The Evolution of Autonomous Robots in Industrial Applications: From clunky, pre-programmed behemoths to the sleek, AI-powered collaborators of today, the journey of robots in factories is a wild ride. We’re talking a transformation that’s reshaped entire industries, boosting efficiency and pushing the boundaries of what’s possible. Get ready to explore this incredible evolution, from the early days of simple automation to the sophisticated, intelligent systems shaping our future.
This deep dive will unpack the key milestones: the rise of programmable robots, the crucial role of sensors and AI, and the exciting possibilities of human-robot collaboration. We’ll look at real-world examples, showcasing how autonomous robots are revolutionizing manufacturing, logistics, and beyond. Buckle up, because this is one technological revolution you won’t want to miss.
Early Stages of Industrial Robots
The journey of industrial robots began not with sleek, articulated arms, but with much simpler automated machinery. These early systems, while lacking the sophisticated intelligence of modern robots, laid the groundwork for the advancements we see today. Their impact on manufacturing efficiency and worker safety, albeit limited initially, was undeniable and spurred further innovation.
Early industrial automation focused on performing repetitive, dangerous, or physically demanding tasks. Think assembly lines in the early 20th century, where simple mechanisms and specialized tools replaced human labor for specific, often isolated operations. This wasn’t robotics as we understand it now, but it was the crucial first step toward automation.
Early Robotic Systems and Their Limitations
The first true industrial robots emerged in the mid-20th century. These early systems were typically large, unwieldy, and lacked the dexterity and adaptability of their modern counterparts. They were often programmed to perform a single, pre-defined task with limited flexibility. For example, Unimation’s Unimate, one of the first commercially successful industrial robots, was primarily used for die casting and spot welding in General Motors factories. Its operation relied on pre-programmed sequences, making it unsuitable for tasks requiring any deviation from the set instructions. The limitations were significant: lack of sensory feedback, limited programmability, and slow operational speeds. These early robots were essentially programmable manipulators, far from the intelligent systems we see today. Their success, however, demonstrated the potential for automating complex industrial processes.
Technological Advancements Leading to Sophisticated Robots
Several key technological advancements propelled the evolution of industrial robots beyond their rudimentary beginnings. The development of more powerful and reliable microprocessors drastically increased processing power, enabling more complex control systems and improved programming capabilities. Simultaneously, advancements in sensor technology – including vision systems, force sensors, and proximity sensors – provided robots with the ability to perceive their environment and react accordingly. This “sensory feedback” allowed for more precise movements and adaptability, moving beyond simple pre-programmed routines. Furthermore, the development of more robust and flexible robotic arms, incorporating advanced materials and designs, enhanced their dexterity and operational range. The convergence of these technological advancements – increased computing power, sophisticated sensors, and improved mechanical design – formed the foundation for the next generation of more intelligent and adaptable industrial robots.
The Rise of Programmable Robots: The Evolution Of Autonomous Robots In Industrial Applications
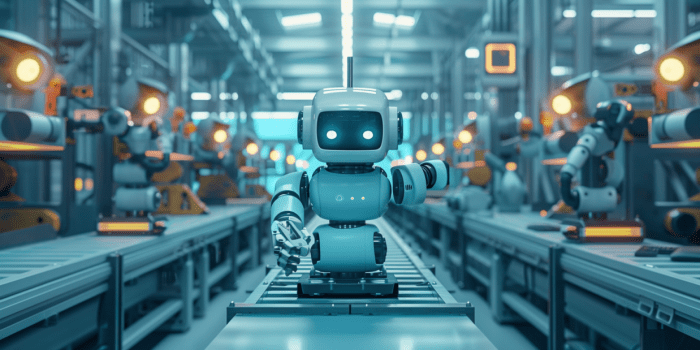
Source: ctfassets.net
The dawn of programmable robots marked a pivotal shift in industrial automation, moving beyond the rigid, pre-programmed machines of the early era. This revolution was fueled by advancements in computing power and the development of sophisticated control systems, most notably the programmable logic controller (PLC). The ability to reprogram robots for different tasks dramatically increased their versatility and economic viability, paving the way for widespread adoption across diverse industries.
The impact of programmable logic controllers (PLCs) on industrial automation cannot be overstated. PLCs acted as the brain of automated systems, providing a flexible and reliable method for controlling complex sequences of operations. Unlike hardwired systems, PLCs allowed for easy reprogramming, adapting production lines to changing demands with minimal downtime. This flexibility reduced production costs, improved efficiency, and enabled manufacturers to respond more quickly to market changes. The introduction of user-friendly programming interfaces further democratized automation, allowing a wider range of technicians to participate in designing and maintaining automated systems.
Generations of Industrial Robots and Their Capabilities, The Evolution of Autonomous Robots in Industrial Applications
Industrial robots have evolved through several generations, each marked by significant improvements in capabilities. First-generation robots were essentially simple, point-to-point manipulators, limited in their movements and requiring extensive manual programming for each task. Subsequent generations saw the introduction of more sophisticated control systems, allowing for continuous path control, increased precision, and the integration of sensors for improved feedback and adaptability. Modern robots, often classified as sixth-generation or beyond, leverage advanced technologies like artificial intelligence and machine learning to perform increasingly complex tasks with minimal human intervention. They can adapt to changing environments, learn from experience, and even collaborate effectively with human workers.
Industries Benefiting from Programmable Robots
The introduction of programmable robots revolutionized numerous industries. Their ability to perform repetitive, precise tasks with high speed and consistency significantly boosted productivity and reduced manufacturing costs. The following table highlights some key examples:
Industry | Robot Type | Application | Impact |
---|---|---|---|
Automotive | Articulated arm robots, SCARA robots | Welding, painting, assembly, material handling | Increased production speed, improved consistency, reduced defects, enhanced worker safety |
Electronics | SCARA robots, six-axis robots | Pick and place, circuit board assembly, testing | Higher precision, increased throughput, reduced labor costs, improved product quality |
Food Processing | Delta robots, collaborative robots (cobots) | Packaging, palletizing, material handling | Faster processing, improved hygiene, reduced waste, enhanced worker safety |
Logistics and Warehousing | Mobile robots, articulated arm robots | Order fulfillment, picking, packing, sorting | Increased efficiency, reduced operational costs, improved order accuracy, enhanced warehouse space utilization |
Sensors and Perception in Autonomous Robots
The leap from programmable robots to truly autonomous ones hinges on their ability to perceive and interact with their environment. This requires sophisticated sensor systems that provide a “real-world” understanding, allowing robots to react dynamically and make informed decisions without constant human intervention. The integration and processing of this sensory data is a complex challenge, but one crucial to unlocking the full potential of autonomous industrial robots.
Sensors provide the crucial link between the robot and its surroundings. They translate physical phenomena—light, pressure, distance—into data that the robot’s control system can understand and act upon. The effectiveness of an autonomous robot is directly tied to the quality, quantity, and integration of its sensor suite. The more comprehensive the sensory input, the more effectively the robot can navigate its workspace, avoid obstacles, and perform complex tasks with precision.
Types of Sensors Used in Autonomous Robots
Various sensor types contribute to the robot’s “perception.” Vision systems, using cameras and image processing algorithms, provide spatial awareness and object recognition. Force sensors, often embedded in the robot’s end-effector (the tool it uses), allow for precise control during tasks requiring delicate manipulation or contact, such as assembly or polishing. Proximity sensors, such as ultrasonic or laser rangefinders, detect nearby objects, ensuring collision avoidance and safe operation. Other sensors, like accelerometers and gyroscopes, provide information about the robot’s own movement and orientation. The specific combination of sensors depends on the robot’s application.
Challenges in Sensor Data Integration and Processing
Integrating and processing sensor data in real-time presents significant computational challenges. The sheer volume of data generated by multiple sensors, combined with the need for rapid analysis and response, demands powerful processing units and efficient algorithms. Data fusion—combining data from multiple sources to create a more complete and reliable picture—is particularly crucial, requiring sophisticated software to resolve inconsistencies and uncertainties. For instance, a vision system might identify an object, but a force sensor could provide additional information about its material properties or stability. Real-time processing is paramount to ensure the robot reacts quickly and appropriately to dynamic changes in its environment. Delays in processing can lead to collisions, errors, or inefficient operation.
Hypothetical Sensor System for an Autonomous Welding Robot
Consider an autonomous welding robot operating in a manufacturing plant. A robust sensor system would be vital for its safe and efficient operation. This system could incorporate:
- High-resolution vision system: This would allow the robot to precisely locate weld joints, identify the type of metal, and assess the condition of the workpiece before welding.
- Force/torque sensors in the welding torch: These would ensure consistent welding pressure and prevent damage to the workpiece or the torch itself.
- Laser rangefinders: These would provide continuous monitoring of the robot’s distance from surrounding objects, enhancing safety and preventing collisions.
- Temperature sensors: Monitoring the temperature of the welding torch and workpiece would ensure optimal welding parameters and prevent overheating.
- Safety laser scanners: These would provide a 360-degree view of the robot’s surroundings, enabling it to stop operations if a human or object enters its workspace.
The data from these sensors would be processed by a powerful onboard computer using algorithms designed to handle the complexities of real-time data fusion and decision-making. This would enable the robot to autonomously perform welds with high precision, while maintaining a safe working environment. Such a system could significantly improve efficiency and reduce the risk of human error in the welding process.
Artificial Intelligence and Machine Learning
The integration of artificial intelligence (AI) and machine learning (ML) has revolutionized industrial robotics, pushing autonomous systems beyond pre-programmed routines into realms of adaptability and intelligence. These technologies empower robots to learn from data, make decisions, and optimize their actions in dynamic environments, leading to increased efficiency, safety, and overall productivity.
AI and ML algorithms dramatically enhance the capabilities of autonomous robots by enabling them to handle complex tasks previously impossible with traditional programming. Instead of relying solely on pre-defined instructions, these robots can process real-time sensory data, learn from experience, and adapt their behavior to changing circumstances. This adaptability is critical in industrial settings where tasks often involve variability and unpredictability.
AI-Powered Features in Industrial Robots
Modern industrial robots leverage AI for a range of functionalities, improving their precision, speed, and decision-making abilities. These advancements contribute to higher throughput, reduced error rates, and enhanced safety protocols.
- Path Planning: AI algorithms, particularly those based on reinforcement learning, can optimize robot movement for maximum efficiency. This involves finding the shortest, safest, and most obstacle-free paths in complex environments, even with dynamic obstacles. For example, a robot navigating a busy factory floor can adjust its trajectory in real-time to avoid collisions with other robots or human workers.
- Object Recognition: Computer vision systems, powered by deep learning, allow robots to identify and classify objects with remarkable accuracy. This is crucial for tasks like picking and placing, quality inspection, and sorting. A robotic arm equipped with a vision system can differentiate between different parts on a conveyor belt, accurately grasp the correct one, and place it in the designated location, even if the parts are slightly different or irregularly oriented.
- Predictive Maintenance: AI can analyze sensor data from the robot itself and other equipment to predict potential malfunctions. This allows for proactive maintenance, minimizing downtime and preventing costly repairs. For example, by monitoring vibrations and motor currents, an AI system can predict when a robot’s joint is likely to fail, allowing for scheduled maintenance before a breakdown occurs.
Reinforcement Learning in Industrial Robot Optimization
Reinforcement learning (RL) is a powerful ML technique particularly well-suited for optimizing robot performance in complex industrial scenarios. RL algorithms allow robots to learn optimal behaviors through trial and error, interacting with their environment and receiving rewards or penalties based on their actions.
Consider a robotic arm tasked with assembling a complex product. Using RL, the robot can be trained to find the most efficient assembly sequence. Initially, the robot might make many mistakes, leading to inefficient movements or even failures. However, through repeated attempts and feedback from the environment (rewards for successful steps, penalties for errors), the RL algorithm gradually refines the robot’s actions, eventually converging on an optimal assembly strategy. This approach is especially valuable when the optimal solution is not easily programmed explicitly, such as in scenarios with many variables or unpredictable disturbances. The robot learns the optimal strategy through interaction, eliminating the need for explicit programming of every possible scenario.
Human-Robot Collaboration in Industrial Settings
The integration of humans and robots in industrial settings marks a significant shift from traditional automation. Instead of robots operating in isolated cells, collaborative robots, or cobots, are designed to work alongside human workers, sharing tasks and responsibilities. This paradigm shift demands careful consideration of safety, efficiency, and the overall impact on the human workforce. The benefits are potentially transformative, but careful planning and implementation are crucial for successful integration.
Human-robot collaboration (HRC) is reshaping the industrial landscape, promising increased productivity and enhanced workplace safety. However, the seamless integration of humans and robots requires a deep understanding of the inherent safety concerns and the development of sophisticated design principles for collaborative robots. The benefits extend beyond efficiency gains, impacting job satisfaction and creating new opportunities for skilled workers. Nevertheless, several challenges remain, including the need for robust safety systems and the potential displacement of certain job roles.
Safety Considerations and Design Principles for Collaborative Robots
Safety is paramount in HRC. Cobots are designed with inherent safety features, such as force limiting, speed monitoring, and power and force limiting systems. These features minimize the risk of injury should a collision occur between a human and a robot. Design principles emphasize intuitive interfaces and easy-to-understand control systems, enabling human operators to easily interact with and supervise the cobot. Risk assessments are crucial before deployment, identifying potential hazards and implementing appropriate safety measures. This might include physical barriers, safety mats, or light curtains to create designated collaborative zones. Regular maintenance and safety checks are also essential to ensure continued safe operation. Furthermore, comprehensive training programs for human workers are vital to ensure they understand how to interact safely with the cobots and to recognize potential hazards.
Benefits and Challenges of Integrating Humans and Robots in Shared Workspaces
The benefits of HRC are numerous. Increased productivity is a key advantage, as humans and robots can complement each other’s strengths, performing tasks more efficiently than either could alone. Robots can handle repetitive, strenuous, or dangerous tasks, freeing up human workers for more complex and creative endeavors. This can lead to improved product quality and reduced error rates. Moreover, HRC can create a more flexible and adaptable manufacturing environment, allowing for quicker response times to changing market demands. However, challenges remain. The initial investment in cobots and the necessary safety infrastructure can be substantial. Integrating robots into existing workflows requires careful planning and potentially retraining of the workforce. Concerns about job displacement also need to be addressed proactively, emphasizing the creation of new, higher-skilled jobs in areas such as robot programming, maintenance, and system integration.
Applications of Human-Robot Collaboration
The advantages of human-robot collaboration are particularly pronounced in several key industrial applications:
The following applications showcase the powerful synergy between human dexterity and robotic precision.
The rise of autonomous robots in factories is revolutionizing industrial processes, boosting efficiency and reducing waste. This increased efficiency directly impacts our environmental footprint, as explored in this insightful article on How AI is Helping to Solve Global Environmental Challenges , showing how smart tech minimizes resource consumption. Ultimately, the evolution of these robots contributes to a greener future by optimizing industrial operations and reducing overall environmental impact.
- Assembly and Manufacturing: Cobots can assist with intricate assembly tasks, handling small parts and performing delicate operations while human workers focus on more complex assembly steps requiring problem-solving and adaptability.
- Packaging and Palletizing: Robots can handle the repetitive and physically demanding tasks of packaging and palletizing, reducing strain on human workers and improving efficiency.
- Machine Tending: Cobots can load and unload parts from machines, freeing up human operators to focus on monitoring the machines and performing maintenance.
- Welding and Painting: In environments involving hazardous materials, robots can perform welding or painting tasks, reducing risks to human workers.
- Inspection and Quality Control: Robots can assist in inspection tasks, identifying defects and inconsistencies that might be missed by human inspectors.
The Future of Autonomous Robots in Industry
The relentless march of technology ensures that the future of industrial automation will be profoundly shaped by increasingly sophisticated autonomous robots. We’re moving beyond simple programmable machines to a new era of collaborative, adaptable, and intelligent systems that will redefine manufacturing and logistics. This shift will be driven by emerging technologies, resulting in a significant impact across various industrial sectors.
Emerging Technologies Shaping Industrial Automation
The next generation of industrial robots will leverage several cutting-edge technologies to achieve unprecedented levels of autonomy and efficiency. These advancements are not isolated developments but rather interconnected elements that build upon each other to create a truly transformative impact.
Swarm Robotics and Cloud Robotics
Swarm robotics, inspired by the collective intelligence of insect colonies, involves coordinating large numbers of relatively simple robots to accomplish complex tasks. Imagine a warehouse where hundreds of small, autonomous robots work together to sort, transport, and package goods with unparalleled speed and efficiency. This contrasts sharply with traditional methods relying on large, individual robots or human workers. Meanwhile, cloud robotics uses the power of cloud computing to provide robots with access to vast amounts of data, processing power, and software updates, enhancing their capabilities and adaptability. A cloud-connected robot can learn from the experiences of other robots across the globe, constantly improving its performance. This also allows for remote monitoring and control, enabling rapid response to unforeseen circumstances.
Impact on Industrial Manufacturing and Logistics
The integration of advanced autonomous robots will revolutionize industrial processes across the board. In manufacturing, robots will become more adept at handling complex assembly tasks, performing quality control checks with higher accuracy, and adapting to changing production demands. This leads to increased productivity, reduced error rates, and enhanced product quality. Logistics will undergo a similar transformation, with autonomous vehicles delivering goods efficiently and precisely, optimizing warehouse operations, and minimizing transportation costs. The use of autonomous robots in hazardous environments will reduce workplace injuries and enhance worker safety. Companies like Amazon already utilize fleets of robots in their fulfillment centers, showcasing the practical application of this technology.
A Futuristic Industrial Setting
Imagine a futuristic factory: sleek, automated production lines hum quietly, overseen by a network of intelligent robots. Large, articulated robots with advanced sensor suites perform complex welding and assembly tasks, guided by AI-powered vision systems that ensure perfect precision. Smaller, agile robots navigate the factory floor, transporting materials and components with speed and accuracy, avoiding obstacles and human workers seamlessly. These robots communicate wirelessly, sharing information and coordinating their actions to optimize the entire production process. Overhead, autonomous drones monitor the factory for anomalies, ensuring smooth operations and early detection of potential problems. In the warehouse, a swarm of small, cube-shaped robots scurries around, sorting and packaging products with incredible efficiency. These robots are powered by renewable energy sources, contributing to a sustainable and environmentally friendly manufacturing process. This integrated system, orchestrated by a sophisticated AI system, ensures optimal production, minimal waste, and enhanced safety, representing a significant leap forward in industrial automation.
Case Studies of Successful Implementations
Autonomous robots are no longer a futuristic fantasy; they’re actively reshaping industries worldwide. Their successful integration isn’t just about technological advancement; it’s about demonstrable improvements in efficiency, productivity, and safety. Examining real-world deployments offers crucial insights into their impact and potential.
The following case studies highlight the diverse applications of autonomous robots across various sectors, comparing their performance against traditional methods. We’ll see how these robots are not just replacing human workers, but collaborating with them to achieve unprecedented levels of output and precision.
Amazon’s Robotics Integration in Warehouses
Amazon’s extensive use of Kiva robots (now Amazon Robotics) in its fulfillment centers exemplifies the transformative power of autonomous robots in logistics. These robots, resembling small, automated forklifts, transport shelves of products to human workers, significantly reducing the time and effort required for order fulfillment. Instead of workers walking miles across vast warehouses, the robots bring the inventory to them. This streamlined process has led to faster order processing, reduced labor costs, and improved accuracy. A comparison of pre- and post-robot implementation data shows a substantial increase in order fulfillment speed, with some reports suggesting a doubling of throughput.
Fanuc Robots in Automotive Manufacturing
Fanuc, a leading robotics company, provides a wide range of autonomous robots for automotive manufacturing. These robots perform various tasks, from welding and painting to assembly and quality control. Their precision and speed far surpass human capabilities in repetitive tasks, leading to increased production rates and reduced defect rates. Comparing Fanuc’s robotic systems to traditional assembly lines reveals a significant reduction in production time and a marked decrease in human error. For instance, welding robots can perform consistent welds with higher precision than manual welders, resulting in stronger and more reliable car parts.
Autonomous Mobile Robots (AMRs) in Healthcare
AMRs are increasingly utilized in hospitals and healthcare facilities to automate tasks like medication delivery, sample transportation, and supply chain management. These robots navigate complex environments autonomously, avoiding obstacles and delivering items efficiently. This reduces the workload on healthcare staff, allowing them to focus on patient care. Comparing the efficiency of AMR-based delivery systems with traditional manual methods shows a reduction in delivery times, improved accuracy in medication dispensing, and a decrease in the number of delivery errors. For example, a study showed that AMRs could deliver medication 30% faster than manual delivery.
Case Study Table
Company | Industry | Robot Application | Results |
---|---|---|---|
Amazon | Logistics | Warehouse order fulfillment | Increased order fulfillment speed, reduced labor costs, improved accuracy |
Fanuc | Automotive Manufacturing | Welding, painting, assembly, quality control | Increased production rates, reduced defect rates, improved precision |
Various AMR providers (e.g., Aethon, Vecna) | Healthcare | Medication delivery, sample transportation, supply chain management | Reduced delivery times, improved accuracy, decreased workload on staff |
Concluding Remarks
The evolution of autonomous robots in industrial applications isn’t just a technological advancement; it’s a fundamental shift in how we work and produce. From early programmable machines to the AI-powered collaborators of today, the journey has been remarkable. The future promises even more seamless human-robot partnerships, driven by breakthroughs in AI, swarm robotics, and cloud technologies. This isn’t just about faster production lines; it’s about creating safer, more efficient, and ultimately, more innovative workplaces. The possibilities are endless, and the ride is just getting started.