How 3D Printing is Changing the Manufacturing Landscape? It’s a question that’s shaking up industries worldwide. Forget clunky assembly lines and mass-produced uniformity – 3D printing is ushering in an era of hyper-personalization, on-demand manufacturing, and design freedom previously unimaginable. From rapid prototyping that slashes development time to the creation of intricate, complex parts impossible with traditional methods, 3D printing is rewriting the rules of the game. This isn’t just a technological advancement; it’s a fundamental shift in how we conceive, design, and produce goods.
This revolution is fueled by advancements in material science, allowing for the creation of parts with specific properties tailored to unique applications. Industries from aerospace and automotive to healthcare and consumer goods are embracing this technology, leading to increased efficiency, reduced waste, and the exciting possibility of mass customization. But the journey isn’t without its hurdles. We’ll delve into the challenges and explore the future trajectory of this transformative technology, painting a picture of a manufacturing landscape irrevocably altered by the power of 3D printing.
The Rise of 3D Printing in Manufacturing
3D printing, also known as additive manufacturing, has transitioned from a niche technology to a disruptive force reshaping the manufacturing landscape. Its journey, marked by incremental advancements in printing technology and material science, has paved the way for its widespread adoption across diverse sectors. Early iterations were slow and limited in material choices, producing primarily prototypes. Today, however, high-speed, high-precision 3D printers capable of handling a wide array of materials are commonplace, driving a paradigm shift in how products are designed and manufactured.
The increasing adoption of 3D printing stems from several key factors. Falling hardware costs have made 3D printers more accessible to small and medium-sized enterprises (SMEs), allowing them to compete with larger manufacturers. Simultaneously, advancements in software and design tools have simplified the process, making 3D printing more user-friendly. The demand for customized products and shorter production runs, particularly in niche markets, has further fueled its growth. Industries like aerospace, healthcare, and automotive are embracing 3D printing for its ability to create complex geometries and lightweight parts, leading to improved performance and reduced material waste.
Advantages of 3D Printing over Traditional Manufacturing
3D printing offers significant advantages over traditional subtractive manufacturing methods like milling or casting. These benefits extend across several key areas, impacting speed, cost-effectiveness, material usage, and design flexibility. The following table highlights these differences:
Feature | 3D Printing | Traditional Manufacturing |
---|---|---|
Speed | Faster for prototypes and low-volume production; slower for mass production. Rapid prototyping is significantly faster. | Generally slower for prototypes; faster for mass production once tooling is set up. Significant setup time for tooling is a major factor. |
Cost | Lower tooling costs; higher per-unit cost for low-volume production. Cost-effective for customized or complex parts. | High tooling costs; lower per-unit cost for mass production. High upfront investment in tooling limits flexibility. |
Material Usage | Minimal material waste; only the necessary material is used. Reduces overall material costs and environmental impact. | Significant material waste; substantial amounts of material are removed during subtractive processes. |
Design Flexibility | High design flexibility; complex geometries and intricate designs are easily achievable. Enables rapid iteration and design optimization. | Limited design flexibility; complex geometries are difficult and expensive to produce. Design changes require new tooling. |
For example, the aerospace industry uses 3D printing to create lightweight, high-strength components for aircraft, reducing fuel consumption and improving performance. In the medical field, 3D printing is used to create personalized implants and prosthetics, offering a superior fit and improved patient outcomes. These examples illustrate the transformative impact of 3D printing on various industries.
Impact on Design and Prototyping
3D printing has revolutionized the design and prototyping process, shifting it from a linear, time-consuming endeavor to a rapid, iterative cycle of creation and refinement. This agility allows manufacturers to explore a wider range of design possibilities, leading to innovative products and faster time-to-market. The ability to quickly produce physical prototypes significantly reduces development costs and risk, enabling a more efficient and effective product development lifecycle.
The inherent flexibility of 3D printing empowers designers to create complex geometries and customized designs that were previously impossible or prohibitively expensive to manufacture using traditional methods. This opens doors to previously unimaginable product designs and functionalities, leading to a wave of innovation across various sectors. The freedom to iterate rapidly on designs, based on tangible feedback from prototypes, ensures products are optimized for performance, aesthetics, and functionality before mass production begins.
Rapid Prototyping and Iterative Design
3D printing drastically accelerates the prototyping process. Designers can go from digital design to a physical prototype in a matter of hours or days, drastically reducing lead times compared to traditional methods which might take weeks or even months. This speed facilitates iterative design, allowing for multiple design revisions and refinements based on testing and feedback. Imagine an automotive engineer needing to test the aerodynamics of a new spoiler design; with 3D printing, they can quickly produce several iterations, test them in a wind tunnel, and refine the design until optimal performance is achieved. This iterative approach, fueled by rapid prototyping, ensures that the final product is well-optimized and meets the desired specifications.
Complex Geometries and Customized Designs
Traditional manufacturing processes often impose limitations on the complexity of designs. Casting, molding, and machining processes struggle with intricate internal structures or highly customized features. 3D printing, however, excels at creating complex geometries and highly customized designs. The additive nature of the process allows for the creation of parts with internal channels, lattices, and other features impossible to achieve through subtractive manufacturing. For example, a medical device manufacturer might use 3D printing to create a custom-fit prosthetic limb with intricate internal structures for improved comfort and functionality. This level of customization was previously unattainable, leading to less effective and less comfortable prosthetics. The ability to tailor designs to individual needs significantly improves product performance and user experience.
Industry Applications and Benefits
Several industries are leveraging 3D printing for design innovation. In the aerospace industry, 3D printing is used to create lightweight, high-strength components with complex internal structures, improving fuel efficiency and performance. The automotive industry uses 3D printing to rapidly prototype new parts and create customized interior features. The medical industry utilizes 3D printing to produce personalized implants and surgical tools, leading to improved patient outcomes. For instance, surgeons can use 3D-printed models of a patient’s anatomy to plan complex surgeries, significantly reducing risks and improving surgical precision. In the consumer goods industry, 3D printing enables the creation of highly customized products, catering to individual preferences and needs. The benefits across these sectors include reduced development time, lower production costs, improved product performance, and increased design flexibility.
Material Science and Advancements: How 3D Printing Is Changing The Manufacturing Landscape
The world of 3D printing wouldn’t be what it is today without the incredible advancements in material science. The ability to create objects layer by layer hinges entirely on the properties and capabilities of the materials used. From the humble beginnings with basic plastics, the range of printable materials has exploded, opening up exciting new possibilities across various industries.
The development of new materials and the refinement of existing ones are constantly pushing the boundaries of what’s possible with additive manufacturing. This evolution isn’t just about creating more options; it’s about improving strength, durability, biocompatibility, and cost-effectiveness, making 3D printing a more viable and attractive solution for a wider array of applications.
Material Compatibility in 3D Printing
A diverse range of materials are now compatible with various 3D printing technologies. Thermoplastics like ABS and PLA remain popular choices due to their ease of use and relatively low cost. However, the field has expanded significantly to include:
- Metals: Aluminum, titanium, stainless steel, and even precious metals like gold and silver can be 3D printed using techniques like Selective Laser Melting (SLM) and Electron Beam Melting (EBM). This allows for the creation of intricate metal parts with complex geometries, impossible to achieve through traditional subtractive manufacturing methods. Imagine creating a lightweight, high-strength titanium component for aerospace applications – this is now a reality thanks to 3D printing.
- Ceramics: Materials like alumina and zirconia are used for applications requiring high temperature resistance and exceptional hardness. Think of creating highly durable components for industrial machinery or specialized medical implants.
- Composites: Combining different materials, such as polymers and carbon fibers, allows for the creation of parts with enhanced strength-to-weight ratios. This is particularly beneficial in industries like automotive and aerospace, where weight reduction is crucial.
- Biocompatible Materials: The ability to print with biocompatible polymers and resins opens doors to creating customized medical implants, prosthetics, and surgical tools. The precision and customization offered by 3D printing are revolutionizing the healthcare industry.
- Elastomers: Flexible and elastic materials are increasingly used for applications requiring flexibility and shock absorption. Think of creating soft robotics components or customized footwear insoles.
Advancements in 3D Printing Materials, How 3D Printing is Changing the Manufacturing Landscape
Recent advancements are focusing on improving existing materials and developing entirely new ones with enhanced properties. For instance, research into high-temperature polymers is expanding the applications of 3D printing in industries like aerospace and automotive. The development of self-healing polymers is also a significant step forward, potentially leading to more durable and long-lasting products. Furthermore, advancements in bioprinting are paving the way for creating complex tissue structures and organs for transplantation, representing a groundbreaking achievement in regenerative medicine.
Comparison of 3D Printing Material Properties
Choosing the right material for a 3D printing project depends heavily on the specific application and required properties.
- Strength: Metals generally offer the highest strength, followed by composites and some specialized polymers. Thermoplastics like PLA and ABS are relatively less strong but suitable for many applications.
- Durability: The durability of a 3D printed part depends on factors such as material selection, printing process, and post-processing techniques. Materials like metals and ceramics generally offer superior durability compared to thermoplastics.
- Cost-Effectiveness: Thermoplastics like PLA and ABS are generally the most cost-effective options. Metals and specialized materials like biocompatible polymers tend to be significantly more expensive.
Manufacturing Processes and Applications
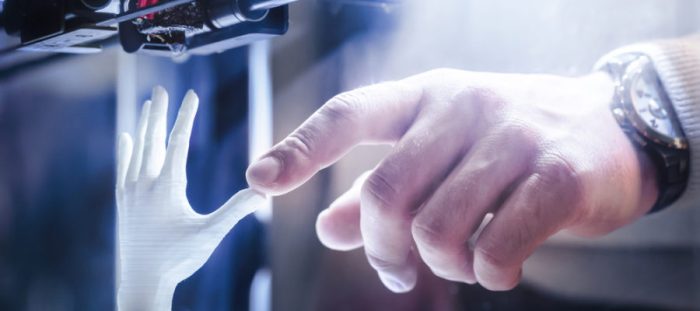
Source: proto3000.com
3D printing, or additive manufacturing, is revolutionizing how products are made, moving beyond rapid prototyping to become a core part of mainstream manufacturing. It’s impacting everything from the creation of tools to the final assembly of complex components, offering unparalleled flexibility and efficiency. This section explores how 3D printing is transforming various manufacturing processes and its diverse applications across multiple sectors.
The fundamental shift lies in the transition from subtractive manufacturing (removing material to create a shape) to additive manufacturing (building up a three-dimensional object layer by layer). This paradigm change offers significant advantages, particularly in terms of design freedom, material efficiency, and production speed, especially for complex geometries or low-volume production runs.
3D printing’s disrupting manufacturing, allowing for hyper-personalized products and on-demand production. But this rapid prototyping also presents new challenges, like verifying the authenticity of parts. This is where AI steps in; check out this insightful article on The Role of Artificial Intelligence in Fraud Prevention to see how similar tech combats counterfeiting. Ultimately, AI could become crucial in ensuring the integrity of this revolutionary manufacturing process.
Additive Manufacturing and Tooling
3D printing’s impact on additive manufacturing is, naturally, profound. It allows for the creation of intricate designs that would be impossible or incredibly expensive to produce using traditional methods. The ability to create customized tools and fixtures directly from a digital design dramatically shortens lead times and reduces costs associated with outsourcing or using pre-made, often ill-suited tools. For instance, a manufacturer can quickly print specialized jigs for assembly, reducing errors and improving worker efficiency. Similarly, 3D-printed molds for casting or forming other materials offer cost savings, particularly for low-volume production, where the cost of traditional tooling would be prohibitive. This enables rapid iteration and experimentation, speeding up product development cycles.
Applications Across Diverse Sectors
3D printing’s applications span a vast range of industries. In aerospace, it’s used to create lightweight, high-strength components for aircraft and spacecraft, reducing fuel consumption and improving performance. Examples include intricate engine parts and customized brackets. The automotive industry utilizes 3D printing for prototyping, creating custom tooling, and producing end-use parts, leading to faster development cycles and more efficient manufacturing processes. Think of personalized car parts or customized interior elements. The healthcare sector benefits immensely from 3D printing’s ability to create personalized medical devices, prosthetics, and surgical implants, improving patient outcomes and reducing recovery times. Examples include patient-specific bone implants or custom-designed hearing aids. Finally, the consumer goods industry leverages 3D printing for mass customization, allowing for the creation of personalized products tailored to individual customer needs and preferences, from customized phone cases to bespoke jewelry.
Efficiency, Waste Reduction, and Mass Customization
3D printing inherently improves manufacturing efficiency by reducing lead times, eliminating the need for extensive tooling, and enabling on-demand production. The process minimizes material waste compared to traditional subtractive methods, as it only uses the necessary amount of material to create the object. This translates to significant cost savings and a smaller environmental footprint. Furthermore, 3D printing facilitates mass customization, allowing manufacturers to cater to individual customer preferences without the high costs associated with traditional mass production. A company can offer a wide range of personalized products without needing to hold large inventories of pre-made items, leading to greater customer satisfaction and improved profitability. For example, a shoe manufacturer could offer customized insoles based on a customer’s foot scan, using 3D printing to create the perfect fit. This demonstrates the power of 3D printing to transform manufacturing into a more agile, responsive, and sustainable enterprise.
Supply Chain and Production Optimization
3D printing is revolutionizing manufacturing, and its impact extends far beyond the factory floor. The technology is reshaping global supply chains, offering unprecedented flexibility and efficiency. This shift is driven by the ability to produce parts on-demand, closer to the point of need, and with significantly reduced reliance on traditional, geographically constrained manufacturing processes.
The ability to decentralize production is a game-changer. Instead of relying on vast, centralized factories and complex global shipping networks, companies can leverage 3D printing to establish localized production hubs or even equip individual customers with the means to create their own components. This reduces lead times, lowers transportation costs, and enhances responsiveness to fluctuating market demands.
On-Demand Manufacturing and Decentralized Production
On-demand manufacturing, enabled by 3D printing, allows companies to produce parts only when needed, eliminating the need for large inventories and reducing waste. This is particularly beneficial for industries with fluctuating demand or those producing highly customized products. Decentralized production, facilitated by the accessibility of 3D printers, allows manufacturers to establish smaller, geographically dispersed production facilities or even empower end-users with the capability of self-manufacturing. This agility translates to faster response times to market changes and a reduced reliance on global supply chains, mitigating risks associated with geopolitical instability or natural disasters. For example, a medical device company could utilize 3D printing to produce customized prosthetics closer to patients, drastically reducing lead times and improving patient care. Similarly, a company producing spare parts for industrial machinery could strategically place 3D printers near its clients, ensuring rapid repair and minimizing downtime.
Optimizing a Manufacturing Supply Chain: A Scenario
Imagine a company that manufactures specialized agricultural equipment. Traditionally, this company relies on a global supply chain, sourcing components from various suppliers across different continents. This process is plagued by long lead times, high transportation costs, and significant inventory management challenges. By integrating 3D printing into its operations, the company can drastically streamline its supply chain. For instance, certain low-volume, highly customized components, previously sourced from overseas, can now be produced on-demand using 3D printers located closer to the assembly plants. This reduces lead times from months to days or even hours. Furthermore, the company can establish regional 3D printing hubs to produce commonly used parts, reducing reliance on distant suppliers and mitigating the risk of supply chain disruptions. The result is a more agile, resilient, and cost-effective supply chain, enabling faster product delivery, reduced inventory costs, and enhanced responsiveness to market demands. The company could even offer customized components to its clients directly, further enhancing customer satisfaction and creating new revenue streams. This scenario illustrates the transformative potential of 3D printing in optimizing manufacturing supply chains, enhancing agility, and building resilience against external shocks.
Challenges and Future Trends
3D printing, while revolutionizing manufacturing, still faces hurdles before achieving complete mainstream adoption. Its transformative potential, however, is undeniable, driven by ongoing advancements that promise to overcome existing limitations and unlock even more innovative applications. The future of this technology hinges on addressing current challenges and capitalizing on emerging trends.
The journey from prototype to mass production using 3D printing isn’t always smooth. Several factors currently hinder widespread adoption, while simultaneous breakthroughs are paving the way for a future where 3D printing becomes an even more integral part of the manufacturing process.
Current Limitations and Challenges
The current limitations of 3D printing primarily revolve around speed, scalability, material limitations, and cost-effectiveness. Production speeds for large-scale manufacturing are still slower compared to traditional methods, limiting its applicability for high-volume production runs. Scaling up production to meet large-scale demands remains a challenge, particularly in maintaining consistent quality and precision across multiple prints. The range of printable materials is constantly expanding, but it still lags behind traditional manufacturing in terms of material diversity and properties. Finally, the initial investment costs for high-quality 3D printing equipment, along with the ongoing operational costs, can be significant, especially for smaller businesses. This makes it challenging for some companies to justify the transition from established methods.
Emerging Trends in 3D Printing Technology
Significant advancements are continuously being made to address the existing challenges. Increased printing speeds are being achieved through innovations in print head technology and the use of multiple print heads working simultaneously. Resolution improvements are leading to greater detail and accuracy in printed parts, opening up new possibilities in areas requiring high precision. The development of new materials with enhanced properties, such as improved strength, flexibility, and biocompatibility, is expanding the applications of 3D printing into new sectors like medical implants and aerospace components. For example, the development of high-temperature polymers has enabled the 3D printing of more robust and durable parts for applications in extreme environments.
Projected Growth and Future Applications
Imagine a graph charting the growth of 3D printing in manufacturing. The line starts relatively flat, representing the early stages of adoption, but then curves sharply upward, indicating exponential growth over the next decade. This growth is fueled by advancements in technology and a wider acceptance of the technology’s capabilities. Future applications will extend far beyond prototyping. We can envision a future where personalized medicine utilizes 3D printing to create customized implants and prosthetics, tailored to individual patient needs. The aerospace industry could see widespread adoption for producing lightweight, high-strength components, optimizing aircraft design and fuel efficiency. The automotive industry may use 3D printing for on-demand manufacturing of customized parts, reducing inventory costs and lead times. Furthermore, the construction industry might leverage 3D printing to create complex building structures and components, leading to faster and more sustainable construction practices. This graph would visually demonstrate the transformative impact of 3D printing on various sectors, showcasing its projected dominance in a wide range of manufacturing applications. The visual representation would show a clear upward trend, with specific sectors labeled to highlight the projected growth within those industries.
Closing Summary
The rise of 3D printing isn’t just a trend; it’s a paradigm shift. Its impact on manufacturing is profound and far-reaching, promising a future where design limitations are shattered, production is decentralized, and customization reigns supreme. While challenges remain, the potential benefits are undeniable. As 3D printing technology continues to evolve, we can expect even more innovative applications and a manufacturing landscape dramatically reshaped by this powerful tool. The future is being printed, one layer at a time.