The Impact of Robotics in Reducing Human Error in Manufacturing is revolutionizing the factory floor. Forget clunky, predictable robots of the past; today’s automated systems are precise, adaptable, and increasingly intelligent. This isn’t just about replacing humans; it’s about augmenting capabilities and creating a safer, more efficient manufacturing process. We’re diving deep into how robots are tackling common human errors, boosting productivity, and ultimately, changing the game for good.
From assembly line hiccups to quality control snafus, human error is a costly and sometimes dangerous reality in manufacturing. But what if we could drastically minimize these issues? This exploration examines the various types of robots employed, the specific human errors they address, and the economic and safety benefits that follow. We’ll also peek at the challenges and future trends shaping this exciting field.
Introduction to Robotics in Manufacturing
The rise of robots in manufacturing isn’t a futuristic fantasy; it’s a deeply ingrained part of modern production. From the clunky, hydraulic arms of the early days to the sophisticated, AI-powered systems of today, robots have revolutionized how we make things, significantly impacting efficiency, precision, and safety. This evolution has led to a dramatic reduction in human error and a substantial increase in overall output.
The integration of robots into manufacturing processes has been a gradual yet transformative journey. Early industrial robots, appearing in the late 1950s and early 1960s, were primarily used for simple, repetitive tasks. These early models were often large, expensive, and lacked the dexterity and adaptability of their modern counterparts. However, they paved the way for significant advancements in robotics technology, leading to the development of more sophisticated and versatile robotic systems. This progress was fueled by continuous improvements in computing power, sensor technology, and control algorithms.
Types of Robots Used in Manufacturing
Several types of robots are employed in manufacturing, each suited to specific tasks and environments. The choice of robot depends on factors like the complexity of the task, the required precision, the payload capacity, and the overall production layout. Understanding these different types is key to appreciating the breadth of robotic applications in manufacturing.
- Articulated Robots: These are the most common type, featuring rotary joints that allow for a wide range of movement. They resemble a human arm and are highly versatile, capable of handling various tasks such as welding, painting, and assembly.
- Cartesian Robots (Gantry Robots): These robots move along three linear axes (X, Y, and Z) and are often used for pick-and-place operations, machining, and 3D printing. Their precise linear motion makes them ideal for applications requiring high accuracy.
- SCARA Robots: Selective Compliance Assembly Robot Arm robots are designed for high-speed assembly tasks. They excel at handling lightweight objects with precision and speed, making them suitable for electronics assembly and other delicate operations.
- Collaborative Robots (Cobots): Designed to work alongside human workers, cobots are equipped with safety features that allow them to operate in close proximity without posing a risk. They are often used for tasks that require both human dexterity and robotic precision, such as machine tending or quality inspection.
Examples of Robotic Applications in Manufacturing
Robots are no longer confined to a single sector of manufacturing; their applications are vast and diverse. The increasing sophistication of robots and the development of advanced control systems have broadened their capabilities, leading to their adoption across various industries.
- Welding: Robots perform consistent, high-quality welds, reducing inconsistencies and improving safety for human workers who would otherwise be exposed to hazardous conditions.
- Painting: Robotic painting systems ensure even coating application, minimizing waste and improving the quality of the final product. They can also operate in environments hazardous to human workers.
- Assembly: Robots are crucial in assembling complex products, from automobiles to electronics. Their precision and speed significantly improve assembly efficiency and reduce errors.
- Material Handling: Robots are used extensively for moving materials within factories, from transporting raw materials to stacking finished products. This reduces the physical strain on human workers and improves overall logistics.
- Quality Inspection: Equipped with advanced sensors and vision systems, robots can perform precise quality inspections, identifying defects that might be missed by human inspectors. This improves product quality and reduces waste.
Types of Human Error Reduced by Robotics
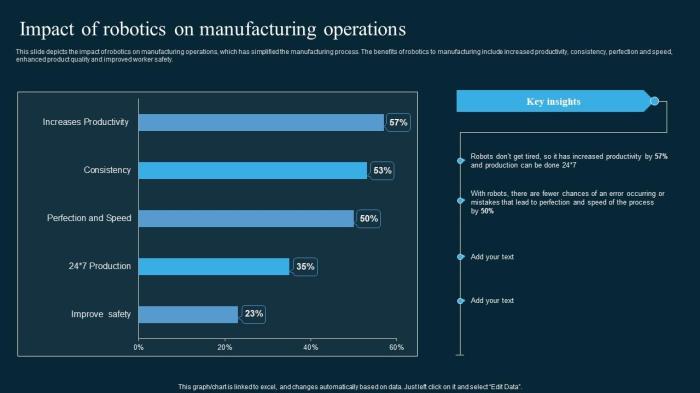
Source: slideteam.net
Let’s face it, humans are prone to mistakes. In the fast-paced world of manufacturing, even small errors can have significant consequences, leading to production delays, damaged goods, and ultimately, lost revenue. Robotic automation offers a powerful solution by minimizing these human errors and boosting overall efficiency.
Robotic systems excel at performing repetitive tasks with unwavering precision, a stark contrast to human capabilities which can fluctuate due to fatigue, distraction, or even momentary lapses in concentration. This leads to a significant reduction in several common types of manufacturing errors.
Assembly Errors
Incorrect assembly is a frequent culprit in manufacturing inefficiencies. Humans, especially when performing repetitive tasks, can easily misalign parts, forget steps, or use incorrect force, leading to faulty products. Robots, programmed with precise assembly instructions, consistently perform these tasks to the same exacting standards, dramatically reducing assembly errors. For example, in the automotive industry, robotic arms are used to precisely weld car body panels, ensuring consistent quality and eliminating the human error associated with inconsistent welding strength or misalignment.
Measurement Errors
Accurate measurement is critical for quality control. Human measurement, however, is susceptible to inconsistencies influenced by factors like tool calibration, operator skill, and even environmental conditions. Robotic systems equipped with sensors and vision systems provide highly accurate and consistent measurements, minimizing discrepancies and improving the overall accuracy of the manufacturing process. Imagine a pharmaceutical company using robots to precisely measure and dispense active ingredients – the consistency is paramount to product safety and efficacy.
Quality Control Errors
Human inspectors, while valuable, can miss defects due to fatigue or oversight, especially when inspecting large volumes of products. Robotic vision systems, combined with advanced algorithms, can detect subtle defects that might escape human eyes, leading to a significant increase in product quality and a reduction in the number of defective items leaving the factory. For instance, a food processing plant could employ robots with vision systems to identify and remove damaged or spoiled products from a conveyor belt, ensuring only high-quality items reach consumers.
Comparative Error Rates
Let’s illustrate the impact of robotics with a hypothetical example focusing on a smartphone assembly line:
Process | Human Error Rate | Robotic Error Rate | Percentage Improvement |
---|---|---|---|
Component Insertion | 2% | 0.2% | 90% |
Screw Tightening | 1.5% | 0.1% | 93.3% |
Visual Inspection | 0.8% | 0.05% | 93.75% |
This table demonstrates the significant reduction in error rates achievable through robotic automation. While these numbers are hypothetical, they reflect the general trend observed in numerous real-world manufacturing applications. The consistent precision of robots leads to a substantial improvement in product quality and reduces waste associated with human error.
Specific Robotic Applications and Error Reduction
The integration of robots into manufacturing processes isn’t just about automation; it’s a strategic move towards significantly improving precision, consistency, and overall product quality. By minimizing human error, robotics contributes to higher yields, reduced waste, and ultimately, a stronger bottom line. Let’s delve into specific robotic applications that exemplify this error reduction.
Robotic arms, with their unparalleled precision and repeatability, are revolutionizing assembly lines. Their impact on reducing assembly errors is substantial, leading to higher-quality products and increased efficiency.
Robotic Arms in Precision Assembly
Robotic arms excel in tasks requiring intricate movements and consistent force application – areas where human fatigue and variability can lead to mistakes. For example, in the assembly of microelectronic components, a robotic arm can place tiny parts with sub-millimeter accuracy, consistently repeating the same action thousands of times without deviation. This eliminates the inconsistencies inherent in manual assembly, reducing errors related to misalignment, incorrect placement, and damage to delicate components. The result is a significant increase in yield and a decrease in costly rework or scrap. Furthermore, robotic arms can operate in hazardous environments, further mitigating human error risks.
Vision Systems in Robotic Quality Control
Vision systems are the “eyes” of robotic quality control. These systems use cameras and sophisticated image processing software to inspect products for defects, inconsistencies, or deviations from specifications. This automated inspection process dramatically reduces human error in quality control, which can be subjective and prone to fatigue. A vision system can consistently identify minute flaws that might be missed by a human inspector, ensuring consistent quality across the entire production run. For instance, a vision system might detect a hairline crack in a weld, a slight discoloration in a painted surface, or a missing component in an assembled product – all with far greater speed and accuracy than a human inspector.
Robotic Welding System in Automotive Manufacturing, The Impact of Robotics in Reducing Human Error in Manufacturing
Imagine a car manufacturing plant using a robotic welding system. This system would consist of a six-axis robotic arm equipped with a specialized welding torch. The robot would be programmed with precise welding parameters based on the vehicle’s design, ensuring consistent weld quality and penetration. A vision system would monitor the welding process, verifying that the weld is being applied correctly and identifying any defects in real-time. This system would replace human welders who are susceptible to fatigue, inconsistent welding techniques, and potential safety risks associated with working with molten metal. The robotic system’s consistent performance and ability to work continuously without breaks would lead to significant improvements in welding quality, reduced defect rates, and enhanced overall productivity. This automated system also eliminates the risk of human error leading to faulty welds, potentially causing safety hazards in the finished vehicle. The cost savings from reduced rework and improved product quality would also be substantial.
Economic and Safety Impacts of Reduced Human Error
The integration of robotics into manufacturing processes isn’t just about technological advancement; it’s a strategic move with significant economic and safety ramifications. By minimizing human error, manufacturers can unlock substantial cost savings, boost productivity, and create a safer working environment. This section delves into the tangible benefits derived from reduced human error, highlighting the financial gains and improved workplace safety resulting from robotic automation.
Reduced human error translates directly into a healthier bottom line and a more secure workplace. The elimination of defects, minimized downtime, and enhanced worker safety all contribute to a significant return on investment for businesses embracing robotic automation. Let’s explore these impacts in detail.
Cost Savings from Reduced Waste and Improved Quality
Implementing robotics significantly reduces waste in manufacturing. Human error contributes to material spoilage, defective products, and rework, all of which incur substantial costs. Robots, programmed with precision, minimize these errors. This leads to less material waste, fewer rejected products, and a higher yield of sellable goods. The consistent quality produced by robots also reduces the need for extensive quality control checks, further lowering operational costs. For example, a car manufacturer might see a 15% reduction in paint defects alone by using robotic painting systems, saving millions annually. This improvement translates to increased profitability and a stronger competitive edge.
Increased Production Efficiency and Output
Robots operate at consistent speeds and maintain a constant output, unlike human workers who can experience fatigue or variability in performance. This consistency translates to higher production efficiency. Robots can work around the clock, increasing overall production volume and meeting higher demands without additional labor costs. Imagine a factory producing electronic components: robots can assemble these components much faster and more accurately than human workers, resulting in a substantially increased output and quicker delivery times. The economic benefits are obvious: higher sales, faster turnaround, and enhanced market responsiveness.
Safety Improvements in the Manufacturing Environment
Robotic automation significantly enhances workplace safety by taking on dangerous or repetitive tasks that pose risks to human workers. This reduces the likelihood of workplace accidents, injuries, and fatalities, resulting in lower insurance premiums and reduced compensation claims. Tasks such as handling heavy materials, working in hazardous environments (e.g., high temperatures, chemical exposure), and performing repetitive motions are prime candidates for robotic automation. For instance, in the automotive industry, robots handle welding and painting tasks, eliminating the risk of burns or exposure to harmful chemicals for human workers.
Data Demonstrating Cost Savings and Safety Improvements
The economic and safety benefits of robotic automation are supported by substantial data. Consider these examples:
- A study by the Boston Consulting Group found that companies using robotics extensively saw a 20-30% reduction in manufacturing costs.
- The National Safety Council reports that workplace injuries and fatalities have decreased significantly in industries with high levels of robotic automation.
- A survey by the Robotic Industries Association indicated that companies implementing robotics experienced a 10-15% increase in productivity.
- Several case studies show that the return on investment (ROI) for robotic automation in manufacturing can range from 15% to 30% within the first three years.
While specific figures vary depending on the industry and the specific application, the overall trend is clear: robotic automation significantly improves both the economic performance and safety profile of manufacturing operations. The investment in robotics translates to substantial long-term benefits.
Challenges and Limitations of Robotic Implementation: The Impact Of Robotics In Reducing Human Error In Manufacturing
Automating manufacturing with robots promises significant gains, but the path to a fully robotized factory isn’t paved with gold. Significant hurdles exist, impacting both the initial investment and the long-term operational efficiency. Understanding these challenges is crucial for businesses considering robotic integration.
The transition to robotic systems in manufacturing isn’t a simple switch-flip. High upfront costs, complex integration processes, and the potential for job displacement are just some of the obstacles companies face. Furthermore, current robotic technology isn’t a perfect replacement for human workers; there are limitations that necessitate continued human involvement in various manufacturing tasks.
Robots are revolutionizing manufacturing, slashing human error rates in assembly and quality control. This precision extends beyond the factory floor; think about the seamless global supply chains, where accuracy is paramount. The transparency and security offered by blockchain, as explored in The Role of Blockchain in Redefining Cross-Border Transactions , are crucial for efficient, error-free logistics, ultimately feeding back into the robotic precision of the manufacturing process itself.
The result? A future of flawless production, from start to finish.
Initial Investment Costs and Return on Investment (ROI)
Implementing robotic systems demands substantial upfront capital. The cost includes purchasing the robots themselves, specialized software, integration with existing infrastructure, and employee training. This high initial investment can be a significant barrier for smaller manufacturers or those with limited financial resources. A thorough cost-benefit analysis, projecting ROI over the lifespan of the robotic system, is essential to justify the expenditure. Factors like increased productivity, reduced waste, and improved product quality contribute to the overall ROI, but careful planning and realistic projections are critical. For example, a small bakery might find the cost of a robotic bread-slicing machine prohibitive, while a large-scale car manufacturer could easily absorb the expense given the volume of production.
Integration Complexities and System Compatibility
Integrating robots into existing manufacturing processes isn’t always straightforward. Robots need to seamlessly interact with other machinery, software, and human workers. This requires careful planning, specialized expertise, and often, significant modifications to the existing production line. Compatibility issues between different robotic systems and existing equipment can lead to delays, increased costs, and operational disruptions. Imagine trying to integrate a new, cutting-edge robotic arm into a factory still running on outdated PLC systems – the compatibility challenges would be immense.
Potential for Job Displacement and Workforce Reskilling
The introduction of robots into manufacturing inevitably raises concerns about job displacement. While robots can automate repetitive or dangerous tasks, they can also replace human workers, leading to unemployment and social disruption. Addressing this concern requires proactive strategies, such as investing in workforce reskilling and retraining programs to equip employees with the skills needed for new roles in a robotized environment. For instance, factory workers previously operating assembly lines might be retrained to maintain and program the robots themselves, creating new high-skill job opportunities.
Limitations of Current Robotic Technology and the Need for Human Intervention
Despite advancements, current robotic technology has limitations. Robots often struggle with tasks requiring dexterity, adaptability, and problem-solving skills that humans possess naturally. Situations requiring creativity, judgment, or handling unforeseen circumstances still demand human intervention. For example, a robot might excel at welding identical parts but struggle to adapt to minor variations in the material or assembly process, requiring a human worker to intervene and make adjustments.
Comparison of Human Workers and Robots in Manufacturing
Aspect | Human Workers | Robots | Considerations |
---|---|---|---|
Cost | Lower initial cost, higher long-term cost (wages, benefits) | Higher initial cost, lower long-term operational cost | Consider total cost of ownership (TCO) over the system’s lifespan. |
Adaptability | Highly adaptable to changing conditions and tasks | Limited adaptability, requires reprogramming for new tasks | Evaluate the flexibility needed for future production changes. |
Dexterity and Precision | High dexterity for complex tasks, but prone to errors | High precision for repetitive tasks, but limited dexterity | Balance the need for precision and adaptability in task selection. |
Problem-Solving | Excellent problem-solving and decision-making capabilities | Limited problem-solving abilities, requires human oversight | Consider the complexity of tasks and the need for real-time decision-making. |
Future Trends and Developments
The manufacturing landscape is undergoing a dramatic transformation, driven by advancements in robotics and artificial intelligence. These innovations promise to further minimize human error and boost efficiency to unprecedented levels. The integration of sophisticated technologies is not just about replacing human workers; it’s about creating collaborative environments where humans and robots work synergistically, leveraging each other’s strengths.
The next generation of robots is poised to revolutionize error reduction in manufacturing through enhanced capabilities and collaborative functionalities. This evolution will lead to safer, more efficient, and ultimately, more profitable manufacturing processes.
Collaborative Robots (Cobots) and Their Impact
Cobots, unlike traditional industrial robots, are designed to work alongside humans in shared workspaces. Their inherent safety features, such as force limiting capabilities and collaborative functionalities, minimize the risk of accidents and allow for a more flexible and efficient production line. This collaborative approach allows for tasks to be divided optimally, utilizing human dexterity and problem-solving skills alongside the robot’s precision and tireless repetition. For example, a cobot might handle repetitive assembly tasks while a human operator performs more complex quality control checks or handles unexpected situations. This division of labor reduces the probability of human error stemming from fatigue or repetitive strain injuries. The integration of cobots leads to improved accuracy in assembly, reduced defect rates, and enhanced overall product quality.
AI-Powered Robots and Enhanced Error Detection
The integration of artificial intelligence significantly enhances the capabilities of robots, leading to more sophisticated error detection and prevention mechanisms. AI-powered robots can learn from data, adapt to changing conditions, and make decisions autonomously, minimizing the likelihood of human-induced errors. For instance, AI algorithms can analyze sensor data from robots in real-time, identifying anomalies and potential errors before they escalate into significant problems. This predictive capability allows for proactive interventions, preventing costly downtime and improving overall product quality. Imagine an AI-powered robot on a car assembly line that detects a slight misalignment in a part before it’s fully installed, immediately alerting a human operator to correct the issue—preventing a potentially significant and costly defect.
Projected Growth of Robotics in Manufacturing
The projected growth of robotics in manufacturing over the next decade can be visualized as an upward-sloping curve on a graph. The X-axis represents the years (2024-2034), and the Y-axis represents the global market value of industrial robots (in billions of US dollars). The curve starts at a relatively high point, reflecting the current market size, and steadily increases at an accelerating rate, demonstrating exponential growth. Key milestones along the curve could highlight specific years with significant market expansions, perhaps driven by technological breakthroughs or large-scale industry adoption. The curve’s steepness illustrates the rapid pace of innovation and adoption expected within the manufacturing sector. The visual could also include annotations to indicate projected market shares of different robot types (e.g., cobots, AI-powered robots), demonstrating the shift toward more advanced robotic technologies.
This projected growth is supported by numerous industry reports and analyses which consistently point towards a significant increase in robotic deployment across various manufacturing sectors, driven by factors such as increasing labor costs, the need for enhanced productivity, and the desire to improve product quality and consistency. For example, the International Federation of Robotics (IFR) publishes annual statistics that provide a strong basis for such projections. The growth is expected to be particularly strong in industries with high-volume production, complex assembly processes, or hazardous working conditions.
Final Conclusion
The integration of robotics in manufacturing isn’t just a trend; it’s a fundamental shift towards a future where precision, safety, and efficiency reign supreme. While challenges remain – from initial investment costs to the need for skilled technicians – the potential benefits are undeniable. The ongoing advancements in AI and collaborative robots promise even greater error reduction and a closer partnership between humans and machines on the factory floor. The future of manufacturing is automated, and it’s looking pretty bright.