biocompatibility, depending on the specific application. Another challenge is scaling up production. While 3D printing excels in producing individual prototypes or small batches, scaling up to mass production can be costly and time-consuming compared to established manufacturing methods. The speed of printing and the cost per unit often become limiting factors when transitioning from prototyping to large-scale manufacturing.
Transforming Supply Chains and Production Processes
Forget sprawling factories and lengthy shipping routes. 3D printing is poised to revolutionize how we manufacture products, offering a radical shift towards decentralized production and on-demand manufacturing. This means a future where goods are produced closer to the point of consumption, drastically altering traditional supply chains and reshaping the manufacturing landscape.
3D printing’s ability to create complex parts directly from digital designs eliminates the need for large-scale warehousing and extensive transportation networks. This decentralized approach reduces reliance on global supply chains, making businesses more resilient to disruptions like geopolitical instability or natural disasters. The shift towards localized production empowers companies to respond swiftly to changing market demands and customize products to meet specific needs.
Decentralized Manufacturing and On-Demand Production
The ability to manufacture products on-demand, closer to the end-user, is a game-changer. Imagine a world where spare parts for a broken appliance are printed at home, eliminating weeks of waiting and shipping costs. This is the promise of decentralized manufacturing fueled by 3D printing. This localized production model reduces transportation costs and lead times significantly, leading to increased efficiency and reduced environmental impact. Companies can establish smaller, more agile production facilities closer to their target markets, fostering faster response times and improved customer satisfaction. This also empowers smaller businesses and entrepreneurs, leveling the playing field by removing the barriers to entry associated with traditional manufacturing.
Implications for Inventory Management and Logistics
3D printing dramatically impacts inventory management. Instead of holding vast quantities of finished goods or raw materials in warehouses, companies can maintain smaller inventories of raw materials and produce finished goods only when needed. This reduces storage costs, minimizes waste from obsolete stock, and frees up capital. However, the transition also presents challenges. The need for reliable and readily available 3D printing materials and skilled operators needs to be addressed. Furthermore, quality control and managing the complexities of a distributed manufacturing network require careful planning and implementation. Despite these challenges, the potential benefits of reduced inventory costs and improved responsiveness significantly outweigh the drawbacks.
Examples of Localized Production
Several companies are already leveraging 3D printing for localized production, demonstrating the technology’s transformative potential. For example, some medical device manufacturers are using 3D printing to produce customized prosthetics and implants on-site, drastically reducing lead times and improving patient outcomes. Similarly, aerospace companies are employing 3D printing to create lightweight, high-strength components, leading to fuel efficiency improvements and reduced manufacturing costs. These examples showcase the tangible benefits of reduced transportation costs and shortened lead times associated with localized production through 3D printing.
Integrating 3D Printing into Existing Manufacturing Supply Chains
Successfully integrating 3D printing into an existing supply chain requires a strategic approach. Here are the key steps involved:
- Assess Current Supply Chain: Analyze existing processes to identify areas where 3D printing can provide the greatest value.
- Identify Suitable Applications: Determine which products or components are best suited for 3D printing based on design complexity, material requirements, and production volume.
- Select Appropriate Technology: Choose 3D printing technologies that meet the specific needs of the application, considering factors such as material compatibility, speed, and accuracy.
- Develop a Pilot Program: Implement a small-scale pilot program to test the feasibility and effectiveness of 3D printing in the selected application.
- Scale Up Production: Gradually increase production volume as confidence in the process grows and the technology matures.
- Monitor and Optimize: Continuously monitor performance metrics and make adjustments as needed to optimize the 3D printing process within the supply chain.
Sustainability and the Environmental Impact: How 3D Printing Is Shaping The Future Of Product Manufacturing
3D printing, while revolutionary, isn’t without its environmental footprint. However, a closer look reveals a complex picture, with potential for significant sustainability gains alongside existing challenges. The environmental impact isn’t a simple “good” or “bad” equation; it depends heavily on the specific materials used, the scale of production, and the design of the printing process itself.
The environmental benefits of 3D printing are compelling in certain contexts. Reduced material waste, for example, is a key advantage. Traditional manufacturing often involves significant material loss during machining or subtractive processes. 3D printing, being an additive process, uses only the necessary material, minimizing scrap. Furthermore, localized production reduces transportation emissions associated with shipping parts globally. In some applications, energy consumption can also be lower compared to traditional methods, particularly when using lower-energy materials and processes.
Comparison of Carbon Footprints: 3D Printing vs. Traditional Manufacturing
Let’s consider a specific example: the production of a simple plastic part, say, a phone case. Traditional injection molding involves creating a mold, which is energy-intensive and often produces significant waste. The manufacturing process itself also consumes energy and releases greenhouse gases. In contrast, 3D printing a phone case using a bioplastic filament sourced locally could have a considerably smaller carbon footprint. While the energy used in the 3D printing process needs to be factored in, the reduced material waste and transportation distances can significantly offset this. However, this comparison is highly dependent on the specific materials used in both processes and the energy sources employed. A life cycle assessment (LCA) would be necessary to accurately quantify the differences. A comprehensive LCA considers all stages from material extraction to product disposal.
Challenges in the Sustainability of 3D Printing Materials
One major hurdle to widespread adoption of sustainable 3D printing is the availability of truly eco-friendly materials. Many commonly used filaments are derived from petroleum, negating some of the environmental benefits. While bioplastics offer a promising alternative, their production and biodegradability can vary significantly. Furthermore, the recyclability of 3D-printed objects is often limited. The complex geometries of many 3D-printed parts make them difficult to recycle using traditional methods. Research into biodegradable and easily recyclable filaments, along with the development of closed-loop recycling systems for 3D-printed materials, is crucial for improving the overall sustainability of the technology.
Challenges in the Disposal of 3D-Printed Products
The end-of-life management of 3D-printed products presents another significant challenge. Unlike mass-produced items, 3D-printed products often have unique designs and compositions, making it difficult to establish efficient recycling or disposal processes. The disposal of materials, particularly those derived from petroleum, can lead to environmental pollution. Developing effective strategies for recycling or composting 3D-printed objects, along with clear labeling and guidance for consumers, is essential to minimize the environmental impact at the end of a product’s lifecycle.
Lifecycle of a 3D-Printed Product: A Visual Representation
Imagine a diagram showing the lifecycle of a 3D-printed toothbrush made from a bioplastic filament.
Stage 1: Material Extraction: The diagram shows the harvesting of plant biomass (e.g., corn starch) for bioplastic production. This stage highlights potential land use impacts and energy consumption in farming.
Stage 2: Material Processing: The diagram shows the transformation of plant biomass into bioplastic filament, with associated energy use and potential waste streams.
Stage 3: 3D Printing: The diagram depicts the 3D printing process, showing minimal material waste compared to traditional manufacturing. The energy consumption of the 3D printer is also represented.
Stage 4: Product Use: The diagram shows the toothbrush in use, highlighting its lifespan and potential for reuse or repurposing.
Stage 5: End-of-Life: The diagram shows two paths: biodegradation in a compost environment (if the bioplastic is truly biodegradable) or recycling if a suitable recycling system exists. If neither is available, the diagram indicates disposal in landfill, highlighting potential environmental consequences. The overall visual representation emphasizes the reduced material waste in the manufacturing process but also highlights the importance of sustainable material choices and end-of-life management for minimizing overall environmental impact.
Future Trends and Challenges
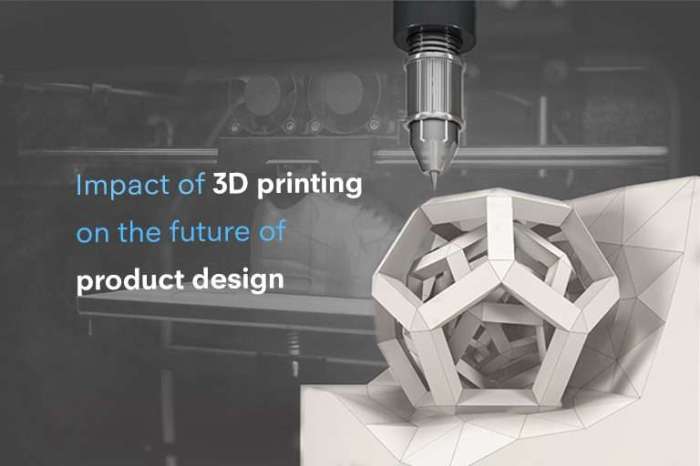
Source: strate.in
The future of 3D printing in manufacturing is a dynamic landscape, poised for explosive growth but also facing significant hurdles. Advancements in technology are constantly pushing the boundaries of what’s possible, while economic and logistical challenges remain. Understanding both the opportunities and obstacles is crucial for navigating this exciting yet complex terrain.
Emerging Trends in 3D Printing Technologies
Material science is undergoing a revolution alongside 3D printing. We’re seeing the development of new polymers with enhanced properties like increased strength, flexibility, and biocompatibility. Metals are becoming easier to print with higher precision and less post-processing, opening doors for complex aerospace and medical device applications. The integration of artificial intelligence (AI) and machine learning (ML) is automating various aspects of the 3D printing process, from optimizing print parameters to predicting potential failures, leading to increased efficiency and reduced waste. For instance, AI-powered software can analyze the design and suggest optimal print settings, minimizing material usage and improving print quality. This automation is not only increasing speed but also improving the overall quality and consistency of 3D-printed products.
Personalized Mass Production and Customized Products
3D printing’s ability to create highly customized products on demand is transforming industries. Imagine a future where consumers can design and order personalized shoes, perfectly fitted prosthetics, or even customized medications, all produced using 3D printing. This level of personalization is driving a shift towards mass customization, where products are tailored to individual needs and preferences without significantly increasing production costs. Companies like Nike are already utilizing 3D printing for customized shoe soles and other components, demonstrating the potential of this technology to revolutionize product design and consumer experience. This personalized approach is particularly impactful in healthcare, where customized implants and medical devices can be produced rapidly and precisely, improving patient outcomes.
Challenges Facing Widespread Adoption of 3D Printing
Despite its potential, widespread adoption of 3D printing in manufacturing faces significant challenges. Cost remains a major barrier, especially for large-scale production. The initial investment in 3D printing equipment can be substantial, and the cost of materials, particularly specialized materials like high-performance polymers and metals, can be significantly higher than traditional manufacturing methods. Scalability is another challenge; while 3D printing excels at producing unique, complex parts, scaling up production to meet the demands of mass markets can be difficult and expensive. Finally, a skilled workforce is essential for operating and maintaining 3D printing equipment and for designing and optimizing 3D-printable products. The shortage of skilled technicians and engineers poses a significant hurdle to the widespread adoption of this technology.
A Future Scenario: 3D Printing in Aerospace
Consider the aerospace industry. In the near future, 3D printing could revolutionize aircraft manufacturing. Instead of relying on complex and time-consuming traditional methods, manufacturers could use 3D printing to create lightweight, high-strength components with intricate internal structures, optimizing performance and reducing weight. This could lead to significant fuel savings and reduced carbon emissions. Furthermore, on-demand manufacturing of spare parts using 3D printing could drastically reduce downtime and maintenance costs, especially for aircraft operating in remote locations. Imagine a scenario where a damaged part on a plane in mid-flight could be remotely diagnosed, and a replacement part could be 3D-printed on-site at the next airport, minimizing delays and ensuring safety. This scenario highlights the potential of 3D printing to not only enhance the efficiency and sustainability of aerospace manufacturing but also to improve safety and reliability.
Conclusion
The rise of 3D printing isn’t just a technological advancement; it’s a paradigm shift. It’s redefining how we design, produce, and distribute goods, promising a future of hyper-personalized products, localized manufacturing, and a more sustainable approach to production. While challenges remain, the potential of 3D printing to reshape industries and revolutionize our consumption habits is undeniable. Buckle up, because the future of manufacturing is being printed, one layer at a time.